People operating or working near forklift trucks can quickly become complacent about the dangers they pose, making it essential that managers and supervisors know how to spot, communicate and rectify bad practice.
Features
Forklift safety: combating complacency is key
Forklift operators often perform the same tasks day in, day out. The repetitive nature of the work and the familiar environment can lead to complacency in the workplace, and the assumption that just because an accident hasn’t happened yet, it never will.
When this attitude is combined with pressure to meet demand, many operators begin to cut corners, particularly when nearing end of shift deadlines.
Complacency can cost you
If an accident occurs, the cost implications can be severe. Aside from the devastating impact on the work team, how might it affect the business? There’s sick leave, compensation, potential court appearances, legal fees and fines (which are currently at an all-time high), not to mention reduced morale among colleagues, which can seriously impact productivity.
Photograph: FLT
Even if the incident causes no physical harm — a dropped pallet, for example — there is the potential cost of stock damage, disruption, aisle closures, clean-up and missed deadlines. Those running a business should therefore ask themselves: how many late or damaged deliveries will my customers accept before they switch supplier? Especially given the growing demand down the supply chain for faster delivery, which gives operations even less room for error.
Poor company culture and a lack of engagement with safety can dramatically increase risk, not only among forklift operators but those working alongside them on foot. Being ignorant of the dangers, or worse still, indifferent to the potential emotional and financial consequences of an accident, does not make them any less devastating.
It’s crucial that managers and supervisors are equipped to step in before bad habits become the norm. By cracking down on complacency at all levels in your workforce, an employer can protect both their staff and the company’s bottom line.
The buck stops with the employer and managers
It is of course the responsibility of the individual to perform their job safely and efficiently, but ultimately, site safety lies with managers and supervisors to uphold.
This is emphasised in the Approved Code of Practice for rider-operated lift trucks (L117), the Health and Safety Executive’s (HSE’s) definitive guide to forklift training and safe use.
While supervisors and managers don’t need to be certificated lift truck operators, they do need to understand the risks involved and how to prevent them.
In this vital role, managers and supervisors must know how to:
- Carry out an effective observation
- Recognise unsafe practice and behaviour
- Communicate effectively with operators and line managers
- Actively maintain and promote health and safety standards.
Even the best-trained teams are at risk in the long term if those overseeing operations don’t continuously encourage best practice and maintain a safe working environment, so those in supervisory roles must be able to recognise and correct any bad practice that occurs.
Communicate the risks to everyone
Forklift operators need the skills and confidence to carry out their job safely – these things should be instilled during standard operator training but must be followed up to ensure best practice continues to be applied day-to-day.
Stuart Taylor: "Combating complacency is key."
However, to ensure the workplace stays as safe as possible, businesses need to do more. As we’ve seen, those in supervisory roles have a key part to play. To allow managers to continually monitor and rectify any unsafe forklift activity, they need to know what danger signs to look out for.
And those working alongside operators on foot must not be forgotten – after all, they are most at risk of injury should a forklift accident occur. Pedestrians will be safer if they’re fully versed in the risks associated with working around forklifts and understand the importance of maintaining a safe distance. But this relies on safe practices and procedures being shared and awareness being raised across the board.
Communication and continual reinforcement of the message is key. According to a recent survey carried out by Mentor FLT Training, one in four respondents said forklift operators at their company were either not aware of the safe systems of work (SSOW) in place or didn’t comply with them. Despite often receiving basic training, we frequently see instances of how complacency and bad habits among operators can soon lead to unsafe practice — if an employer fails to identify and stop it.
There seems to be a missing link.
Too often, the safety message is lost in translation between best practice documented at senior level and what’s happening on the ground. The importance of the entire workforce always following the procedures put in place for their protection is simply not impressed upon the work team – for example, due to poor communication by managers, or a failure by managers and supervisors to regularly reinforce the forklift safety message and instructions, or to spot and correct unsafe behaviour.
To plug the gap, and steer complacent individuals (whether unaware or unconcerned of the risks) away from bad habits and poor practice, managers and supervisors must be proactive. If managers and supervisors don’t take action, it can send a message to other team members that this behaviour is OK. And it doesn’t take long for these bad habits to be adopted as common practice.
Too often, the safety message is lost in translation between best practice documented at senior level and what’s happening on the ground. Photograph: iStock
Effective ways to monitor operations
On average, lift trucks are involved in a quarter of all workplace transport accidents. As the HSE regularly advises, the most important way to prevent incidents is to ensure that all operators are suitably trained and monitored. But with challenges such as large-scale sites, busy traffic routes, multiple vehicle types and the pressure of deadlines, how can managers guarantee that best practice is followed every day?
Here are a few methods and tips for ensuring effective and consistent supervision during materials handling equipment (MHE) operations.
Walk the shop floor
Managers must have in-depth knowledge of best practice and what to look for when supervising operations. Not only should they be able to recognise any dangerous behaviour but they must also be proactive in challenging it and reinforcing basic training principles and the SSOW.
For example, overloading, speeding, pedestrians in unauthorised areas, not wearing seatbelts and unsafe dismounts are just a few examples of behaviours that need to be stopped and rectified.
Managers and supervisors must also keep an eye on who is operating MHE, like forklifts. Only employees who have been properly trained and authorised to use the equipment should do so. Managers must always ensure this is the case.
It is also a good idea to record bad practice using a standard document across the business, as this will help create consistent records of poor practice. These documents should be retained for an appropriate length of time so reviews can be carried out at appropriate intervals to identify trends or problems with poor practice. The documents will also help an employer to demonstrate (and retain proof) that checks on the safe (and unsafe) use of MHE have been carried out.
Keep an eye on key indicators
There are certain key indicators that those overseeing MHE operations can use to assess whether unsafe operations are taking place on site. Managers should look for tangible signs that best practice isn’t being followed, such as damage to trucks, racking, stock or fixtures and fittings, or missing pre-use inspection documentation for MHE.
Check the truck data
Fleet management software systems can be fitted to trucks to track data such as hours used, names of operators, speeds and sudden impacts. By analysing this data, managers can monitor patterns in operator activity and spot any anomalies that need to be addressed.
Have multiple eyes on operations
CCTV is helpful for checking operator compliance, but it must be reviewed regularly, not just when an accident or near miss occurs. The footage can provide insight into the general safety standards on site, as well as highlighting any complacency and corner-cutting going on, which can then be challenged.
Review training requirements
Regularly reviewing operator skills will allow managers to identify whether additional training is required. Refresher training is usually scheduled every three to five years but it could be required more frequently, for instance, if forklift operators have near misses, or there are changes to the equipment they use, their job responsibilities or the site layout.
Forklift awareness training courses – designed for people who work near and around lift trucks – and specialist courses for managers and supervisors, designed to give them a thorough understanding of how to ensure the safe operation and maintenance of forklifts, are now available and can be a useful way of teaching and reinforcing the MHE safety message to everyone at work.
What causes complacency?
Firstly, it’s important to define complacency, as it can sometimes be used as an all-encompassing term for explaining forklift accidents.
Complacency implies that a person (such as a forklift operator or someone who works alongside MHE), is over-confident in their abilities and lacks understanding of the consequences of bad practice.
On closer examination, complacency on forklift safety can be caused or influenced by a variety of factors. These include rushing, poor or inadequate perception of the risks, risk-fatigue over time (for example, failing to appreciate or disregarding the danger due to a long period without an incident, accident or near miss) and the repetition of tasks, such as operating a forklift for long periods or working near a forklift for long spells, which can cause people to begin to forget about risks and precautions.
Complacency can also potentially be influenced by an individual’s peers or the company’s safety culture – for example, if colleagues regularly take short-cuts around the safe use of MHE, or there is a culture of workers being allowed or even encouraged to take risks. As well as these possible factors, complacency may just be a natural consequence of human behaviour and how our brains work.
Our brains filter approximately two million bits of information per second. If we tried to process that level of information, we would be overwhelmed and ineffective. By nature, our brains have specific components designed to filter out information we deem unnecessary and focus instead on what we have decided is important. The brain therefore ignores stimuli that we deemed as repetitive and meaningless. It does this unconsciously and automatically.
For example, when we learn to drive, it is a new skill and we have to concentrate. Our brain is filtering information into our consciousness, and we are highly aware of the risks when driving. As we become more familiar with driving, we relax, and we don’t identify potential risks to the same extent. We are not as focused. Driving becomes second nature almost, and we allow ourselves to pay attention to other things, perhaps listening to or adjusting the radio, having conversations with passengers, or getting lost in thought. The brain is filtering out the risks as unnecessary information. Have they gone away? Of course not. Nor does it make someone a bad driver, it’s just how our brains work.
It’s the same with the workforce. The risks from forklifts and other MHE are always present, but those carrying out the tasks have simply become numb to the danger. It’s therefore the manager’s job to remind workers of the importance of always following safe practices when using or working near forklifts and MHE and to keep the entire workforce on the right track.
For more information see: mentortraining.co.uk
Stuart Taylor is Managing director at Mentor FLT Training
FEATURES
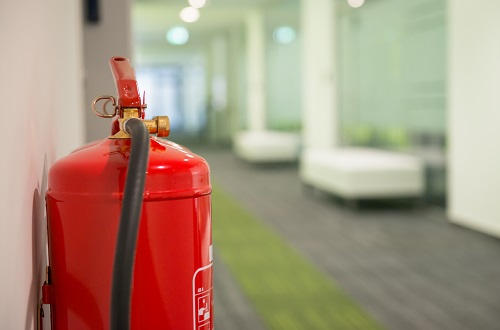
The C8 foam ban explained: what it means for you
By Laurie Pollard, Firechief® Global on 09 July 2025
From 4 July, the use of fire extinguishers and suppression systems containing the ‘forever chemical’ perfluorooctanoic acid (PFOA) will be prohibited, meaning duty holders need to move fast to ensure compliance with the law.
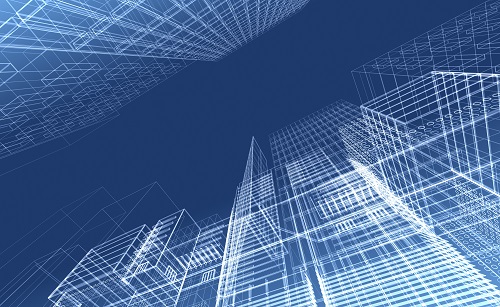
A year on – what have been the developments in competence management and the golden thread?
By Sofie Hooper, Association for Project Safety and Anthony Taylor, Resolve Risk Ltd on 03 July 2025
Last July the authors published an article in Safety Management where we looked at the expectations for those responsible for managing competence and those creating and managing the golden thread. In this edition we provide an update on both these key requirements of the Building Safety Act/Fire Safety Act’s ‘new regulatory regime’ including for higher-risk buildings (HRBs).
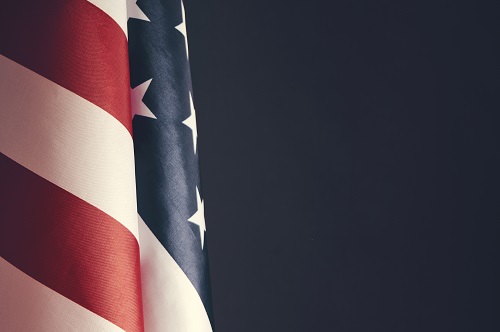
Stars, stripes and safety
By Belinda Liversedge on 07 July 2025
It seems like America today is rarely out of the news, particularly since President Trump won his second term. Our ‘special relationship’ with America has continued, with the country a strong pipeline for inspiration, products and trends.