Slips, trips and falls on the same level are the most common cause of injury at work, but there are practical ways of preventing them.
Features
Don’t slip up on safety
Slips, trips and falls on the same level are the most common cause of workplace injuries, with the most recent annual statistics revealing nearly 700,000 cases.
Seventy per cent of health and safety professionals believe that good quality, slip-resistant footwear is enough to keep their people safe, but the reality couldn’t be further from the truth.
Additional factors, such as the range of floor types, level of floor degradation, floor maintenance regimes and any containments on the floor surface, will contribute to slip risks.
The Pendulum method of testing a floor’s slip resistance is the only method recognised in a UK court of law. Floor surface testing during 2018/19 showed that, of the 511 tests completed, 350 failed to achieve a safe standard of slip resistance.
In some cases, a floor’s slip resistance was so poor, it would have an accident probability as high as one in two¹. Without sufficient measures in place, employees and members of the public are being put at unnecessary risk of injury. Businesses, meanwhile, face the threat of prosecution and reputational damage, with slips, trips and falls costing employers more than £500 million each year.
Reducing the risk of slips, trips and falls
It’s critical that health and safety professionals take a holistic approach to slip prevention, considering:
- Floor type, such as tile, vinyl, laminate or concrete
- Friction compromised by spilled liquids or poor cleaning regimes
- Footwear type and level of slip resistance.
The majority of slips occur when floors are contaminated with water, oil, food, debris or dust. Even the smallest amount of contamination can pose a major slip risk on floors with a smooth surface, such as glazed ceramic tiles or varnished wood.
When considering the floor type, health and safety professionals must also consider how much the floor has degraded because trips generally take place on damaged, uneven or poorly laid surfaces. To minimise hazards, cleaners and supervisors should be encouraged to report any defects or unmarked changes, such as a missing tile or a curling mat – this could be done within the near miss reporting process.
The Pendulum test can be used to measure the slip potential of dry, wet and contaminated flooring. As the only test used in enforcement and prosecution, passing the test can not only improve safety but provide critical defence against potentially lengthy court cases, personal injury claims and higher insurance premiums. However, to ensure accurate results, the test should only be conducted by a trained operative who understands how to use the test and its data.
Choosing the correct cleaning regime
To effectively remove contaminant, the correct cleaning regime needs to be selected. For example, detergent is essential if there is grease or oil, while mopping is usually only effective on smoother floors because it only skims the floor surface. Operatives must also consider other hazards in the working environment. For instance, a sweeping brush can create airborne dust and therefore should not be used when there are dust-related risks to health such as sawdust.
Selecting anti-slip products for existing flooring
Businesses should select products specifically designed to help prevent slips, trips and falls, such as floor waxes developed to ensure they are hard-wearing and slip-resistant.
Slippery areas, such as toilets and showers, can be coated with grit to create non-slip surfaces. In addition, matting can reduce the risk of slipping on potentially treacherous surfaces and, in some cases, provide fatigue relief for standing operatives. For example, slip-resistant matting can help prevent slip injuries by providing more underfoot grip on floor areas contaminated by water, liquids and oil. Entrance matting, on the other hand, can help prevent dirt and water from being tracked onto floors, minimising potential slip hazards.
Health and safety professionals should also consider the impact of physical fatigue on staff members. Standing for long periods of time on hard floor surfaces is uncomfortable and can cause tiredness which reduces concentration, increasing the likelihood of a slip or trip.
Anti-fatigue matting is a simple method that employers can introduce to help to decrease foot weariness and the risk of slips, trips and falls. The built-in cushioning helps promote regular subtle foot movement, reducing stress on the soles of the feet and distributing the pressure over a greater surface. The cushioning underlay also insulates the feet from hard surfaces, cold floors, vibrations, moisture and sound.
Keeping the workforce standing tall
It’s critical that employers carry out a slip risk assessment, review the floor types and quality and ensure their floor cleaning regime is correct. By implementing safety measures, employees will be given the best possible chance of getting home safely at the end of the working day.
For more information about Arco’s anti-slip campaign and how to address slip risks, see: www.dontslipup.co.uk
Neil Hewitt is Director of QSHE UK and Asia at Arco.
References
1) 1,300 independent slip risk assessment studies conducted by Bonasystems in 301 locations across the UK. Accident probability is given based on the correlation to the Pendulum Test Values (PTV) as guided by the HSE.
FEATURES
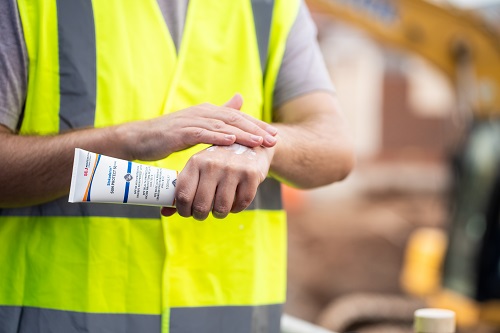
Facing the facts: protecting your outdoor workforce from UV exposure and skin cancer
By SC Johnson Professional on 11 July 2025
With outdoor workers at significant risk of skin damage, ageing and cancer due to exposure to the sun’s UV rays, it’s essential that employers in sectors like construction and agriculture create a working environment where sun safety precautions become the norm, rather than the exception.
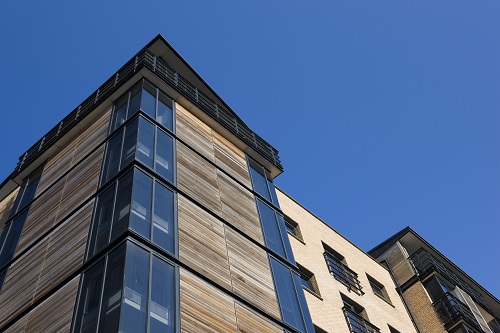
2025 UK fire safety regulation updates: a quick guide
By Chloe Miller on 11 July 2025
The regulatory landscape covering fire safety arrangements and structural features in domestic and commercial buildings has undergone a number of significant changes in recent years, making it essential for responsible persons to review their approach to keeping residents, workers and the nearby public safe from the risk of fire.
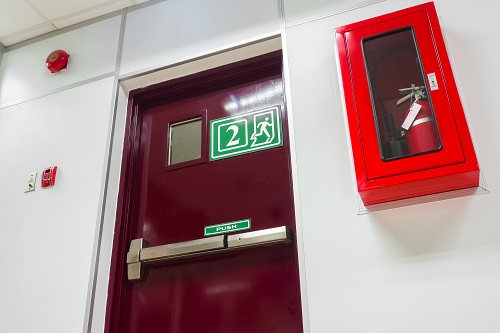
Tackling new fire risks as Fire Door Safety Week celebrates 12th year
By Helen Hewitt, British Woodworking Federation on 11 July 2025
The British Woodworking Federation’s annual Fire Door Safety Week this September will encourage duty holders such as those in charge of residential buildings to consider the dangers from lithium-ion batteries and ensure fire doors remain fit for purpose in reducing the risk should a battery-related fire break out.