Dave Renshaw, workshop and warehouse supervisor at Allied Infrastructure Management Ltd, is seen by his colleagues as a health and safety hero because of his innovations on the shopfloor and his uncompromising attitude towards behaviours that could put his colleagues’ lives at risk. This earned him the title of Health and Safety Champion at the International Safety Awards 2019.
Features
A stickler for safety
Allied Infrastructure works on all of the UK and Ireland’s civil and military airfields undertaking all aspects of air-side and land-side airport infrastructure maintenance. The company holds a number of Highways England and highway maintenance contracts, regularly providing support and services to main contractors.
The Allied Maintenance team works within strict time constraints, security measures and critical operational requirements related to the narrow time gap during which repairs and maintenance can be done without causing major disruption to airport and highway operations. The work carried out at the workshop and warehouse which Dave Renshaw manages at the company’s headquarters in Leigh, Lancashire, is critical to the efficiency and safety of the work of his colleagues and the operation of machinery and equipment.
Dave Renshaw describes his role: “It is my responsibility to ensure that all of the machinery leaving the workshop or yard is going out in good order and on time. This includes checking that the day-to-day maintenance has been carried out and that everything is clean and working well. The plant must be roadworthy; for example, if we are towing machinery, all the lights must be working.
Making new marked walkways in the warehouse has been challenging
“I manage the day-to-day running of the business in relation to plant (machinery and vehicles) and materials. My team includes three fitters and two warehouse operatives, as well as the team of workers that the company employs to carry out maintenance, installation and repairs of the site. At any given time there could be up to 15 men working on the site. We prepare the plant for the ongoing jobs and carry out regular maintenance and servicing.
“I am also responsible for the organisation of the yard, for instance, making sure that machinery is in the appropriate position and safely parked, ready for the next job. Bearing in mind the nature and the number of vehicles and pieces of plant which we use, i.e. trailer rigs, hot and cold applied sealant machines, compressors, boilers, floor saws and electrical generators, safe parking and storage has direct safety implications for everyone working in the workshop and yard areas.
“The company runs as a 24-hour operation, so we have to make sure that we are ready for the jobs which come in every day from all over the country. That means either for that night or the following morning. I’m talking about some 160 pieces of plant to maintain and look after. Our fitters are kept very busy!”
Dave’s involvement in safety
“I have worked for Allied for 10 years and when I took on the management of the workshop, I was expected to introduce improvements to the way the workshop, warehouse and the yard operated. I had to make things run a bit smoother so the lads could get on with their job of maintaining and servicing the equipment to ensure that workflow was not disrupted in any way. That also meant making things safer here and for when our machinery and our guys are on the road or on site working.
David Renshaw, Health & Safety Champion 2019
“When you are responsible for people, you want to make sure that they are all working safely. We all have families and I want to make sure that everyone returns home safe and well at the end of every day. There have been a few incidents in the past where people could have been seriously hurt so we must do everything in our power to prevent that happening.
“Probably the riskiest situations to work in are on motorways. A few years ago, there was an incident on the M25 when our team was working behind a varioguard and an artic wagon entered the closure. We refused to work because the access wasn’t closed. The consequences could have been tragic but fortunately, no one was injured. We called the engineers working further down the road and made them aware of the situation and the closure was made safe.
“Similar risks exist on airport taxiways and runways because we have many pieces of machinery and other contractors working alongside us. If we’re resurfacing the taxiway or runway, we may have asphalters, mini diggers and lots of electrical equipment. We could have 50, 60 contractors in one area, so it can be very crowded and that carries many risks.”
Home and away
Jon Steele, general manager for Allied Infrastructure, a company entering its 25th year of business, also comments on the health and safety challenges that the company faces: “Many of our operatives work on client premises – they go out remotely in teams. They’re operating under a lot of time pressure (e.g. airport runways are closed and only free of traffic for short durations), with many pieces of high-energy equipment that move, rotate, etc.
“The biggest health and safety risk for us is sending inexperienced employees out on jobs because they are not always familiar with the dangers. Experienced guys can walk safely along the side of the road or in the airfields with the right markings, whereas someone who is inexperienced may
not understand the surrounding area risks. That’s why the effectiveness of our health and safety work depends on good communication, planning and supervision.
“This is particularly relevant at a time when the company is extending its reach internationally. Increasingly often, we receive contracts from European airfields. Our most recent job involved our machinery being sent to Brussels. We have also done work in Jersey, Guernsey, the Isle of Man, Denmark, Gibraltar and Cyprus. Our team has even worked on the Falkland Islands.”
Leading the way
Although Dave has no formal qualification in health and safety beyond his supervisory role, his commitment is reflected in the multiple health and safety innovations he has introduced on the shopfloor, including traffic management, lifting, operations and vehicle loading.
“When I began working at the yard in Leigh, we didn’t have any footpaths or walkways. Both the yard and the warehouse/workshop areas get very busy, so this was an obvious priority. I proposed and introduced footpaths through the warehouse and the workshop to segregate ourselves from other people entering the yard. The guys working in the workshop are not always aware of people walking past them. If people keep to the footpath, we know that they’re not going to be in our vicinity while we’re doing work which could be dangerous to others, such as welding.
Dave has introduced multiple health and safety innovations he has introduced on the shopfloor, including traffic management, lifting, operations and vehicle loading
“I also proposed and introduced a one-way traffic system in the yard, so people who are trying to get to the fuel tanks do not reverse on blind bends but have to drive around the yard. This makes things easier and much safer for everyone.
“We also introduced a marked footpath at the front of the staff parking area rather than behind the staff parking area where it used to be. When vehicles were reversing into the space, they were parking on the footpath, making it difficult for staff to walk on. The new footpath is much more visible and safer.
“Segregation of waste was another initiative which we put into place. We have a lot of different waste materials here, including scrap metal, builders’ waste, cardboard, flammable products, etc. which is now being recycled and disposed of in a much more environmentally friendly and safer way. We have also installed a Control of Substances Hazardous to Health [COSHH] cabinet in the workshop, which now stores all COSHH substances and aerosols safely. We have also put fire extinguishers, first aid materials including burns kits, eye washes and introduced signage at appropriate points in the workshop.”
—
Which of these initiatives gave you most satisfaction
“The lads’ reaction to these changes is what pleases me most, particularly when they accept them and work with them without grumbling or me having to remind them. They work very hard, but they are more mindful of the safety now. We now do face fit training in house for respiratory protective face masks. The lads have grown to understand that these measures have been brought in to keep them safe and healthy at work.
Dave is very pleased when his colleagues accept health and safety rules and recommendations without grumbling
“Of course, sometimes I have to challenge them, such as when they don’t wear the appropriate PPE or footwear, particularly when loading vans, or when they leave vans outside idling, or over the cleanliness of the machines. I give them advice on many parts of their jobs because I have done them myself previously. Occasionally though, I have to have a strong word with them to get the message across.
“I always challenge the guys who I see trying to manually load generators and hydraulic packs into the van. I remind them that we have an electric stacker truck and that they are all trained to use it. ‘Let the machine do the job for you. It makes it a lot easier and safer for you guys.’
“Preparing the new marked walkways was the most challenging job in terms of organisation. We only have a couple of people in the business who could do the spraying of the surfaces and we couldn’t do it during the normal working day. Our surface preparation division, which is based in Saxilby, Lincolnshire, came out of hours to prepare the floor and shot blast it. Afterwards, the painting guys came in and sprayed it. Most of the work was done over the weekend.
“In the workshop, we have a ramp which we use to move the machines and it can be very slippery when wet. So again, we improved access there by shot blasting it and then covered it with special resin and grit. Again, this work was done over the weekend with a lot of hard graft, but I think that the guys ultimately appreciate the effort made to improve their working environment and make it safer.”
A guy in the background
When asked what his reaction was when he learnt that he had received the Health and Safety Champion Award at the British Safety Council’s International Safety Awards, Dave says: “Of course, I was happy, but I’m not a limelight sort of guy. I like to be left in the background.
“The health and safety side of my work has become second nature to me. I used to work on site and have seen some horrific injuries in my time, so I instinctively pick up on danger signs when I see them. Different types of training and inductions also help you to be alert. I always tell the lads: ‘Make sure you’re safe wherever you are because you have a family, perhaps a wife and kids. If anything happens to you, it won’t just affect you but your whole family and the business, perhaps even the future of your kids.’
If someone is doing something wrong, I just go over and say: ‘Listen, don’t do it that way or do something about it, like put your boots on or don’t reverse around a corner.’”
“I’m not saying that I always followed the rule book because I didn’t, sometimes we let things slip a bit. But we should always be mindful of not putting ourselves and our people at risk and that’s what it’s all about.”
FEATURES
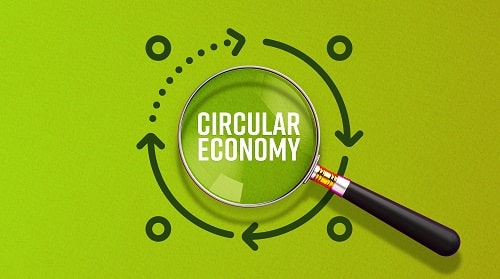
How to build circular economy business models
By Chloe Miller, CC Consulting on 07 April 2025
Widespread adoption of a circular economy model by business would ensure greater environmental and economic value is extracted and retained from raw materials and products, while simultaneously reducing carbon emissions, protecting the environment and boosting business efficiency and reputation.
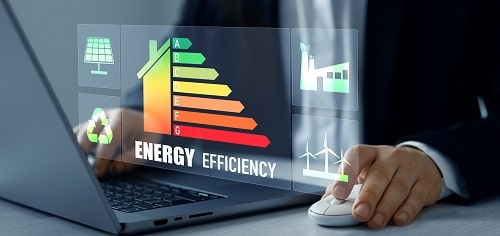
What does the first year on an accelerated net zero path have in store for UK businesses?
By Team Energy on 07 April 2025
The UK is halfway to net zero by 2050 and on a new, sped-up net zero pathway. In light of this, Graham Paul, sales, marketing & client services director at TEAM Energy, speaks to TEAM Energy’s efficiency and carbon reduction experts about the future of energy efficiency and net zero in the UK.
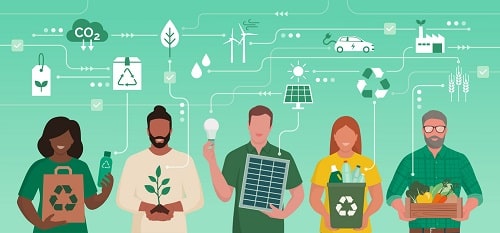
Aligning organisational culture with sustainability: a win, win for the environment and business
By Dr Keith Whitehead, British Safety Council on 04 April 2025
The culture of an organisation is crucial in determining how successfully it implements, integrates and achieves its sustainability and environmental goals and practices. However, there are a number of simple ways of ensuring a positive organisational culture where everyone is fully committed to achieving excellent sustainability performance.