When hiring workplace transport equipment operators like forklift drivers, it’s vital to know how to check the validity of their training certificates.
Features
Check them out
If you’re one of the many employers whose business involves workplace transport operations, then you’d ideally like peace of mind knowing that every new driver or agency worker will have the correct skills for the job. But just how confident are you in that being the case? Do you know what to look
for to see if their training is accredited? Did you know to look for accreditation?
Training certificates for operators of mobile plant and equipment – such as forklifts, reach trucks, telescopic handlers and excavators – are often taken on face value and accepted as ample evidence that the person presenting them is at the required level of competency. Operators are frequently taken at their word without a thorough validation process being undertaken.
This may be because the recruiter didn’t fully understand the certificate the operator presented, or the employer didn’t know how they should be checking it. But if your new recruit is not actually as competent as you assume, there is a much higher risk of them being involved in a serious accident – putting other people in danger and creating major problems for your company.
But how do you verify the training of someone who operates workplace transport equipment – whether it be a lift truck, sideloader machine, vertical stock picker or any other type of plant or machine? Where do you start?
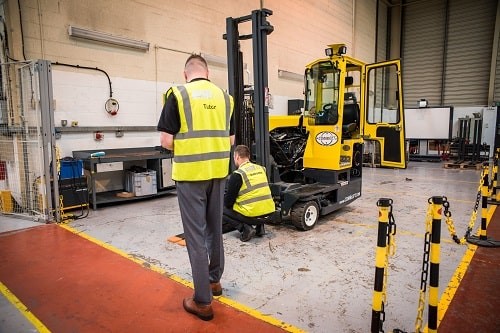
Always check the accreditation
AITT (The Association of Industrial Truck Trainers) is one of the leading accrediting bodies for workplace transport training and is part of the Accrediting Bodies Association – Workplace Transport (ABA).
Working with an accrediting body like AITT can make it easier to get support and answers if there is any uncertainty over the validity of an operator’s certificate.
The first thing we would advise you to look for is proof of accreditation from one of the ABA awarding bodies: AITT, ITSSAR, NPORS or RTITB.
Training certificates issued to operators should have a unique reference number issued by one of these awarding bodies to signify that the company or individual instructor who delivered the training has undergone an external audit by the relevant awarding body and found to be delivering the training to the required standard.
Each number – and the related individual certificate – should be linked to the accrediting body’s operator registration scheme. In the case of AITT we use a system called ACORNS (AITT Certification of Operator Registration Numbers Scheme). It is our database of all AITT-accredited training delivered by registered providers. If you need to check the legitimacy of a workplace transport operator’s training certificate, you can contact AITT quoting the ACORNS number from the certificate. If it is not on our database, then the certificate is not accredited.
You shouldn’t fret about whether or not to challenge a certificate if you have any doubt whatsoever. It’s important to catch any potential problems as early as possible to reduce the chance of serious issues arising later. Systems like ACORNS help take the uncertainty out of recruitment.
Categories and codes
Trucks are categorised into 14 ABA workplace transport groupings based on size and function. For example: pedestrian and rider pallet trucks (category A), counterbalance trucks (category B) and sideloaders (category C).
But truck categorisation is another fundamental area where awareness and knowledge are frequently lacking. Different types of trucks will require different types of training, and there can be a lot of confusion over which category contains which truck.
People can assume that an operator’s qualification covers several different types of truck when that may not be the case. Even if some truck types appear fairly similar to you, they can have quite specific control differences that change how they operate, meaning separate training is needed for each.
Knowing the correct ABA workplace transport codes is incredibly useful during the recruitment process. When advertising for an operator the employer can include the relevant codes for the various truck types that will be used on site rather than just broad terms like ‘picker’. This allows potential applicants to compare their qualifications with the employer’s requirements – and allows the employer to ascertain whether conversion training would be needed.
For more information about the codes visit: www.aitt.co.uk/news/bringing-industry-up-to-code
Advice from experience
The recent online AITT conference, ‘The key to effective training’, touched on some of these important issues. Attendees heard from the Health and Safety Executive – along with guest speakers from companies that employ workplace transport operators – who shared what they had learned and offered key tips and advice on ensuring better, more effective operator training.
Gary Rowland, group compliance training manager at nationwide food distributor Greencore, talked about the challenges faced at one of Greencore’s sites. By working with an accredited training body to ensure an industry-standard training framework and bringing in a rigorous operator auditing system, driver competency levels were raised and site impacts were reduced by 50 per cent. He stressed the importance of continuous improvement and why training and development for machine operators should extend beyond the classroom.
Simon Ambridge, risk and compliance manager at drinks wholesaler Matthew Clark, talked about the ways operators can be better engaged in both their training and ways of ensuring they continue to safely operate their mobile machines and plant. He discussed the importance of getting operator feedback in order to see how they felt about the training and how they were subsequently applying the knowledge learned on the job. This allowed Matthew Clark to assess how well the training was working and formulate more effective action plans for follow-up training.
The AITT online conference is available to watch in full on demand. For more information see: www.aitt.co.uk/news
Take safety seriously
It will always be in your best interest to ensure employees have the correct type of training for their job, from trainers you know have been assessed to the high standards of the ABA. Not only will it give you better reassurance that your employees are working correctly, but it shows
your employees that you are taking their safety journey seriously.
For more information see:
www.aitt.co.uk
T. 01530 810867
Adam Smith is managing director of The Association of Industrial Truck Trainers (AITT).
FEATURES
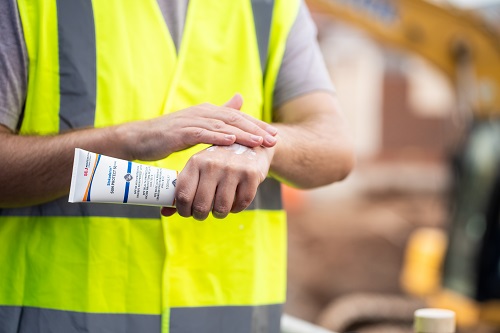
Facing the facts: protecting your outdoor workforce from UV exposure and skin cancer
By SC Johnson Professional on 11 July 2025
With outdoor workers at significant risk of skin damage, ageing and cancer due to exposure to the sun’s UV rays, it’s essential that employers in sectors like construction and agriculture create a working environment where sun safety precautions become the norm, rather than the exception.
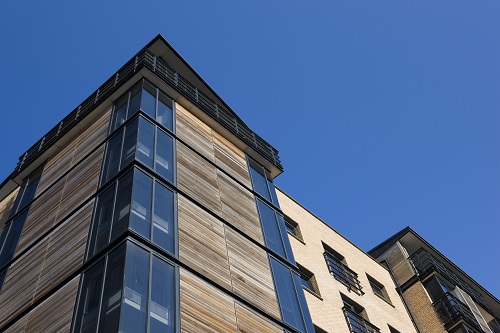
2025 UK fire safety regulation updates: a quick guide
By Chloe Miller on 11 July 2025
The regulatory landscape covering fire safety arrangements and structural features in domestic and commercial buildings has undergone a number of significant changes in recent years, making it essential for responsible persons to review their approach to keeping residents, workers and the nearby public safe from the risk of fire.
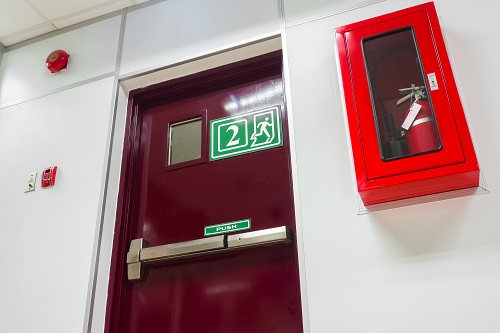
Tackling new fire risks as Fire Door Safety Week celebrates 12th year
By Helen Hewitt, British Woodworking Federation on 11 July 2025
The British Woodworking Federation’s annual Fire Door Safety Week this September will encourage duty holders such as those in charge of residential buildings to consider the dangers from lithium-ion batteries and ensure fire doors remain fit for purpose in reducing the risk should a battery-related fire break out.