Dangerous substances can and do put people’s safety at risk. Find out how to handle them.
Features
How to handle flammable liquids and other dangerous substances
Dangerous substances, if not properly controlled, cause harm to people as a result of fire or explosion or corrosion to metal. They can be found in nearly all workplaces and include such things as solvents, paints, varnishes, flammable gases and dusts.
The European Directive 99/92/EC (ATEX 137 or the ATEX Workplace Directive) refers to minimum requirements for improving the health and safety protection of workers at risk from explosive atmospheres. In the UK the directive was implemented under the Dangerous Substances and Explosive Atmospheres Regulations (DSEAR) 2002, which place a duty on employers and the self-employed to protect people from these risks to their safety in the workplace, and to members of the public who may be put at risk by work activity.
The DSEAR requires employers to:
- Find out what dangerous substances are in their workplace and what the risks are
- Put control measures in place to either remove those risks or, where this is not possible, control them
- Put controls in place to reduce the effects of any incidents involving dangerous substances
- Prepare plans and procedures to deal with accidents, incidents and emergencies involving dangerous substances
- Make sure employees are properly informed and trained to control or deal with the risks from the dangerous substances
- Identify and classify areas of the workplace where explosive atmospheres may occur and avoid ignition sources (from unprotected equipment, for example) in those areas.
The regulation is supported by an Approved Code of Practice (ACOP) and guidance issued by the Health and Safety Executive (HSE) and provides really useful advice on how to comply with the regulation and covers design, storage, control and safe maintenance.
Organisations need to put controls in place to reduce the effects of any incidents involving dangerous substances. Photograph: iStock/Milos Dimic
Following the guidance is not a legal requirement or compulsory, unless specifically stated, and you are free to take other actions. Having said that, if you do read and follow them, you will normally be doing enough to comply with the law. It is worth noting that health and safety inspectors seeking to secure compliance with the law may refer to this guidance.
With specific regard to the storage of flammable liquids, regulations state that:
“Fire resisting storerooms and fire resisting workrooms should provide a minimum of 30 minutes fire resistance in respect of integrity, insulation and where applicable; load bearing capacity.”
The exception to this is when the storeroom or workroom is within a building that also contains residential accommodation, in which case the partition between the two should provide a minimum of 60 minutes fire resistance to comply with the law.
Fire resisting cabinets or other enclosures should provide a minimum of 30 minutes fire resistance in respect of integrity, except where provision is made for explosion relief. Fire resisting cupboards and bins should provide a minimum of 30 minutes fire resistance in respect of integrity, except where provision is made for explosion relief and/or ventilation to comply.
There are several more demanding standards and design specifications which refer to the fire performance of the complete cabinet structure, including:
- BS EN 14470-1:2004 ‘Fire safety storage cabinets – Part 1: Safety storage cabinets for flammable liquids’
- Factory Mutual, Underwriters Laboratories and ANSI/NFPA 30 standards.
Flammable substances need to be kept in the correct type of storage unit
Where standards go beyond the minimum requirements of the law, their implementation in the UK is not a legal requirement. However, for quantities in excess of the recommended maxima, employers/dutyholders may find that cabinets with enhanced fire performance help in making their risk assessment demonstration.
When considering the external storage of flammable liquids, there are strict adherences concerning separation distances. This is the distance the flammable liquids must be stored from occupied buildings, boundaries, process units, flammable liquid storage tanks and/ or sources of ignition.
Larger fire rated storage units designed for the storage of drums and or IBC of flammable liquids typically use non-combustible inter-locking steel-clad fire resistance panels in their construction and the fire rating will be shown in minutes; such as REI 60, 90, 120 or 240, to indicate the time the performance criteria has fulfilled during a standardised fire test.
R = Load bearing capacity – The load bearing capacity is the ability for a building element to resist a fire when exposed on one or several sides and when supporting an external load during a time period without losing its stability
E = Integrity – The integrity is the ability of a test sample when exposed to fire on one side, to prevent the passage through it of flames and hot gases and to prevent the occurrence of flames on the unexposed side
I = Insulation – The insulation is the ability of a test sample when exposed to fire on one side, to restrict the temperature rise of the unexposed face to below specified levels.
These fire rated storage units can provide a practical solution when the separation distance criteria cannot be met and have the advantage of being relocatable (normally positioned by forklift truck or crane dependent on their size); allowing you to reposition them if and when circumstances change within your operation.
Questions worth considering:
- Is there good natural air movement in and around where the flammable substances are stored and used? If not, you may have to consider mechanical air changes. Good ventilation will mean that any vapours given off from a spill, leak, or release will be rapidly dispersed.
- Have all the obvious ignition sources been removed from the storage and handling areas? You need to think outside the box as an ignition source can be very varied: sparks from electrical equipment, welding or cutting tools, hot surfaces, open flames, static charge, etc. An explosion can even be caused by the simple action of decanting a flammable liquid from one container to another if they have not been earthed.
- Are your flammable substances kept in the correct type of storage unit? Check the distance from the unit or proposed site of the unit to occupied buildings, boundaries, process units, flammable liquid storage tanks and or sources of ignition.
- Does it need to be fire rated? As previously stated, if you can’t meet the separation distance relevant to the volume of liquid you are storing you will need to use a fire rated unit.
- If there is a spill will it be contained and prevented from spreading? Consider what will happen if the liquid spills out of the bunded storage unit.
- Can you replace a flammable substance for a less flammable one, or can you eliminate it from the process completely? Processes and products evolve, check with your supplier to see if they have alternatives, including a non-flammable one; and/or research the possibility of redesigning your process to make it safer.
- Are your flammable substances stored and used in a different area to other substances and processes? By separating them you will lessen the risk of an incident and improve workplace safety. Flammable liquids should be stored separately from other dangerous substances that may enhance the risk of fire or compromise the integrity of the storage unit; for example, energetic substances, oxidizers and corrosive materials. Sometimes these other dangerous substances may be flammable liquids in their own right or held in a flammable liquid. However, it is still inappropriate to store these in the same cabinets or bins with other flammable liquids.
Overview
In the event of an incident, the objective is to ensure that people can safely escape from the working area. In this context, the purpose of storing dangerous substances in the appropriate storage unit is to provide a physical barrier to delay the involvement of the stored liquids in a fire and provide sufficient time for people’s safe evacuation and the immediate implementation of emergency procedures.
It’s important not to overlook any aspect associated with the safe handling of flammable liquids such as static discharge during filling/decanting, combustion due to excessive heat build-up, potential ignition sources such as a spark from a tool or electrical component and pressure build-up in a container.
Insurance providers and the local authority fire brigade will also have valuable insight that could save you time and money going forward. Also, you might want to consider the services of an outside company to assess/review your site; as an outside pair of eyes will often see things that have become commonplace to you.
Andrew Lawrence is group coordination manager at Empteezy
FEATURES
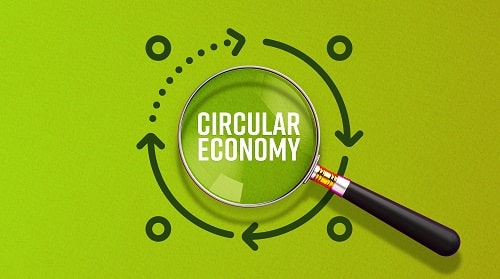
How to build circular economy business models
By Chloe Miller, CC Consulting on 07 April 2025
Widespread adoption of a circular economy model by business would ensure greater environmental and economic value is extracted and retained from raw materials and products, while simultaneously reducing carbon emissions, protecting the environment and boosting business efficiency and reputation.
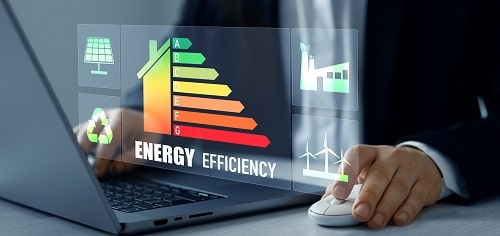
What does the first year on an accelerated net zero path have in store for UK businesses?
By Team Energy on 07 April 2025
The UK is halfway to net zero by 2050 and on a new, sped-up net zero pathway. In light of this, Graham Paul, sales, marketing & client services director at TEAM Energy, speaks to TEAM Energy’s efficiency and carbon reduction experts about the future of energy efficiency and net zero in the UK.
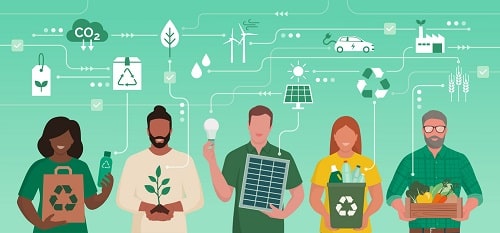
Aligning organisational culture with sustainability: a win, win for the environment and business
By Dr Keith Whitehead, British Safety Council on 04 April 2025
The culture of an organisation is crucial in determining how successfully it implements, integrates and achieves its sustainability and environmental goals and practices. However, there are a number of simple ways of ensuring a positive organisational culture where everyone is fully committed to achieving excellent sustainability performance.