Brazing is still widely used in earthing systems, despite the increased evidence of the high safety risks that it poses.
Features
Down to earth
Brazing is a metal-joining process in which two or more metal items are joined together by melting and flowing a filler metal into the joint. It is widely used to join metal conductors in high through to low voltage electrical earthing systems. This process is currently used in the UK, Ireland and many other countries worldwide, in order to create a permanent joint of two conductive metals, usually copper or steel.
In the UK, this method is still used in earthing systems for substations, railways, datacentres, etc, despite the increasingly high safety risks that it poses.
With alternatives available that mitigate or even eliminate the risks involved, the question remains as to why industries don’t make the decision to change standards and legislation to reduce or, where possible, eliminate the use of brazing as a method of welding.
Exothermic welders. Photograph: Aplicaciones Tecnológicas S.A
As an alternative to brazing earth conductor metals, exothermic welding provides a versatile method that, at the same time, improves on the quality of the permanent joints. Exothermic welding uses graphite moulds to enclose the metal conductors being joined, whereby the weld occurs within the mould itself.
Albeit traditionally, exothermic welding would use flammable and explosive materials, technology has moved towards eliminating these altogether, resulting in systems with an St0 rating (non-explosive/non-flammable). With no specific storage or handling requirements, it can be used and also transported without any restrictions.
Correct personal protective equipment (PPE) is always recommended, as materials can still reach high temperatures and should be handled with care.
Brazing uses a highly explosive and flammable mix of gases, usually Oxygen-Acetylene.
Acetylene, unlike the other fuel gases used in gas welding, is potentially unstable; in either the liquid state or as a gas under pressure it may decompose violently in the absence of oxygen or air. When acetylene comes into contact with some metals – notably copper, silver and mercury – acetylides may be formed, particularly when moisture is present. Acetylides are unstable and may explode or initiate decomposition of the acetylene.
Weld of earthing tape. Photograph: Aplicaciones Tecnológicas S.A
When using Oxygen, materials are more easily ignited, burn faster, generate higher temperatures and they may be difficult or almost impossible to extinguish. Materials such as clothing, plastics and metals which do not normally burn in air may burn vigorously in an atmosphere rich in oxygen. Oil or grease may react explosively with pressurised oxygen. A room atmosphere with more than about 25 per cent of oxygen by volume can be dangerous, particularly if it is a confined space, and fatal accidents have occurred. Even in the open air, oxygen may remain trapped in clothing or hair, which can then easily be ignited, causing serious or fatal burn injuries.
Use of such high-risk materials on a widespread level puts an unnecessary level of risk on those handling, working with and transporting this equipment.
Among the risks posed by brazing equipment are:
- Fire caused by heat, sparks, molten metal or direct contact with the flame;
- Fire/burns resulting from misuse of oxygen
- Fire/explosion caused by gas leaks, backfires and flashbacks
- Burns from contact with the flame or hot metal
- Eye injuries from intense light and ultra-violet radiation, hot particles and heat
- Explosion from over-pressurisation of the equipment
- Crushing or impact injuries when handling and transporting cylinders.
Following an event in which a fatality caused by an acetylene gas explosion involving a van carrying oxy-acetylene welding equipment, HSE commissioned research to investigate foreseeable gas leak rates, vehicle ventilation and any possible vehicle modifications that may help to mitigate the explosion risk, albeit unfortunately not eliminate risks altogether.
HSE recently published a bulletin stating there is new scientific evidence that exposure to all welding fume, including mild steel welding fume, can cause lung cancer as well as limited evidence linked to kidney cancer.
Brazing requires to be in very close proximity to the metals being welded, therefore, as per the strengthening of HSE’s enforcement expectation for all welding fume, engineering controls may need to be considered or adequate and suitable respiratory protective equipment (RPE).
Exothermic welding does still pose a certain level of risk. PPE such as special gloves should be worn when handling hot materials, along with correct eye protection.
Risks in exothermic welding are:
- Splash back of materials when moisture is present
- Burns from contact with hot metal or graphite moulds
- Eye injuries from hot particles and heat.
New technologies however mitigate these risks altogether. Exothermic welding, using a remote ignition device, ensures that the person carrying out the process remains at a safe distance from the metals being welded, up to 10m away.
Safety at work always comes first in any industry, however traditional tools and technologies require updating and often new methods are either overlooked or not explored carefully enough.
Most manufacturers provide training for any products or tools in order for everyone to stay current on electrical earthing safety.
Nik Sweeting is area manager at Aplicaciones Tecnológicas S.A.
FEATURES
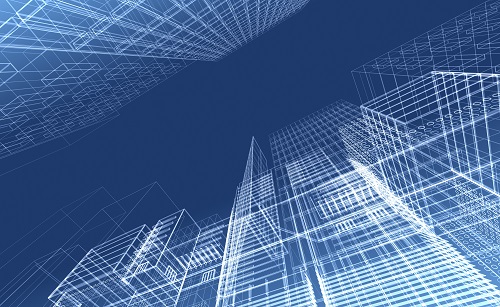
A year on – what have been the developments in competence management and the golden thread?
By Sofie Hooper, Association for Project Safety and Anthony Taylor, Resolve Risk Ltd on 03 July 2025
Last July the authors published an article in Safety Management where we looked at the expectations for those responsible for managing competence and those creating and managing the golden thread. In this edition we provide an update on both these key requirements of the Building Safety Act/Fire Safety Act’s ‘new regulatory regime’ including for higher-risk buildings (HRBs).
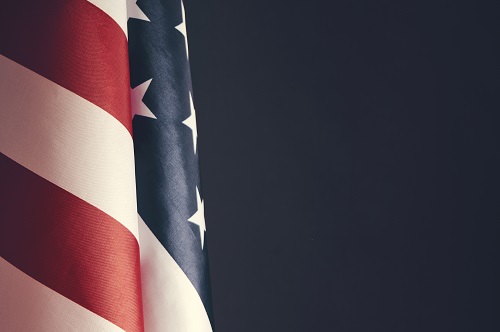
Stars, stripes and safety
By Belinda Liversedge on 02 July 2025
It seems like America today is rarely out of the news, particularly since President Trump won his second term. Our ‘special relationship’ with America has continued, with the country a strong pipeline for inspiration, products and trends.
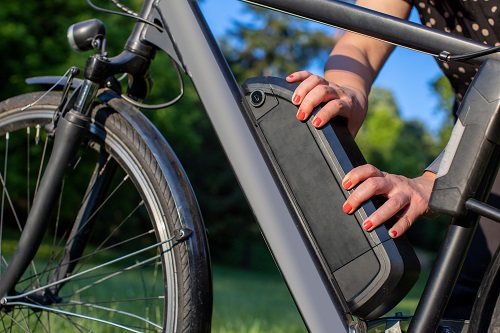
The hidden risks of lithium-ion batteries
By Adrian Simmonds, QBE Europe on 01 July 2025
With UK fire services now tackling at least three Li-ion battery fires a day, it’s clear that stronger regulation and enforcement is urgently required to prevent the sale, use and modification of poor-quality and potentially dangerous batteries used in e-bikes and scooters.