When most people think of injuries in the materials handling industry, they picture serious incidents – severe trauma or even fatalities. However, a silent issue affects far more workers every day: musculoskeletal disorders (MSDs).
Features
The growing problem of MSDs in the materials handling industry
These not only cause physical discomfort but also hamper a worker’s ability to perform at their best, ultimately impacting the productivity of businesses.
Photograph: Mitsubishi Forklift Trucks
Readers will no doubt be familiar with the study by the Health and Safety Executive (HSE) 2022/23. It found that 473,000 workers in the UK are affected by MSDs daily, leading to the loss of more than 6.6 million working days every year. These figures highlight the scale of the problem, with MSDs representing one of the most significant occupational health challenges in the country. The impact of these lost days is substantial.
Yet, this issue is not just about downtime. Left unchecked, MSDs can lead to chronic health problems for the individual, increased absenteeism, and high turnover rates — all of which have long-term effects on the operation’s bottom line.
Understanding the impact of MSDs on workers and operations
The physical toll of MSDs on workers is apparent, but the knock-on effects for businesses are sometimes overlooked. When workers experience pain or discomfort from MSDs, their concentration and reaction times are reduced. This not only limits their ability to work effectively but can also put colleagues at risk, particularly in high-risk environments like warehouses or factories.
For example, forklift drivers suffering from MSDs are more likely to experience delayed reactions. This is catastrophic in fast-moving environments. Errors caused by diminished concentration can lead to accidents involving heavy machinery, endangering not only the driver but other employees in the vicinity. In industries reliant on forklifts, these risks are particularly high.
The financial costs associated with MSDs are equally worrying. According to HSE estimates, the annual cost to UK businesses is an estimated £675 million. This figure reflects both the complete absence of workers who take sick days and the reduced output of those who continue to work through their pain. Workers pushing through their symptoms are far less efficient, which can drag down overall team performance. Unplanned absences caused by MSDs can throw schedules off course, halt entire operations and leave employers scrambling to find replacements or adjust workflows.
What causes MSDs?
To effectively tackle the issue, businesses need to understand the causes of MSDs. There isn’t one single factor behind the problem. It’s a combination of factors that are commonly found in materials handling workplaces.
- Whole-body vibration: Employees working long shifts on vibrating machinery are particularly vulnerable. Prolonged exposure to vibration is known to increase the risk of developing chronic MSDs, and forklift drivers who often work eight-plus hour shifts are among the most affected workers. The vibration absorbed by the body over long periods contributes to joint and muscle strain, leading to both short-term and long-term musculoskeletal issues.
- Bumpy, uneven surfaces: In many warehouses, distribution centres, or work sites, operators navigate forklifts over uneven floors. These surfaces increase the level of vibration transmitted through the body, particularly to the spine. Over time, this can cause cumulative damage, leading to MSDs.
- Poor posture: Workers who spend long hours seated in less-than-ergonomic conditions are more likely to develop MSDs. The cumulative effects of poor posture combined with repetitive tasks can strain muscles and joints. Unfortunately, poor posture is often overlooked until symptoms worsen and affect the worker’s ability to perform their job.
- Lack of stretching or movement: Long, static shifts without adequate movement or stretching breaks create the perfect environment for MSDs to thrive. Muscles that remain tense and unused during long stretches of sitting or standing are more prone to injury.
Preventing and managing MSDs: ergonomics in equipment design
Given the scale of the problem, businesses should be looking for ways to reduce the risk of MSDs. One of the most promising approaches involves improving the ergonomics of the equipment that operators use daily.
Kirsty Cunningham is health and safety facilities manager at Mitsubishi Forklift Trucks. Photographs: Mitsubishi Forklift Trucks
Modern materials handling equipment has increasingly been designed with operator ergonomics in mind. By focusing on reducing whole-body vibration and improving operator comfort, manufacturers aim to reduce the long-term health impacts of MSDs. Investing in these ergonomic solutions is critical for businesses that want to protect their workforce and maintain efficiency.
Some of the most effective ergonomic features in modern trucks include:
- Dynamic power steering: This reduces strain on the operator’s arms, shoulders and back. The smoother the movement, the less force is required, which helps protect workers from developing chronic musculoskeletal issues.
- 360-degree steering: By allowing more controlled manoeuvring with less stop-start in turns, it reduces the physical demands on operators, especially in confined spaces. This helps alleviate the strain that could otherwise contribute to MSD development.
- Suspension seats: Trucks with advanced suspension seats are designed to absorb shocks and vibrations, particularly on rough terrain. This is especially beneficial for electric trucks, which typically lack suspension systems found in IC engine models. Suspension seats provide a smoother ride and help prevent chronic back pain and discomfort in operators.
Maintenance: the overlooked factor in MSD prevention
While investing in ergonomic equipment is an essential first step, it’s equally important to ensure that the equipment is regularly maintained. Poorly maintained trucks and machinery may experience mechanical issues that exacerbate vibration levels and operator discomfort. A well-planned maintenance schedule, ideally supported by a service agreement, can help businesses ensure that their equipment remains in good condition.
Regular maintenance helps to identify and fix issues that might otherwise go unnoticed, such as worn-out suspension components, loose parts, or other issues that contribute to increased vibrations. Keeping machinery in optimal working condition can prevent minor problems from becoming much more significant.
The role of training and workplace culture
In addition to ergonomic equipment and regular maintenance, businesses must prioritise comprehensive training initiatives to help workers prevent MSDs. Training courses can teach forklift operators how to maintain proper posture, how to handle equipment safely, and the importance of taking breaks during long shifts.
Training programs that focus on ergonomic best practices are particularly important. Workers need to understand how proper posture and positioning can help them avoid injury. They should also be taught techniques for adjusting their seat and controls to minimise the risk of vibration-related injuries. Additionally, training should highlight the importance of regular movement and stretching — particularly for workers who spend extended periods in a single position.
Photograph: Mitsubishi Forklift Trucks
Employers also need to ensure that workers take regular breaks. Warehouse shifts are often long, repetitive and fast-paced. Without adequate rest, workers are at higher risk of developing MSDs due to the constant strain on their muscles and joints. By building break times into work schedules, businesses can alleviate the tension and fatigue that contribute to development of these conditions.
Protecting employers and workers: the legal implications
Businesses also face legal risks if they fail to properly train their workers or ensure safe working conditions. In recent years, there have been several high-profile cases where companies have been fined for failing to provide adequate training. For example, a major UK supermarket was fined £1 million after one of its forklift operators was injured and the investigation found they hadn’t received sufficient training.
Providing comprehensive training not only reduces the risk of injury but also ensures that businesses remain compliant with health and safety regulations. Failure to do so can result in significant legal and financial consequences, as well as damage to the company’s reputation.
In summary
Musculoskeletal disorders present a serious challenge for both workers and employers in the materials handling industry. The physical strain of long shifts, whole-body vibrations and repetitive tasks take a toll on workers’ health, leading to reduced productivity, higher absenteeism and significant financial costs.
By investing in ergonomic equipment, maintaining a strong focus on equipment upkeep and providing comprehensive training, businesses can significantly reduce the risk of MSDs. These measures not only protect workers but also ensure that businesses remain productive and profitable in the long run.
Kirsty Cunningham is health and safety facilities manager at Mitsubishi Forklift Trucks.
For more information see:
T: 0845 3713048
FEATURES
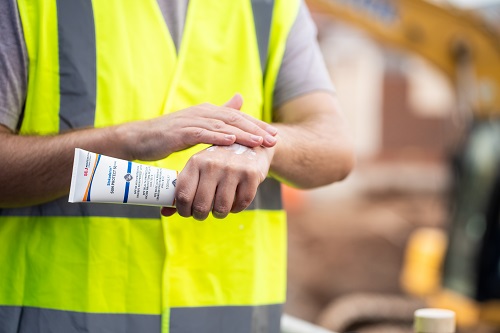
Facing the facts: protecting your outdoor workforce from UV exposure and skin cancer
By SC Johnson Professional on 11 July 2025
With outdoor workers at significant risk of skin damage, ageing and cancer due to exposure to the sun’s UV rays, it’s essential that employers in sectors like construction and agriculture create a working environment where sun safety precautions become the norm, rather than the exception.
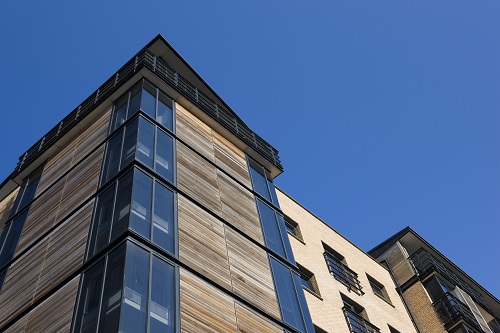
2025 UK fire safety regulation updates: a quick guide
By Chloe Miller on 11 July 2025
The regulatory landscape covering fire safety arrangements and structural features in domestic and commercial buildings has undergone a number of significant changes in recent years, making it essential for responsible persons to review their approach to keeping residents, workers and the nearby public safe from the risk of fire.
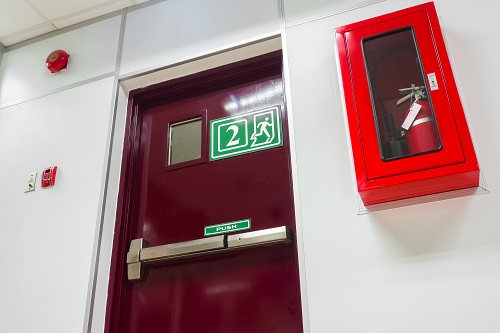
Tackling new fire risks as Fire Door Safety Week celebrates 12th year
By Helen Hewitt, British Woodworking Federation on 11 July 2025
The British Woodworking Federation’s annual Fire Door Safety Week this September will encourage duty holders such as those in charge of residential buildings to consider the dangers from lithium-ion batteries and ensure fire doors remain fit for purpose in reducing the risk should a battery-related fire break out.