Specifying fire doors that have undergone independent third-party certification provides reassurance the door will perform as stated in the event of a fire, when correctly installed and maintained, and ensures compliance with fire door regulations to protect lives and property.
Features
Championing fire door safety best practice
On a typical day, a fire door is no different to an average door – they’re often access routes into a room or building. In the event of a fire, however, the true ability of a fire door is revealed as it holds back the spread of smoke and fire to save lives.
Photograph: British Woodworking Federation
Since the Grenfell Tower tragedy, the introduction of new legislation holds those with responsibility for fire doors and other fire safety systems to higher levels of accountability. But what does this mean for the ‘responsible person’ and how can you demonstrate that passive fire protection measures, such as fire doors, will perform as designed in the event of a fire?
The life-saving role of fire doors
The majority of public, commercial and multiple occupancy buildings require fire doors to hold back the spread of fire and/or smoke to allow time for safe exit from the building and for fire services to enter to tackle the fire. Compartmentalising the building, and in turn controlling the passage of fire and/or smoke, these doors play a vital role in keeping escape routes clear.
The fire door classification – the period of time it can resist fire, or whether it can control the passage of smoke – is identified by testing to either the National System or European System.
Fire doors which have been assessed to BS 476: Part 22 for fire resistance can, for example, if tested, resist fire for a minimum of 30 minutes and can be classified as FD30. Additional successful testing to BS 476-31.1 for smoke control enables them to be classified as FD30S.
For classification under the European System, fire doors are assessed to BS EN 1634-1 and those that resist fire, when tested, for a minimum of 30 minutes can be classified as E30. Successfully passing the smoke control test – BS EN 1634-3 – enables them to be classified as E30Sa.
The benefits of third-party certification
The ability of fire doors to perform as needed in the event of a fire can mean the difference between life and death. This is why at the BWF Fire Door Alliance, we believe that only through third-party certification can you be confident that a fire door will perform as stated.
Third-party certification provides crucial evidence of performance and, importantly, supports traceability throughout the supply chain. This sees each certified fire door given a unique identification number so that all key information including manufacturer details, test reports and compatible component parts can be accessed for ongoing maintenance and awareness purposes.
A robust process, fire door third-party certification involves three steps:
- Fire testing – At least one full-sized fire door assembly is tested in accordance with BS 476: Part 22 or BS EN 1634-1 at a UKAS accredited test facility. This provides proof of performance and contributes to the scope of certification.
- Manufacturing process audit – The fire door manufacturer or licensed processor is audited by a UKAS accredited certification organisation ensuring that manufacturing and management processes are in place to deliver consistency.
- Regular audits – The fire door type, and its production, are subject to regular scrutiny through ongoing testing and auditing of the manufacturing and quality management systems to demonstrate repeatable test results and performance.
Positively, the BWF Fire Door Alliance Be Certain, Be Certified campaign found an increased understanding of the benefits of third-party certification in 2023. This is a welcome sign of the industry’s drive for best practice surrounding fire safety, and is particularly important in light of the Building Safety Act and Fire Safety Act.
The ‘golden thread’
The introduction of the Building Safety Act 2022 and Fire Safety Act 2021 has set out new requirements to place greater accountability on the persons responsible for fire safety and traceability throughout the construction supply chain. This means a ‘golden thread’ of information is required to demonstrate compliance with building regulations and provide evidence of performance.
Kevin Underwood is technical director at British Woodworking Federation (BWF). Photograph: BWF
While third-party certification of fire doors is not mandated, it does provide robust proof of performance and traceability – two of the key elements required by the recent legislation. This view has been supported by BWF Fire Door Alliance research, with two thirds (66 per cent) of those responsible for fire door specification, installation and maintenance across the UK stating they’re more likely to seek certification as a consequence of the Building Safety Act.
Fire door inspection
The performance and testing of a fire door are crucial to its specification and ensuring compliance. However, once installed only through regular inspections and prompt maintenance can this be upheld.
Under article 17 of the Regulatory Reform (Fire Safety) Order 2005 (FSO), it is a legal requirement to ensure that fire resisting doors and escape doors are “maintained in an efficient state, in efficient working order and in good repair”.
Expanding on this, the Fire Safety (England) Regulations 2022 set out the inspection regime for fire doors in multi-occupancy residential buildings in England above 11 metres in height. The legislation requires quarterly checks of all fire doors including self-closing devices in common building areas and yearly checks of flat entrance doors including self-closing devices.
However, at the BWF we believe that the frequency of use should also be considered when developing fire door inspection programmes. For example, a fire door that is installed in a communal space, where it may be more at risk of damage and subject to a high volume of traffic, should be inspected more frequently than others. This could mean scheduling inspections once per week, or month, depending on its usage.
When inspecting a fire door, there are five simple steps to quickly identify any issues:
- Certification – is there a label or plug on the top or side of the door leaf to evidence it’s a third-party certified fire door? Or does the doorset have a conformity marking label applied? If not, report it to whoever is in charge of your building. All ironmongery such as locks, latches, controlled door closers and hinges must be conformity marked, when required, and compatible with the door leaf’s certification.
- Apertures – check the door for alterations for glazing apertures or air transfer grilles as this will make certification void.
- Gaps and seals – check the gap around the door frame is consistent – this is often between 2mm and 4mm, while the gap under the door can be up to 8mm. If the gaps are larger or you can see light under the door, report it. Look for signs of damage to the intumescent seals around the door or frame. If there’s an issue, report it as the seals are vital to stopping fire and/or smoke moving through the cracks.
- Closers – confirm the closer shuts the door onto the latch from any position.
- Operation – ensure the door closes around all parts of the frame without sticking on the floor or frame.
For fire doors that are third-party certified, they should be inspected against the original specification and any maintenance must be carried out in line with the original certificate. This helps ensure that the certification isn’t invalidated.
Driving best practice and awareness of fire door safety
A correctly installed and maintained third-party certified fire door can mean the difference between life and death in the event of a fire. This is why at the BWF, we continually raise awareness of their crucial role through our ‘Be Certain, Be Certified’ and Fire Door Safety Week campaigns. As we prepare for this year’s annual Fire Door Safety Week campaign in September, it’s clear that ongoing education and awareness is vital to help drive industry best practice and public engagement with fire door safety.
Everyone can play a role in ensuring that a fire door performs as it should in the event of a fire. From fire safety professionals, who specify and install fire doors, to building owners and managers, who maintain them, to the people using them every day – with the right information everyone can help spot and report issues which might save a life.
Kevin Underwood is technical director at British Woodworking Federation (BWF).
For more information visit:
FEATURES
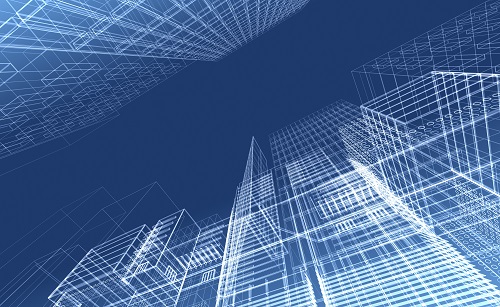
A year on – what have been the developments in competence management and the golden thread?
By Sofie Hooper, Association for Project Safety and Anthony Taylor, Resolve Risk Ltd on 03 July 2025
Last July the authors published an article in Safety Management where we looked at the expectations for those responsible for managing competence and those creating and managing the golden thread. In this edition we provide an update on both these key requirements of the Building Safety Act/Fire Safety Act’s ‘new regulatory regime’ including for higher-risk buildings (HRBs).
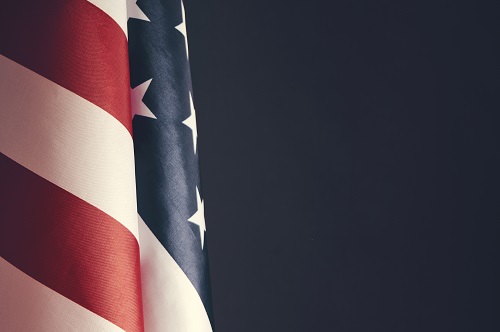
Stars, stripes and safety
By Belinda Liversedge on 02 July 2025
It seems like America today is rarely out of the news, particularly since President Trump won his second term. Our ‘special relationship’ with America has continued, with the country a strong pipeline for inspiration, products and trends.
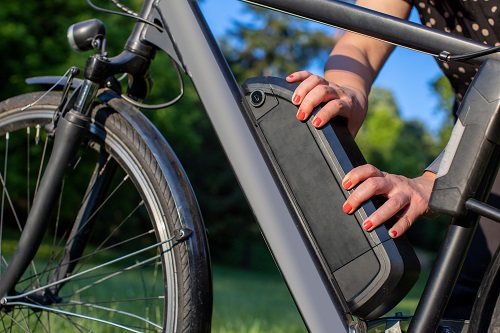
The hidden risks of lithium-ion batteries
By Adrian Simmonds, QBE Europe on 01 July 2025
With UK fire services now tackling at least three Li-ion battery fires a day, it’s clear that stronger regulation and enforcement is urgently required to prevent the sale, use and modification of poor-quality and potentially dangerous batteries used in e-bikes and scooters.