Tower scaffolds are widely used for work at height, but they must be carefully selected and only erected and used by trained and competent people.
Features
A head for heights
Scaffold towers are a familiar tool for many workers, who find them a quick and convenient way to work at height. But how do you make sure your team is protected up there? It starts with providing safe, reliable equipment.
Select safe equipment
I won’t tiptoe around it – you need a tower you can trust with your life. This isn’t the time to cut costs or pick the first item you find online. A good quality, reliable tower will provide your team with a safe working platform for years to come, so do your research.
Check it’s certified
Luckily, there’s an easy way to tell if a tower includes all the safety features you need. Simply check that it’s certified to the relevant design standard.
If it’s a mobile access tower – a straight up and down, single bay structure with four legs and wheels – it must comply with BS EN 1004. If it’s another configuration of tower, such as a cantilever tower, the relevant standard is BS 1139-6.
Don Aers: "You need a tower you can trust with your life."
These standards tell you that a tower meets minimum safety requirements, such as:
- Purpose designed platforms with safe trapdoor entry and exit
- Built in access for safe ascent and descent
- Supplied with the correct size and quantity of stabilisers to prevent overturning
- Has the correct quantity and number of guardrails and toe-boards with the correct gaps and dimensions to prevent a person or object falling.
BS EN 1004 is being updated soon and BS 1139-6 is under review, so this is a great time to specify their use in your organisation.
Choose a reliable brand
PASMA is the voice of authority on access towers. Our members come from across the industry, including manufacturers, hire centres and training companies. They have one thing in common – a commitment to raising tower safety standards.
If you choose towers that have been manufactured by PASMA members you’ll know they prioritise your safety above all else. It’s a condition of membership that their towers meet the most up-do-date standards and are independently certified. If you’re renting a tower, using a PASMA hire centre will provide the same reassurance.
Use it safely: training for your team
Even a certified tower is only safe if it’s assembled, inspected, used and dismantled by competent workers. Anyone working with a mobile access tower should have passed a PASMA Towers for Users training course within the last five years and we recommend their managers and supervisors complete PASMA Towers for Managers.
Even a certified tower is only safe if it’s assembled, inspected, used and dismantled by competent workers
Additional training is needed for anything other than a simple BS EN 1004 mobile access tower. There’s a growing range of BS 1139-6 tower configurations available, with a corresponding PASMA training course for each of them:
- Cantilever towers
- Towers on stairways
- Towers with bridges
- Linked towers
- Large deck towers.
If it’s not practical to have your own workers trained, or if you need a non-standard tower designed for your site, you can use a PASMA ‘Hire & Assembly’ Member. Their qualified Access Tower Specialists will assemble and dismantle the tower for you.
Use it safely: follow the instruction manual
Even though the person assembling the tower must be trained, they must always have, and follow, the instruction manual provided by the manufacturer or hirer. It must be available on site as it contains critical safety information, including:
- How to assemble the tower without ever standing on an unprotected platform
- The bracing pattern, which gives the tower its strength and must be followed exactly
- The maximum safe working load
- Information about hazards.
Following the manual is the only way to ensure the tower has all the strength, stability and safety features that its manufacturer intended.
Don’t forget the tower needs to be inspected before use and a report of the inspection (normally in the form of a PASMA inspection record attached to the tower) available on site and kept for three months after.
Preparing for new standards
For the smoothest possible transition to new tower standards, PASMA recommends taking the time now to review your company’s purchasing policy to ensure it specifies that any towers you’re buying or hiring must be certified to the latest version of:
- BS EN 1004 (mobile access towers); or
- BS 1139-6 (cantilever towers, towers on stairways, towers with bridges, linked towers and large deck towers); or
- BS 8620 (low level work platforms, also known as podiums).
Make sure you’re only using towers that meet these standards, and if you aren’t, update your fleet at the earliest opportunity.
It is also essential to regularly inspect any towers you currently own to ensure they’re in good working condition. If they are, you won’t need to replace them even when the standards change. When they need replacing or if you’re buying additional towers, make sure they meet the latest version of the standard.
BS EN 1004:2020
We expect BS EN 1004:2020 to be published later this year and the old version to be withdrawn 12 months afterwards. The year in between is a transition period.
Having followed the advice in this article, you’ll be ready to seamlessly adopt the new standard when it comes into effect. In the meantime, you have the reassurance of knowing that your workers are using safe towers for every job.
PASMA will be providing regular updates on the implementation of BS EN 1004 and producing detailed guidance on its implications for tower users, including for health and safety practitioners.
Register for the updates at: pasma.co.uk/en1004
Don Aers is Technical director at PASMA
FEATURES
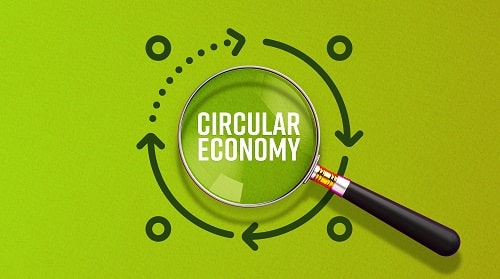
How to build circular economy business models
By Chloe Miller, CC Consulting on 07 April 2025
Widespread adoption of a circular economy model by business would ensure greater environmental and economic value is extracted and retained from raw materials and products, while simultaneously reducing carbon emissions, protecting the environment and boosting business efficiency and reputation.
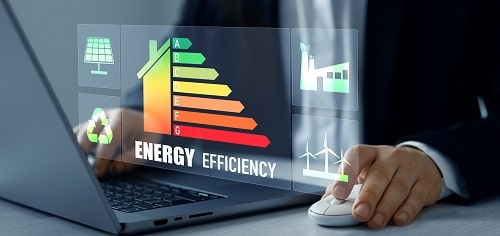
What does the first year on an accelerated net zero path have in store for UK businesses?
By Team Energy on 07 April 2025
The UK is halfway to net zero by 2050 and on a new, sped-up net zero pathway. In light of this, Graham Paul, sales, marketing & client services director at TEAM Energy, speaks to TEAM Energy’s efficiency and carbon reduction experts about the future of energy efficiency and net zero in the UK.
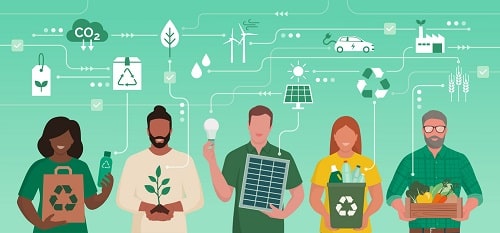
Aligning organisational culture with sustainability: a win, win for the environment and business
By Dr Keith Whitehead, British Safety Council on 04 April 2025
The culture of an organisation is crucial in determining how successfully it implements, integrates and achieves its sustainability and environmental goals and practices. However, there are a number of simple ways of ensuring a positive organisational culture where everyone is fully committed to achieving excellent sustainability performance.