Whether it be managers knowing how to spot bad practice or co-workers understanding how to stay out of the danger zone, it’s clear that forklift training needs to cover more than just the operators themselves.
Features
Lift truck training: don’t forget co-workers
As we see all too often in industry news reports, materials handling operations can be extremely dangerous if proper safety measures are not taken. Indeed, it’s telling that the transportation and storage sector, for instance, which is heavily reliant on materials handling equipment (MHE) use, has significantly higher injury and fatality rates than the UK average.
As the ones in the driving seat day-in, day-out, forklift operators themselves are typically the main focus when it comes to reducing risk. They certainly have a vital role to play in site safety and, thankfully, the majority of today’s employers acknowledge the importance of basic operator training for the good of their people and their business. The work to be done in this area now seems to be around ensuring the standard and sufficiency of their training, via accreditation and the following of ACOP guidance.
As the ones in the driving seat day-in, day-out, forklift operators themselves are typically the main focus when it comes to reducing risk. Photograph: Mentor FLT Training
But targeting operators alone will only get you so far. Other areas for improvement have been identified by the industry and incorporated into a more holistic approach to training. By broadening the reach in terms of who we train and how we do so, we’re able to reduce risk further, across the entire workforce.
Widening the reach
In recent years, more attention has been given to those who oversee operations. Even well-trained operators can make mistakes or become complacent over time, so supervision and monitoring is key to maintaining a safe working environment.
However, to be effective, managers and supervisors must be able to spot and correct bad practice. With no requirement for those in a management role to come from an operating background, more and more employers are recognising the fact that specialist training is essential for those managing forklift operations, to ensure safety and compliance is upheld.
A watershed moment for the industry was the addition of specific references to this as a requirement in the HSE’s definitive forklift safety document Approved Code of Practice for Rider Operated Lift Trucks (L117), when it was re-released in 2013. Though already best practice, its specific inclusion in the ACOP cemented it as a firm requirement for businesses with MHE.
Despite the progress, there remains much room for improvement, as many still don’t understand that ensuring these skills is a necessity, with 50 per cent of businesses we recently surveyed reporting that their managers had received no formal training in managing forklift operations.
What’s more, because our sector is always looking to reduce risk further, the training landscape continues to widen and employers are being urged to consider others who work alongside MHE, including colleagues on foot, visitors, delivery drivers and more. With no protective cab and often little to no specific training, they make up the most vulnerable group in this environment so it’s vital that they are made aware of the risks they face while working alongside these powerful trucks day-to-day.
Unlike basic operator training, forklift awareness courses can provide a concise, impactful look at key safety messages surrounding forklift use, enabling everyone to understand how to keep themselves and others safe around MHE. This makes them suitable for pedestrians as well as experienced operators at risk of complacency, emphasising to all parties the need to stay alert and maintain safe distances. After all, it’s important that everyone working with forklifts in any capacity understands the importance of following safety measures, and the potential consequences if they don’t.
Stuart Taylor: "What we know for sure is that there is certainly an ever-growing appetite for flexible ways of learning, and forklift training will undoubtedly keep evolving." Photograph: Mentor FLT Training
Improving access to vital training
As the audience has evolved, so too have the learning patterns and formats of training on offer.
Change is inevitable, and it’s important that MHE training providers evolve their courses to ensure vital training can be accessed by those who need it. Even prior to the pandemic and the world’s reliance on online platforms, our sector was busy developing e-learning courses that could bring information to more audiences.
Due to their very nature, operator courses will always need to contain practical, hands-on training. But there are opportunities to utilise flexible e-learning options within our industry, as traditional, classroom-based courses can present challenges for some employers, particularly with regards to organising training for managers.
E-learning options have therefore been developed as a direct response, to offer a flexible alternative and overcome barriers such as:
- Staff availability: any companies struggle to free up individuals for training as it can impact operations and productivity. But with learners able to complete training at a time and place that suits them, businesses don’t need to worry about losing staff en masse or at key times. This is especially valuable for managers, as significantly limiting management presence across multiple sites for a sustained period is not viable in many cases.
- Location: Because training is done online, there is no need to send learners off site. They simply need access to a device and internet access, whether this is at work or at home.
- Time: E-learning courses can generally be completed in fewer total hours as they are completed at the individual’s own pace. It also allows them to dip in and out of modules around their other commitments and engage with training when it suits them.
- Cost: The cost of sending learners on training courses can be considerable, especially when you factor in expenses for food, travel and maybe even hotels. But with e-learning you save on all these costs, and the associated administration time.
- Engagement: Theoretical training content lends itself well to videos and quizzes that can easily be delivered over e-learning platforms. Courses can be broken down into modules, and offer effective, interactive elements that actively engage delegates, assess knowledge, and track training progress.
- Integration: E-learning courses can often be obtained as licenced versions, which can be added to a business’ existing Learner Management System. This means all training and associated records can be accessed from a single location, enabling consistent training records and efficient reporting.
We have already seen businesses of all types and sizes across a wide range of industries adopt e-learning courses to date, with some making management courses a mandatory requirement, and others rolling out the course as part of a worldwide forklift safety programme.
The future
When it comes to training, broadening the reach to enable wider understanding amongst all those at risk continues to help businesses stay safe, compliant and productive, and this is evidenced by the exponential uptake of e-learning across the industry to date.
What we know for sure is that there is certainly an ever-growing appetite for flexible ways of learning, and forklift training will undoubtedly keep evolving, removing the obstacles and opening up access to essential skills (and safer workplaces) even further, in the future.
For more information see: mentortraining.co.uk
Stuart Taylor is Managing Director at Mentor FLT Training
FEATURES
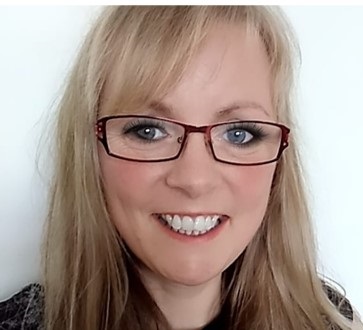
From crisis to prevention: the urgent role of employers in upstreaming health
By Dr Julie Riggs, British Safety Council on 16 June 2025
Poor public health and long-term sickness absence are placing extreme financial pressure on the UK’s health and social care system and the overall economy. However, by investing in workplace health prevention programmes and education initiatives, employers can help reduce the scale of ill health among the population and minimise the associated costs for society and business alike.
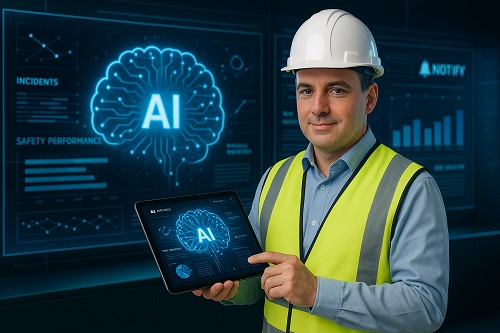
The AI safety revolution: augmentation, not elimination
By Alex Nichol, Notify Technology on 16 June 2025
Artificial Intelligence looks set to vastly reduce the amount of time and effort required to record, create and analyse occupational safety and ESG data, procedures and performance, while automatically providing insight into areas for improvement and areas of excellence.
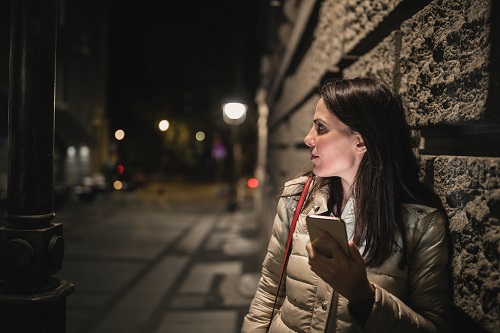
Protecting lone workers: a structured approach is critical
By Naz Dossa, Peoplesafe on 06 June 2025
Whether dealing with the public in their homes or working in remote locations, lone workers face a variety of risks to their health, safety and wellbeing. It’s therefore vital that employers systematically identify and assess the specific hazards lone workers face and then implement suitable measures to mitigate them.