Regular refresher training and ongoing monitoring is crucial for ensuring that forklift operators do not develop unsafe habits or suffer ‘skill fade’, but it’s essential that any refresher and monitoring programme is based on a thorough assessment of a site’s unique transport safety needs and day-to-day challenges.
Features
Forklifts: why regular refresher training and monitoring is key to operational safety
Thankfully, when it comes to forklift trucks, most reputable employers understand the need for basic novice training for new operators. Given the size and power of these machines, it’s easy to see why this is a recognised requirement.
Photograph: Mentor FLT Training
But what’s just as important is ensuring that any good work done initially to equip an operator to work safely is not lost as time goes on. Indeed, this vital reinforcement of best practice with regular monitoring and refresher training is where many businesses’ operational safety falls down.
Skill fade
It is human nature that the skills we possess will fade over time, if not honed and maintained. The consequences of this in the case of materials handling equipment (MHE) operation, however, can be severe. If allowed to develop, bad habits and complacency can lead to costly accidents and serious injuries, putting everyone in danger.
Although unsafe operators are a risk to their own safety, with the protection of the truck’s cab and seatbelt, they are not the most vulnerable, if an accident occurs. Unsafe operating practice is far more likely to put those around them at risk, whether this is their colleagues, visitors to site or even customers, in the case of premises open to the public.
Aside from the safety concerns, bad practice can also increase stock, truck and building damage, and hinder productivity should operations be disrupted or halted – all of which are detrimental to the profitability of the business.
Regular refreshers
To combat this ‘skill fade’, it’s vital that operators are consistently reminded of best practice, and the need to follow it every single day. Even a simple change of equipment, working environment or load type brings new operating conditions or characteristics that can soon compromise safety, if the additional risks aren’t considered.
A good place to start is implementing a refresher policy to ensure that operators receive periodic training to reassess their abilities, learn new skills (where appropriate) and reinforce good driving habits. This will help you to maintain a high level of competence throughout your operations.
With no specified forklift refresher period set out by law, choosing the right interval for you requires a sound understanding of your operational risks and how they should then influence your training schedules.
Implementing a refresher policy
As a guide, the generally recommended industry standard for refresher policies is every three to five years. But to ensure it is truly suited to your business, your policy should be based on a thorough risk assessment of your unique operations. Every workplace is different, and this tailored approach is vital to ensure operators receive the right frequency of training for the type of work they do, and the risks involved.
Though refresher training is widely adopted by UK businesses, a recent survey Mentor FLT Training conducted found that 20 per cent of respondents had not completed a risk assessment to specify its frequency. However, given that our survey was conducted primarily with businesses who are conscious of industry standards and HSE requirements, we believe that across the wider market, this proportion would be much greater.
Without the foundations provided by this risk assessment, companies may not be providing suitable training to their teams, which could see the risk of accidents and costly damage increase on their sites.
Similarly, if the quality of the training received is not verified or consistent, this may undermine the process. It is vital that when training does take place, that it is effective. When sourcing an external provider, look for those delivering accredited training, registered with an Accrediting Bodies Association for Workplace Transport (ABA) member body, for assurance that training is externally verified. Opting for these accredited courses will give you the peace of mind that all essential content is covered, by qualified instructors, and in line with the required industry standards.
Once the right training and timescales are established, the policy should be implemented and reviewed to ensure it is followed consistently by all and remains relevant as things evolve. To assist, some training companies can help employers to manage refresher requirements by holding records and issuing reminders to prompt when required training is due.
Though implementing a suitable refresher policy is an important process, it is not sufficient to simply implement a regular training interval and assume it will cover all eventualities. There are instances where refresher training or retesting may be required sooner.
The importance of monitoring
As the Approved Code of Practice for Rider-operated lift trucks (L117) states, “lift-truck operators, even those who are trained and experienced, need to be routinely monitored in the workplace and, where necessary, retested or refresher trained to make sure they continue to operate lift trucks safely”.
It is important that businesses supplement their refresher policies with regular monitoring and supervision, as additional training may be required outside of the specified intervals – for instance, if an operator has a near miss, has not used trucks for some time or if their working practices or environment has changed.
Without consistent monitoring, businesses are unable to confirm the current quality of operation taking place onsite, and whether safe practice is being followed day to day.
Our recent survey revealed that 24 per cent of respondents did not monitor operator ability in between refreshers, unless prompted by a concern raised. Again, given the nature of those surveyed, we can presume that, industry-wide, the number of businesses taking this approach is much higher.
Photograph: Mentor FLT Training
Rather than taking a reactive stance, regular monitoring can help to nip unsafe practice in the bud, before it develops into an issue. There are many different forms of monitoring that can be used where MHE operation takes place. As well as walking the floor, consider additional tools such as CCTV and telematics to help you identify any problem areas.
Utilising a variety of monitoring methods helps you stay informed and recognise when action needs to be taken, and the overall process can help you to significantly reduce the risk of accidents and injuries.
It’s also worth noting that, for the managers and supervisors that will carry out this monitoring, there is specialist training available to help them recognise what good and bad practice looks like and how it should be rectified, should they need it. Our feedback received from delivering such training to managers from large UK businesses suggests that, if implemented well, it does make a difference in terms of operational safety and understanding (as well as lowering costs, as a result of reduced accidents and stock damage).
In summary
Ultimately, it’s important to remember that even your best lift truck operators need regular reminders to ensure safe practice is followed consistently and complacency is kept at bay. By proactively ensuring that safety remains at the forefront of your operators’ minds, you can significantly reduce the risk of accidents and injuries on your site.
A relevant refresher policy, based on your operations, will ensure training is carried out regularly to reinforce key skills and safety messages. Following this up with continual monitoring will give you a true picture of current standards, allowing you to pinpoint any areas of concern which develop in the interim, for a comprehensive approach.
L117, the industry’s Approved Code of Practice
The Approved Code of Practice for Rider-operated lift trucks (L117) is the HSE’s definitive guide to forklift safety and training. Like all ACOPs, L117 has special legal status, so following its guidance will mean you remain on the right side of the law. If you are prosecuted for a health and safety breach, and it’s proven that you didn’t follow the relevant provisions in L117, you risk potential fines and prosecutions.
Within the publication, there is dedicated guidance on monitoring and refreshers, including the purpose and frequency of the training and suggested instances where refresher training or retesting may be appropriate for your operators.
For anyone involved in the management of lift truck operations, the ACOP is a vital resource to familiarise yourself with. Copies can be obtained from HSE.
Stuart Taylor is managing director at Mentor FLT Training.
For further information contact Mentor FLT Training:
T. +44 (0)1246 555222
FEATURES
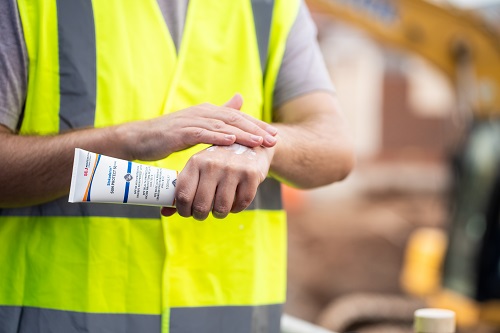
Facing the facts: protecting your outdoor workforce from UV exposure and skin cancer
By SC Johnson Professional on 11 July 2025
With outdoor workers at significant risk of skin damage, ageing and cancer due to exposure to the sun’s UV rays, it’s essential that employers in sectors like construction and agriculture create a working environment where sun safety precautions become the norm, rather than the exception.
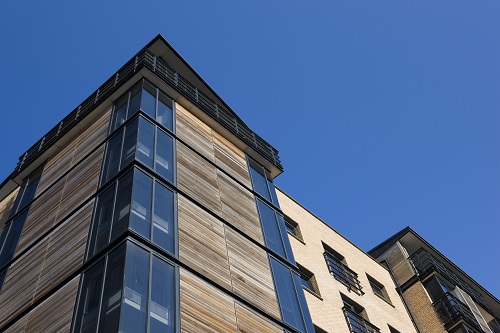
2025 UK fire safety regulation updates: a quick guide
By Chloe Miller on 11 July 2025
The regulatory landscape covering fire safety arrangements and structural features in domestic and commercial buildings has undergone a number of significant changes in recent years, making it essential for responsible persons to review their approach to keeping residents, workers and the nearby public safe from the risk of fire.
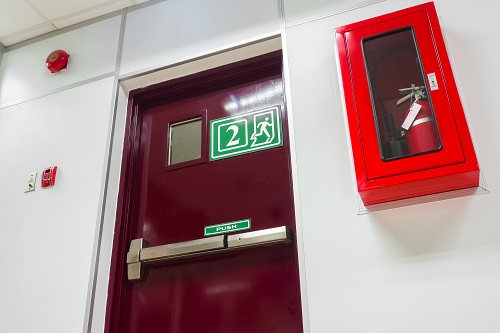
Tackling new fire risks as Fire Door Safety Week celebrates 12th year
By Helen Hewitt, British Woodworking Federation on 11 July 2025
The British Woodworking Federation’s annual Fire Door Safety Week this September will encourage duty holders such as those in charge of residential buildings to consider the dangers from lithium-ion batteries and ensure fire doors remain fit for purpose in reducing the risk should a battery-related fire break out.