A Low Emission Zone for non-road mobile construction machinery in London is helping to reduce the plant’s contribution to the city’s air pollution – and in May 2023, the project was judged Innovator of the Year at the Fleet Vision International Awards.
Features
Construction machinery in London: cutting its contribution to air pollution
The health impacts arising from poor air quality are now very widely known. No longer considered issues confined only to respiratory function, there are now clear causal links made to cardiovascular disease, reproductive health and dementia, and the list is growing.
In fact, since the smallest of particles, those graded at PM2.5 and below, are able to cross into the bloodstream intact, they may circulate through every tissue and organ. Such particles are then able to cross cell membranes and become retained within cells.
Photograph: Cleaner Construction for London
Diesel compression chambers are excellent manufactories of PM2.5 pollutants, as well as the nitrogen Oxides (NOx). These further compound health impacts.
The UK can count 36,000 deaths annually where poor air quality has paid a part. Of these, London has a share of 4,000. Since we are all breathing polluted air, it follows that all of us shall have our health adversely affected. According to the World Health Organization (WHO), air pollution is the single greatest environmental risk to health.
The harm caused by diesel fumes isn’t a new understanding, the hazards have been known for many years. The International Agency for Research on Cancer (part of WHO), stated that: “The scientific evidence was compelling, and the Working Group’s conclusion was unanimous: diesel engine exhaust causes lung cancer in humans. Given the additional health impacts from diesel particulates, exposure to this mixture of chemicals should be reduced worldwide.”
That was released back in 2012. There’s additional bad news. The more that gets discovered about diesel pollutants, the more alarming the picture becomes.
There’s some good news too. Over the past 11 years, the diesel engines coming off production lines have got very much cleaner, but of course the operational fleet on the ground lags behind these standards, often by decades.
There are a number of things that can be done to mitigate a construction worker’s exposure to engine emissions. Some are through the usual source/path/receiver approaches, such as retrofitting exhaust after-treatment, providing operator training on idling, or even just proper consideration of the location of generators, crushers and similar machines.
Andrew Gordon is project manager on the Pan-London Non-Road Mobile Machinery Project at Cleaner Construction for London. Photograph: Cleaner Construction for London
In London, however, something additional has been going on. A great deal has been achieved through policy measures set out in 2014 by the Greater London Authority (GLA). Once implementation of this policy became city-wide in 2019, London became the only metropolitan area in the UK to have a fully operational Construction Low Emission Zone (CLEZ).
The well-known road-based LEZ, and now the ULEZ (Ultra Low Emission Zone), offer significant air quality benefits, but the non-road engines need to be properly factored in too. Although air quality and public health professionals seem enthusiastic about the road LEZ and ULEZ, these measures are not without detractors, and they are politically active issues. Where the construction sector is required to take similar action on emissions, something is done to ‘sweeten the pill’ of the road-based initiatives for the commercial and residential end-users.
The GLA policy was published within a Supplementary Planning Guidance, designed to control the dust and emissions arising from construction. This set out a zones-based scheme, and a set of escalating requirements for the improvement of the construction fleet. In turn, the 33 local authorities referenced this document in their planning conditions, requiring that only the cleaner engines got deployed. What Cleaner Construction for London (CCfL) did, was to visit the active sites and ensure what was set out in policy was being reflected in the real world. It’s an ongoing piece of work of course, as incremental measures are taken to actualise the zero-emissions commitments of 2040.
Over the past seven years, the construction industry in London has done some truly exemplary work in mitigating its emissions, something that really should be recognised more widely. This work has been undertaken mostly within an environmental compliance and neighbourhood air perspective, but the huge co-benefit has been that of the health implication for workers, in addition to that of the local residents. It took the creation and enforcement of the construction LEZ to actualise a lot of the environmental objectives that would have otherwise likely just languished in the organisational strategy documentation of developers.
The London Atmospheric Emissions Inventory (2019) apportions to construction activity in London, 30 per cent of total PM10, eight per cent of PM2.5 and four per cent of total NOx. However, these values are for ambient levels, and not for hyperlocal levels. We know from the studies of road-based emissions, that ‘canyoning’ effects between tall buildings can create micro-environments within which pollutants may concentrate greatly. In neighbourhoods of regeneration, where construction sites are often operating alongside each other on all sides, very much higher apportionments of pollutants are found to be arising from this sector.
What area could in fact be more hyperlocal, than the construction site itself? Which receptor is more exposed, than the very operator of that dumper, excavator, or perhaps the SHEQ manager sitting in a generator-powered cabin 10 hours a day?
How does a Construction Low Emission Zone operate?
Although things can get technical quite quickly, simply put, engine emissions are set out in Emission Limit Values, which assign per kW of power produced, given amounts of NOx and PM. Tested engines are type-approved with a more simplified ‘Stage’ coding running from: I, II, IIIA, IIIB, IV and V, getting cleaner as we go. It’s not unlike the Euro 1–6 system for road-going vehicles. See the table below.
Source: Non-Road Mobile Machinery (NRMM)
Practical Guide v.5, Cleaner Construction for London, london.gov.uk/media/47992/download
Of course, as the engine ages, we can expect that performance for emissions reduction falls off to an extent, but the coding system remains a useful indicator.
On the engine casing of a certified engine (all lawful engines should be certified) there shall be an emissions plate. This holds a Type Approval Number from which the Emissions Stage can be inferred.
The London zones system currently creates requirements for engines to be at IIIB, IV and V, according to location. This means that the dirtier engines at I, II, and IIIA should not be deployed on construction sites if they are >37kW. Very small dumpers and excavators are currently ‘off-scope’ but most of the kit you’d see on a typical site, including most generators, comes under the scheme.
If the machines encountered during site inspections are not to standard, they must be removed if NRMM planning conditions are to be successfully discharged. Of course, such machinery shouldn’t be there in the first place, but the inspection process is forward-looking and seeks to create good environmental governance where it has been found to be wanting. The scheme has always worked cooperatively with industry. For some of the smaller contractors, it actually provides a valued service, and is far from just being perceived as a regulatory function.
The London Construction Low Emission Zones. All of the London boroughs are included, with additionally enhanced requirements for those zones shaded orange. From 2025, all of London shall have the same requirement, of Stages IV and V. Map courtesy of: nrmm.london
So, what can be done for construction workers outside London?
A contractor outside London, seeking to best protect their staff and local residents, can simply specify that their fleet, either in-house or from suppliers, is to that same set of standards.
Everything is set out on the GLA website, where there’s a download of the Practical Guide which is a succinct booklet containing everything you need to know.
Keeping an auditable record of the emissions stage of your NRMM fleet is a good way to demonstrate that you’ve taken reasonable steps to mitigate needless worker exposure to airborne pollutants, and are also on the journey towards zero emissions.
What does this actually mean for the health of workers and residents?
Because CCfL seek to visit all sites in London, and record details from the engines and machines themselves, the dataset collected is certainly the most accurate representation of the construction fleet of any city, very likely worldwide. We can see the favourable trends over different machine types over the months and years.
We’re just about to re-run our emissions model incorporating the 2022/23 data. It’s been a busy year and we completed 1,755 audits. Last April we modelled some really encouraging savings derived through the zone implementation. Of particulate matter, of which most shall be PM2.5 and sub-PM2.5, savings were in the region of 71 tonnes. For nitrogen oxides, 1,600 tonnes of pollutant were prevented from being needlessly discharged into neighbourhoods.
How are such huge savings possible? The Emissions Stages shown in the table on the previous page, really count for a lot once operational hours and kilowatts are factored.
When a machine is either swapped-out, or better still specified to the London standard at the outset, when we compare annual emissions against the previous non-compliant stage, the savings are huge. See the table below.
An elevated specification from IIIB to IV, as occurs in the enhanced zones, delivers a massive annual NOx saving. Not to mention the IIIAs, IIs, Is, as well as the uncertified engines that are still encountered on a routine basis.
In Greater London more widely, the default specification to a compliant IIIB from a non-compliant IIIA, delivers another order of magnitude decrease in annual PMs. This has very significant health implications.
Going forward to 2040 and to zero emissions
Just as Rudolf Diesel chose to use plant-based fuelling for his revolutionary engine at the turn of the 20th Century, it’s a rather similar story for the internal combustion engine. At the beginning of the 19th Century, Isaac de Rivas is credited with the invention of the first vehicle propelled by an internal combustion engine. The fuel that was used? You guessed it: hydrogen. It’s quite a recurring theme in low emissions technology, with milk-floats, trams, cargo-bikes and more, all appearing in the historical picture. Once fossil reserves of power were tapped, nothing else could compete. Now that these are no longer a viable resource, options that have remained in the wings for a while, return to the stage.
Hydrotreated vegetable oil for fuelling the current fossil fleet can only be considered a stepping-stone toward a more radical fleet upgrade. Because fossil fuelling has been so cheap for so long, we now really need to think more about deriving and specifying proper power-levels for given tasks, and the efficiency of the machines delivering these tasks.
Electrification of fleet is certainly the way some road-based transit is going, and this shall be the direction for a lot of the construction machinery. Fuel cells too, operating the HGVs running up and down the country, some with battery hybrid set-ups, shall likely find their way into similar application profiles in construction in the near future. The combustion of hydrogen in compression engines, is already a practical reality for excavators of typical size for major developments.
For hydrogen, it’s infrastructure that’s the key challenge, alongside of course, cost against the competitive options. For electrification, infrastructure again, where the grid is not yet able to carry the additional demand required. It may well be that policy measures set the future tipping point, whereby zero emission options become the default choice, rather than the selection only of exemplary organisations.
As things stand, the only driving forces working to accelerate in practical fashion, progress towards a cleaner and zero-emission construction fleet, are the site inspections in London, and the H&S and Environmental aspirations of the developers.
Summary
- Consider non-diesel options, including battery packs, temporary building supply, including battery-augmented TBS, hybrid options, electrified plant and hydrogen.
- Where diesel-engined plant is the only option, specify from suppliers or sub-contractors, the best Emission Stage models available, currently Stage V for most applications.
- Where upgrade of in-house fleet is unfeasible, retro-fitted exhaust after-treatment options exist.
- In London, register your sites and compliant plant with GLA online. (CCfL shall arrange an appointment and certificate your good work for free!)
- Outside London, just apply the same compliance criteria, but keep your NRMM records internally, rather than using the online register.
- Develop your environmental portfolio pro-actively, in anticipation of additional metropolitan zones arising in future.
- Grow your portfolio for tendering.
Andrew Gordon is project manager on the Pan-London Non-Road Mobile Machinery Project at Cleaner Construction for London.
For more information see:
FEATURES
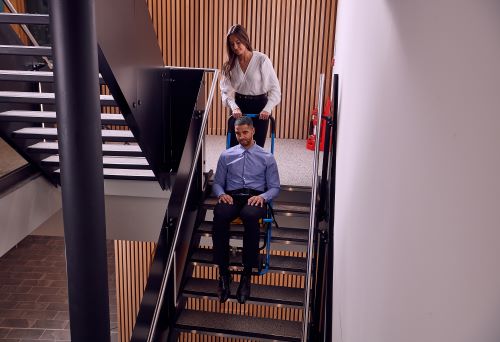
Emergency evacuation for people with mobility issues: why we must do better
By Gerard Wallace, Evac+Chair International on 01 August 2023
With research revealing poor understanding among many businesses of their duty to have arrangements in place to safely evacuate mobility-impaired people, it’s time for the government to educate building owners about their obligations and mandate the provision of evacuation equipment, to ensure a safe evacuation for everyone.
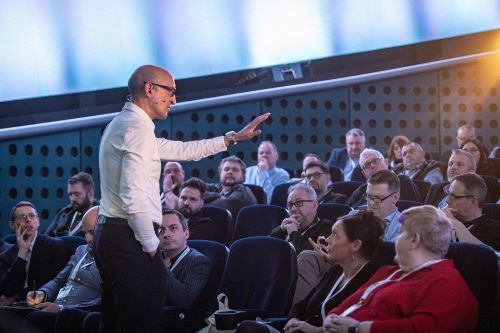
Establishing a company culture of safety
By Driving for Better Business on 01 November 2024
Collision prevention takes growth mindsets, psychological safety and a ‘just’ culture, delegates at the recent National Highways ‘Driving Change’ conference heard.
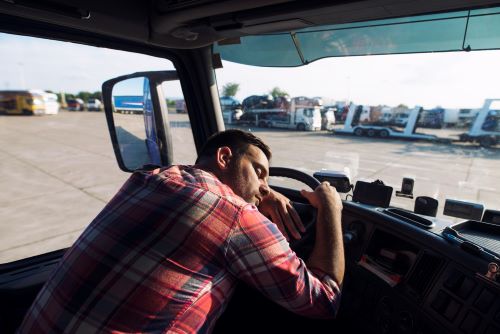
Driver fatigue: always minimise the risk
By Driving for Better Business on 01 November 2024
Research shows that driver fatigue may be a contributory factor in up to 20 per cent of road incidents, and up to one-quarter of fatal and serious incidents.