Machinery designed specifically for potentially explosive atmospheres will contain sparks that could trigger a fire or explosion. It’s essential it undergoes an independent inspection prior to initial use, in case the installer compromises the manufacturer’s design, invalidating the equipment and creating a potentially dangerous situation.
Features
Electrical installations in hazardous areas: why effective commissioning, installation and inspection are crucial
Machinery and other equipment used in potentially hazardous environments to automate or control certain production processes poses an increased risk of fire and explosion. This is because the normal operation of equipment often involves actions or reactions which represent a potential ignition source. Electrical equipment used in hazardous environments must therefore be expressly designed to minimise risks, and manufacturers of such equipment and systems must ensure that their products meet the requirements of applicable regulations and standards.
Photograph: iStock/NewSaetiew
Ex-rated equipment has been classified as safe for use in hazardous areas as it is designed to contain or prevent any sparks, flames or explosions, and poor installation can compromise its integrity. Conducting initial detailed inspections prior to first use will therefore help to identify potential installation quality issues, as well as ensuring the equipment is suitable for use.
In the UK, the UKCA Ex Regulation provides a detailed overview of the essential health and safety requirements applicable to equipment used in hazardous environments. The task of demonstrating compliance rests with the party responsible for introducing a product into the marketplace or putting into first use (for example, products that are made in-house).
In the European Union there are two ATEX Directives – one for the manufacturer and one for the user of the equipment. The ATEX 114 ‘equipment’ Directive 2014/34/EU focuses on the responsibilities of manufacturers of Ex-rated machinery and other equipment. In the UK, it is implemented by The Equipment and Protective Systems Intended for Use in Potentially Explosive Atmospheres Regulations 2016, which is law.
The legislation’s function is to ensure that the design and manufacture of equipment intended for explosive atmospheres conforms with the Essential Health and Safety Requirements, so that these are met before anything is placed on the market. This is typically achieved by third-party testing and certification by an Approved or Notified Body. However, after machinery has been installed, how can you verify that conformity and compliance have been achieved?
To ensure the installation quality and integrity of Ex-rated equipment post-installation, an intrusive inspection by a competent person should be carried out. This is described within the requirements of EN60079-17 as an ‘Initial Detailed Inspection’. If carried out correctly, such an inspection will ensure that the equipment, including its internal and external components, are fit for purpose and installed correctly.
Testing equipment intended for explosive areas
Manufacturers spend thousands of pounds designing and testing equipment intended for explosive areas, and typically the end-user will pay a premium for these products. So, if your installer compromises the manufacturer’s design, this invalidates the equipment and creates a potentially dangerous installation.
Ian Wright is operations manager, industrial products at TÜV SÜD. Photograph: TÜV SÜD
Also, assuming the issue is identified, there will be a significant financial cost to re-establish compliance. This is so often the case when an end-user takes delivery of, for example, a packaged skid assembly which has been manufactured off-site at a supplier’s premises. In such circumstances, Ex-related issues are only found during the completions, inspections and commissioning process. The consequence will be delays to commissioning and potentially start-up, alongside unplanned additional financial costs.
Installer competency is often a key issue. Keeping a core team of trades people as permanent employees is not always financially viable so it is common for suppliers and installers to hire workers for ad-hoc projects. This makes the assurance of installer competency a difficult area to manage.
However, the problem can be more systemic, and looking at the bigger picture the questions might be: did the supplier fully understand what they were asked to build and to what standard? Were the specifications and design documents supplied by the end-user or designer adequate? Did they cover the required legislative areas correctly and suitably? Were the appropriate standards referenced? At this point in a project disputes and frustrations are common, which can lead to further delays and cost – all of which can be avoided.
Importance of independent inspectors
Employing competent, impartial and independent Ex inspectors to inspect installations and carry out detailed inspections prior to initial use, or in the case of the suppliers, prior to shipping, is a key element to detecting and rectifying problems early. Engaging a competent inspector to monitor the build, offer advice and potentially mentor as the installation progresses is an area that is often overlooked. However, by doing so there is significant potential to minimise or eliminate the need of rework after inspection.
Another area that is commonly overlooked is the use of an independent and impartial specialist to review the technical documentation and project deliverables with respect to the installation of Ex electrical and non-electrical equipment. Design reviews, alongside build monitoring and inspection during the whole lifecycle of the project, will ensure both compliance and quality are achieved first time and on time.
Photograph: iStock/NewSaetiew
Ensuring that the supplier or installer knows exactly what they are tasked with delivering is key to ensuring the safe and successful delivery of new Ex installations. Specifying the scope and required level of competency is therefore vital, alongside the involvement of competent people in the design, procurement and installation to help to mitigate Ex compliance issues.
To be able to eliminate the potential ignition sources, which can include considered faults, prior to manufacture and installation, a pre-assessment is recommended to understand the equipment design, operation and desired location and environment.
Ian Wright is operations manager, industrial products at TÜV SÜD.
TÜV SÜD is a global product testing and certification organisation. For more information see:
tuvsud.com/en-gb/industries/manufacturing
linkedin.com/company/tuvsud
FEATURES
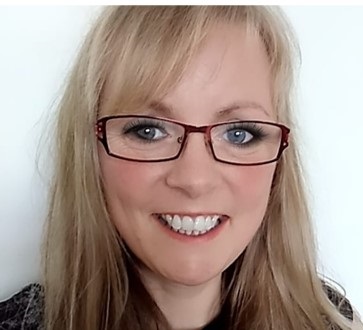
From crisis to prevention: the urgent role of employers in upstreaming health
By Dr Julie Riggs, British Safety Council on 16 June 2025
Poor public health and long-term sickness absence are placing extreme financial pressure on the UK’s health and social care system and the overall economy. However, by investing in workplace health prevention programmes and education initiatives, employers can help reduce the scale of ill health among the population and minimise the associated costs for society and business alike.
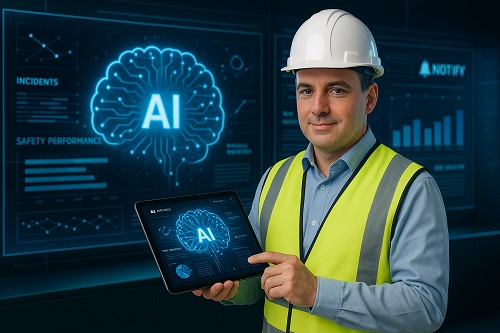
The AI safety revolution: augmentation, not elimination
By Alex Nichol, Notify Technology on 16 June 2025
Artificial Intelligence looks set to vastly reduce the amount of time and effort required to record, create and analyse occupational safety and ESG data, procedures and performance, while automatically providing insight into areas for improvement and areas of excellence.
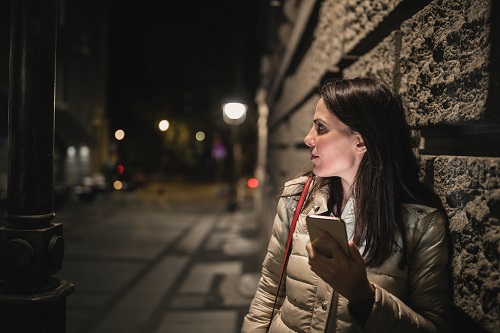
Protecting lone workers: a structured approach is critical
By Naz Dossa, Peoplesafe on 06 June 2025
Whether dealing with the public in their homes or working in remote locations, lone workers face a variety of risks to their health, safety and wellbeing. It’s therefore vital that employers systematically identify and assess the specific hazards lone workers face and then implement suitable measures to mitigate them.