Employers should be using new cost-effective technology and techniques to prevent workers suffering permanent and disabling hearing damage from exposure to loud noise at work.
Features
Noise exposure: time for a new approach
Unsustainable noise-induced hearing loss (NIHL) UK insurance claim payouts of more than £400million in 2014 alone illustrate just how ineffective current conventional noise risk reduction processes (dominated by personal protective equipment), have been to cut a health risk that is 100 per cent preventable. It’s long past time to make noise risk management effective by applying new techniques and technology.
The almost ubiquitous conventional approach to noise risk management has been to spend resources on repeated placebo noise assessments coupled with recommending personal hearing protection for workers.
Virtually no resources are spent on evaluating the effectiveness of the personal protective equipment (PPE) in practice. Photograph: shutterstock
Virtually no resources are spent on evaluating the effectiveness of the personal protective equipment (PPE) in practice (despite HSE research proving that hearing protection is not effective), or on modern, low cost (even self-financing) and highly effective noise control measures for plant and machinery.
However, there is an updated best practice approach that can reduce NIHL risk within almost any organisation by 75–90 per cent. In most cases, this can be achieved at negligible cost or even at a profit when compared with current expenditure.
The three key areas where the current process must be changed are as follows:
- Assessment: do not waste money on repeating placebo noise assessments that tell you what you already know – that you have a problem with noisy plant and machinery that pose a risk of damaging the hearing of workers. Spend the resources on noise risk reduction instead, particularly as – according to the HSE – most noise assessments are inadequate and not fit for purpose.
- PPE performance: there is the potential to double or treble real-world personal hearing protection performance by understanding the limitations and using the latest PPE technology. This involves ignoring the hearing protection equipment manufacturers’ assumed protection data for their PPE.
- Noise control: most organisations can reduce risk by 50–90 per cent at little or no cost (or even at a profit), by using online tools to source the best engineering noise control measures available anywhere.
Let’s explore those three key areas in a little more detail.
Risk assessments
Do not keep repeating noise risk assessments, just update them if there have been substantial changes to noise levels. HSE’s attitude is that you do not necessarily even need to measure noise levels, just start implementing noise exposure risk reduction measures. Risk assessments that do not include useful and practical information on noise control are inadequate by definition.
Do not keep repeating noise risk assessments, just update them if there have been substantial changes to noise levels.
Best practice is to carry out a noise control audit (NCA) instead of yet another risk assessment. An NCA is an engineering audit that generates a cost/benefit analysis of the noise control options for each item of noisy plant based on current best practice.
Anyone, whether they know much about noise or not, can make a basic evaluation of the likely control options using online information or by taking advantage of a free email analysis service. Under the Control of Noise at Work Regulations 2005, PPE (i.e. personal hearing protection) cannot be used for long-term risk management unless it can be proved that noise control is impractical.
This process will provide the information you need to budget and plan the most practical and cost-effective programme of action possible. It should also provide you with accurate plant noise levels.
Once you know the costs of noise control measures for plant and the estimated noise reductions they will provide, you can take into account both the risk reduction and cost savings from these measures – for example, less expenditure on PPE, audiometry and management resources, plus improved communication and productivity, etc – to determine the optimum course of action.
PPE performance
It has been known for decades that it is virtually impossible to guarantee adequate protection from hearing damage when using PPE where noise levels are much above 95dB(A) and it can even be difficult above 90dB(A).
HSE research – see bit.ly/3ijgIZa and bit.ly/38KQdIE – proving that hearing protection is not effective drives a coach and horses through any attempts by employers to defend a personal injury claim from a worker for hearing damage using the argument that they provided personal hearing protection to the affected individual.
Although the best way to guarantee the protection of exposed personnel is to reduce noise levels from plant, machinery and tools, there are simple ways to improve the real-world protection offered by the personal hearing protection equipment that is worn by workers. Therefore, when providing and using hearing protection, remember that:
- You must have a mechanism in place to evaluate the wear rate. The wear rate means that if – for example – a worker only wears their hearing PPE for half the time, the maximum attenuation (i.e. the reduction in noise exposure) they receive is 3dB (50 per cent), no matter the theoretical attenuation figure quoted by the PPE manufacturer. For a 75 per cent wear rate, the attenuation is 6dB. So, unless you know the wear rate, you have no idea of the protection that is being achieved in practice by the PPE. Therefore, logging wear rates provides a mechanism to evaluate changes in risk reduction performance over time. So, where appropriate, consider using the latest generation of ‘intelligent’ PPE that logs the wear rate and attenuation automatically. For a good example of this type of ‘intelligent’ hearing protection see: bit.ly/3ihTpi8
- You must train personnel in all aspects of the correct use of personal hearing protection, including its correct fitting. This is particularly important for ear plugs where the manufacturers’ assumed protection of 30dB can actually end up as low as 3dB in actual use if workers do not insert them correctly
- You must regularly audit the effectiveness of the hearing protection you provide to track and document its performance over time
- There is a prospect that new developments in field Otoacoustic Emission (OAE) audiometric testing will be able to provide feedback on any slight hearing loss in hearing protection users after just one year. Currently, conventional audiometry can only detect very large falls in hearing acuity that occur over a longer period. This longer time period is far too late to spot the signs of hearing damage as by then the damage has already been done. When this new technology becomes available, it should therefore provide a useful, low-cost tool to evaluate the effectiveness of a company’s hearing conservation programme.
Noise control
The general level of knowledge of noise assessors and non-specialist (or even specialist) engineers about modern best practice in controlling noise from plant and machinery is abysmal. Consequently – and much to the annoyance of HSE – practical and cost-effective noise control advice in noise assessors’ reports is conspicuous by its absence.
A little understood fact is that if you reduce noise by 3dB you have cut the risk of harmful noise exposure by 50 per cent. However, cut it by 7dB and the risk reduction is 80 per cent.
Consequently, if you can reduce noise from 98dB(A) down to 91dB(A), the risk to hearing has been cut by 80 per cent (even though you will still legally need to provide workers with personal hearing protection if noise is above 85dB(A)).
This also means that it becomes very much easier to guarantee adequate PPE performance, as the lower the noise level, the less attenuation is needed to protect the user adequately.
Most organisations can reduce NIHL by 50–90 per cent at little or no cost (or even at a profit) by applying the best engineering noise control measures available using the latest technology.
The question is: ‘How do you find the optimum noise control options?’ The answer is that there are comprehensive online databases of engineering noise control case studies that are freely accessible from anywhere by anyone. For example, see:
https://bit.ly/3nQUFtI
https://bit.ly/39zLk4t
https://bit.ly/2Lzdch2
https://bit.ly/2XWH61D
Safety professionals without engineering expertise who encounter noise problems or who have quotes for conventional high-cost noise control measures – such as noise-absorbing enclosures around machines – can search the four online databases above for better options.
Alternatively, they can take advantage of a free analysis service from INVC by emailing smartphone data (namely a short video clip and photos), acquired on-site for a cost/benefit analysis of the options based on the best of current technology. For more details on this, see: https://bit.ly/2LV7juo
While some noise control techniques require specialist engineering expertise and knowledge, many noise problems have simple solutions that can be found online and applied by any competent engineer. For example, see the Detailed solutions to the 10 most common industrial noise problems on INVC’s website at: https://bit.ly/38LxOvf
Updating best practice
Every year, a substantial number of employees suffer unnecessary hearing damage at work because the default risk management procedures currently used are not sufficiently effective. Based on results, they are obviously not best practice.
Three simple changes to the ‘standard’ approach can reduce NIHL risk by 75–90 per cent quickly and at negligible or no cost. In many cases, the revised procedures and techniques introduced to reduce risk are less costly than current expenditure.
The necessary changes involve:
- Eliminating much of the current costly (and ineffective) risk assessment and reporting process
- Learning how to evaluate the real-world attenuation from hearing protection and modifying hearing conservation programmes to increase performance
- Taking advantage of smartphones and other digital technology to gain free access to the latest low-cost engineering noise control techniques to reduce noise from plant and machines at source.
75–90 per cent reduced risk for less than the current expenditure on noise? Sounds like a plan…
Peter Wilson is Technical director at INVC
FEATURES
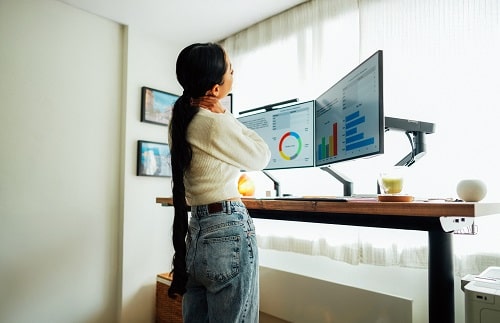
Adaptability, ergonomics and wellbeing: building blocks for the workplace in 2025
By Guy Osmond, Osmond Ergonomics and Alex Reffell, Osmond Inclusive Wellbeing Services on 04 February 2025
Employee expectations around the nature and organisation of office, home and hybrid working have changed significantly in recent years, making it more important than ever for employers to rethink and update their approaches to flexible working, ergonomics and workplace design, to better support employee wellbeing, motivation and job satisfaction.
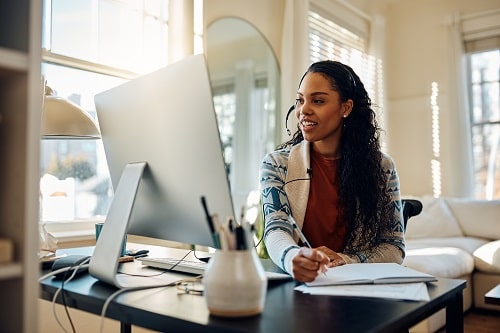
Supporting wellbeing across the flexible extended workplace: why we need a different approach
By Andy Lake, Flexibility.co.uk on 04 February 2025
Flexible working has been shown to offer numerous benefits, from improved employee wellbeing to greater productivity. But the rapidly changing nature of work in a digital age means employers need to take a strategic, joined-up approach when implementing flexible working practices, if they are to fully realise the benefits.
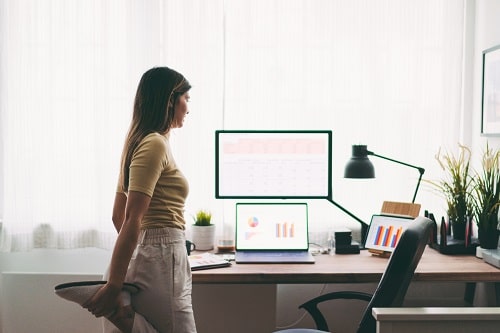
Supporting wellbeing when working from home: some key tips
By Nigel Oseland, Workplace Unlimited on 31 January 2025
Home and hybrid working are now firmly established as regular working patterns for significant numbers of people, so it’s a good time for employers to revisit their arrangements for supporting the wellbeing of home workers – from ensuring good ergonomic workstation set-ups to encouraging regular rest breaks.