Getting the PPE selection process right leads to better wearer protection, cost savings and environmental benefits – but it’s essential to use a specialist provider with the expertise to guide you.
Features
Selecting PPE: suitability and sustainability are key
The pandemic-induced mass demand for personal protective equipment (PPE) led to a worldwide scramble for sought-after global stocks, where control over spend was de-prioritised. In the aftermath of this, the focus seems to be firmly back on allocation – spend and control, with cost saving initiatives coming back to the fore. Along with this is a prioritisation of quality, sustainable and fit-for-purpose options, and specialist services and solutions like site surveys to properly assess requirements.
Photograph: iStock/maselkoo99
Organisations are keen to make the right product choices for their needs, minimise their carbon footprint and ensure the safety, wellbeing and comfort of their employees. The latest innovations, technologies and solutions emerging, as product innovation gets back on track following a lull, are helping them achieve this. And, contrary to common perception, choosing better quality or more sustainable options can actually create cost efficiencies rather than added cost.
Negating a one-size-fits-all approach... once and for all
It was perhaps difficult to be choosy in a scenario of low global PPE stocks, with a ‘take what you can get your hands on’ approach. But, even prior to the pandemic, many organisations would have been in the habit of buying high volumes of single-use products like gloves and masks in one, or limited, sizes. It may not seem too big an issue, but poorly fitting PPE can inadvertently cause the wearer to manually adjust the product for comfort. This is a natural human reaction, and one that can often happen without the wearer realising. In some cases, this could render the PPE ineffective.
Workwear that is ill-fitting will be too tempting to leave unzipped, rolled up or secured using products not included or approved with the specification, potentially exposing skin and/or causing excess material to become a trip or snag hazard. A mask that has not been correctly face-fit tested can cause leaks, and result in the wearer breathing in the very hazard that the mask was designed to protect them from.
Loose gloves can end up getting caught in machinery, or prevent the wearer from being able to hold their equipment safely, causing grip issues and increasing the risk of hand injury. Gloves that are too tight can affect dexterity, comfort and safety. These examples constitute just some of the many possible scenarios, and present issues to organisations including the safety and wellbeing of employees, contamination risk to production applications, compliance breaches and reduced work output, to name a few.
Ryan Plummer is senior director at RS Safety Solutions.
The emerging solutions and technologies to remedy this are now plentiful, and thanks to greater awareness, more accessible and more easily adopted. Better quality single-use gloves, some of which are manufactured or packaged in a more low-carbon way, present a more sustainable option for this consumable. A higher quality glove may present an initial higher cost, but when taking into consideration the fact it should last longer it can become cost comparable or even more cost efficient. Lower quality gloves may tear more easily and require more changes so ultimately prove more costly overall.
A growing focus on sustainability
There’s no doubt sustainability is becoming a huge consideration and priority as organisations focus on controlling spend and making the right PPE purchasing decisions. And rightly so, as single-use PPE has a significant impact on the environment. The issue is being tackled through the development of lower carbon manufacturing, packaging and transportation processes, use of innovative materials that are recycled or recyclable, and biodegradable options. Therefore, there’s no reason why sustainability can’t be a significant part of any PPE purchasing decision.
Taking gloves as a prime example of a single-use product that is a major landfill contributor, switching to a higher quality product to minimise wastage as a result of the product failing is a great start. But with options that can biodegrade by 90 per cent in 490 days, compared with a traditional nitrile glove which can be in the decomposition process for more than 100 years, organisations can go the extra mile to reduce their environmental impact.
Where processing environments call for strict hygiene standards, like food production, opting for alternatives to single-use aprons can make a real difference. Durable, reusable and washable options that still comply with food safety regulations, can help firms meet environmental goals and save money in the long run. Many of the available options can individually equal a saving of more than 200 disposable garments going into landfill. When used across a workforce, the savings in both money and waste are remarkable.
Specialist advice and services are real requirements
While organisations using PPE are focusing on spend and sustainability goals, knowing where to start and navigating what can be a minefield of products and information is a daunting task. Rather than buying from generic sources, there has been a notable requirement for specialist providers. PPE buyers aren’t just looking for a provider that can offer a wide variety of products for a range of sector needs, but also knowledge and expertise in the best products for the application, a strong understanding of regulations and compliance requirements and site survey services to help them understand their true needs.
Following a period of uncertainty around stock sourcing, firms are also increasingly looking for strong and reliable supply chains, as well as assurance that it is ethical (and verifiable) and they are not at risk of receiving fake, sub-standard or non-compliant goods. PPE isn’t simply a commodity which should be procured in bulk with price being an overriding factor, and thankfully, this is a much more widely recognised realisation.
As industry innovation has been kick-started and new products begin to flood the market, organisations with a PPE requirement should embrace the options available and commit to proper assessment of requirements and the close catering of them, for the good of employees, budget and planet.
Ryan Plummer is senior director at RS Safety Solutions. He has been involved in B2B distribution for more than 18 years, with experience of product and service solutions at the design, build and maintain phases of the asset lifecycle.
For more information on the PPE available from RS Safety Solutions see:
FEATURES
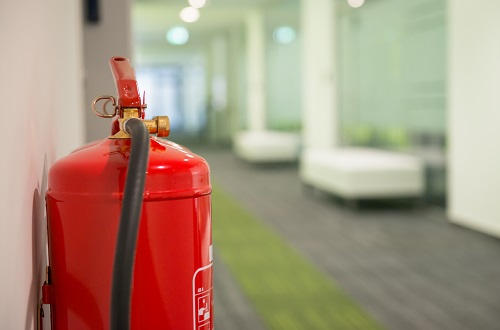
The C8 foam ban explained: what it means for you
By Laurie Pollard, Firechief® Global on 09 July 2025
From 4 July, the use of fire extinguishers and suppression systems containing the ‘forever chemical’ perfluorooctanoic acid (PFOA) will be prohibited, meaning duty holders need to move fast to ensure compliance with the law.
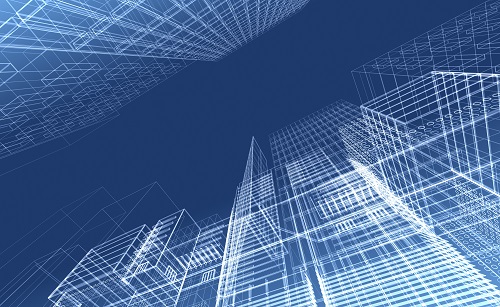
A year on – what have been the developments in competence management and the golden thread?
By Sofie Hooper, Association for Project Safety and Anthony Taylor, Resolve Risk Ltd on 03 July 2025
Last July the authors published an article in Safety Management where we looked at the expectations for those responsible for managing competence and those creating and managing the golden thread. In this edition we provide an update on both these key requirements of the Building Safety Act/Fire Safety Act’s ‘new regulatory regime’ including for higher-risk buildings (HRBs).
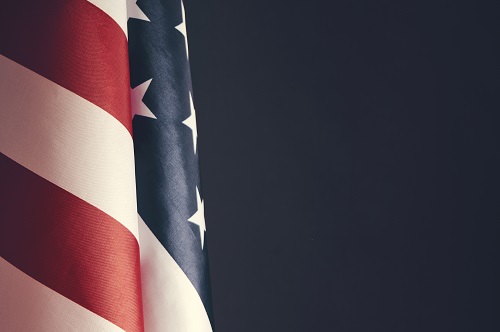
Stars, stripes and safety
By Belinda Liversedge on 07 July 2025
It seems like America today is rarely out of the news, particularly since President Trump won his second term. Our ‘special relationship’ with America has continued, with the country a strong pipeline for inspiration, products and trends.