Opinion
Common safety pitfalls in manufacturing – what can we learn from recent prosecutions?
Statistics from the Health and Safety Executive (HSE) show that the manufacturing sector directly employs approximately 2.5 million people and accounts for 16 per cent of reported injuries to employees in the UK. The diversity of the sector – both in the type and size of businesses it incorporates – gives rise to a number of different health and safety hazards that need to be appropriately managed to ensure the health and safety of workers.
This article looks at three common themes arising out of recent prosecutions of businesses in the manufacturing sector for breaches of UK health and safety legislation. It also considers what can be learnt from these examples to help improve health and safety in a manufacturing business.
Hannah Frost, Solicitor at Pinsent Masons LLP.
1. Inadequate guarding of machinery
A consistent consideration across most manufacturing businesses is a requirement to manage risks posed to their workers by machinery. So, looking at and reviewing two recent prosecutions by the HSE, what are the key safety takeaways from these cases?
Unsafe practices and failure to act on advice
In the first case, ADA Machining Service Ltd was fined £20,000 plus costs following a guilty plea to charges under section 2(1) of the Health and Safety at Work etc Act 1974 (HSWA). This section requires an employer to ensure the health and safety of their workers so far as reasonably practicable.
The charges followed an incident where a worker’s hand was severed while operating a 16-foot vertical boring machine. The worker had stepped onto the machine’s rotating table when it was in operation to check on the work. He slipped and fell and his hand was drawn into the in-running nip and was partially severed.
HSE’s investigation found that there was inadequate guarding to prevent access to dangerous parts of the machinery and the risk assessment in place to cover the operation of the vertical boring machine was considered to be inadequate.
In addition, the HSE discovered there was an established practice in the organisation whereby workers would walk on the rotating table while the boring machine was in operation. HSE had previously provided guidance to the company in relation to guarding boring machines following a similar incident 11 years earlier and identified that the company was aware of the risks posed by the boring machine but had failed to take appropriate remedial action to prevent another similar accident happening.
A culture of compliance is crucial for a business to meet its health and safety obligations. Unsafe practices must not be allowed to continue and employers must ensure that workers are left in no doubt that adherence to health and safety requirements is mandatory.
Risk assessments must be tailored to the particular business operations, regularly reviewed and updated when necessary. Any changes to a risk assessment and the control measures in place must be clearly communicated to workers who should be given suitable training about how to continue to work safely.
There can be no one-size-fits-all approach and the risk assessment itself must not simply be a tick box exercise. HSE guidance and warnings on how to protect the health and safety of workers must be carefully considered and relevant recommendations – either from HSE or the employer’s own risk assessment – must be implemented if enforcement action is to be avoided.
Young workers
In the second case, Amber Industries Limited was prosecuted following an incident where a 17-year-old apprentice was injured while working on an unguarded pillar drill while wearing gloves. The glove on his right hand became entangled in the drill bit and three of his fingers were severed.
In this case, the HSE investigation found the company had failed to provide suitable training to the apprentice, including clear instructions not to wear gloves. There were also no guards in place to prevent access to rotating parts of the drill. The company was fined £52,500 plus costs.
This case highlights the importance of not only guarding machinery appropriately but ensuring that workers are appropriately trained and supervised when operating it. Risk assessments, risk mitigations and training must also take account of the demographic of the particular workers involved. Young workers can be particularly vulnerable to injury or ill health as they are more likely to lack experience, maturity and may be less confident to raise concerns, so care must be taken to provide them with suitable training and supervision. To coincide with the recent National Apprentice Week in February 2023, the HSE also reminded employers to follow its guidance on ensuring the health and safety of young workers.
2. Workplace transport and forklift trucks
Our second theme relates to the risks arising from workplace transport.
Failure to properly control workplace transport risks
G-Tekt Europe Manufacturing Limited was fined £525,000 plus costs following a prosecution by HSE after one of its workers suffered a life-changing brain injury when they were struck by a forklift truck.
HSE’s investigation found that there was inadequate control of workplace transport risks at the company’s premises – including insufficient safety signage, a lack of separation between vehicles and pedestrians and a lack of safe pedestrian crossings.
Manufacturing environments can often be complex to manage from a health and safety perspective. In warehouses and factories in particular it is important that specific attention is paid to appropriately managing the workplace transport risks – including developing effective traffic management plans and implementing controls to ensure the separation of vehicles and pedestrians. Again, a culture of compliance – where employees at all levels see health and safety compliance as an important part of their role – is crucial too.
3. Risks posed by vibrating tools
Our third theme looks at two recent cases relating to the risk to workers using vibrating tools.
Importance of recognising the risk and acting upon it
Following a report from a concerned employee, HSE visited MTL Advanced Limited, a metal fabrication company, and found that (among other safety issues identified), there were systemic failings to recognise the risk of workers developing the health conditions collectively known as hand arm vibration syndrome (HAVS) or to take appropriate action to control exposure to vibration risks.
Following prosecution for the failings, the company pleaded guilty to breaching section 2(1) of the HSWA and was fined £90,000 plus costs.
As part of their investigation, HSE noted that despite reports from employees of pain and tingling in their fingers, hands and arms indicating exposure to harmful levels of hand arm vibration (HAV), the company did not implement reasonable control measures such as limits on use of tools such as angle grinders.
In a similar prosecution, Frontier Plastics Ltd was fined £246,000 plus costs after pleading guilty to similar charges. This time, two employees developed HAVS as a result of using vibrating tools, such as strimmers, drills and hedge cutters, without suitable controls in place to manage the HAV risks.
HSE’s investigation identified that Frontier had failed to adequately assess the risks of using vibrating tools, put in place measures to control the risk, provide suitable training on the risks to employees or conduct suitable health surveillance to spot the early signs of vibration-related disease among the workers at risk.
Again, these cases highlight the importance of identifying and appropriately mitigating the risks posed by the use of vibrating tools in the workplace, conducting appropriate health surveillance and acting upon employees’ concerns over vibration exposure.
What can we learn?
While the health and safety risks associated with the manufacturing sector can be diverse and complex, the message is clear; as with all businesses, the risks must be appropriately assessed and mitigations put in place. The mitigation measures must be tailored to the business and workers involved, employees must be given adequate training on how to correctly follow them, and the risks and the mitigation measures must be regularly monitored and updated when and if necessary. The consequences of failure can be severe, not just in terms of the human cost, but also the financial and reputational cost for the business.
The tone from the top is crucial too and every business should have a culture of compliance that is viewed as mandatory by everyone across the organisation. This is particularly relevant in the current economic climate when businesses may be struggling to keep afloat. There can be no compromise on safety and health.
Contact Hannah Frost at Pinsent Masons law firm:
www.pinsentmasons.com
OPINION
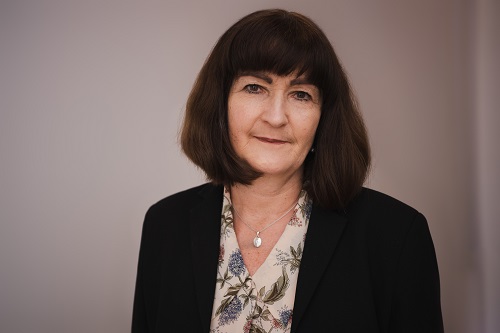
Battery Breakdown e-bike fire safety campaign: where are we two years on?
By Lesley Rudd, Electrical Safety First on 03 July 2025
The Product Regulation and Metrology Bill currently before Parliament offers the opportunity to reduce the fire risks posed by sub-standard e-bikes, e-scooters and their lithium-ion batteries, but the Government needs to go further and faster to protect public safety.
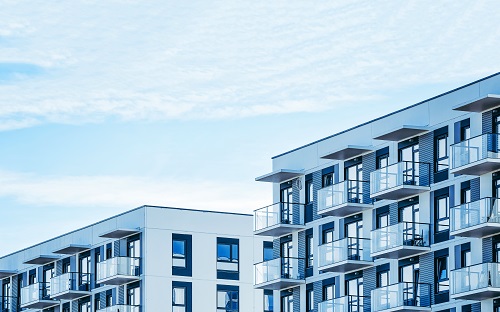
The building safety crisis: a year of Labour in power, still no end in sight for leaseholders
By Campaign team, End Our Cladding Scandal on 01 July 2025
It’s a year since Labour came to power with manifesto commitments to fix the failed approach to the cladding and building safety scandal and deliver meaningful change.
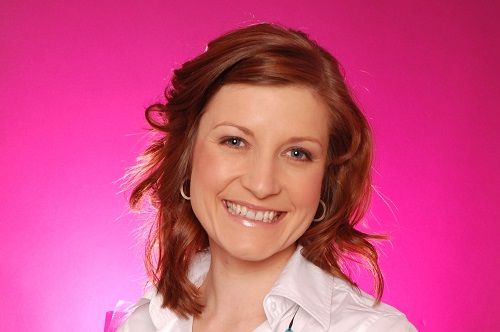
Rethinking workplace wellbeing for a new era
By Kate Field, BSI on 16 June 2025
Today’s workers increasingly value the flexibility to pick the most suitable working model for their needs – whether this be hybrid, fully remote or site-based. However, new BSI research shows a more important consideration is working for an organisation that genuinely prioritises employee wellbeing, offers development opportunities and encourages staff autonomy.