Employers may need to carry out measurements of hand-arm vibration from hand-held tools and machinery to identify if workers are at risk of debilitating and permanent damage to their fingers, hands and arms, but it’s essential the measurement equipment is used in the correct way.
Features
Get a hold on HAVS, before it’s too late
Hand-Arm Vibration Syndrome (HAVS) is a medical condition caused by long-term exposure to the vibrations transmitted from hand-held machinery or power tools. The Health and Safety Executive (HSE) estimates that nearly two million people are at risk of developing the debilitating condition.1 When a person uses these types of tools for extended periods, there is a risk that the blood vessels, nerves, muscles and joints in the hand, wrist and arm may become damaged, which can lead to a range of symptoms. These typically are:
- Tingling or numbness – often felt in the fingers, hands or arms
- Loss of sensation or dexterity – difficulty feeling or manipulating objects with precision
- Pain or discomfort – typically, in the fingers, hands, wrists or arms
- Reduced grip strength – difficulty holding onto objects firmly
- White finger (Raynaud’s phenomenon) – the fingers may become white, numb and painful in response to cold or stress due to restricted blood flow.
Once someone develops HAVS, there is no cure. The condition may lead to the individual suffering from these symptoms permanently, impacting their ability to conduct fine work like the assembly of small components. In severe cases, HAVS can significantly impact the capacity for any hands-on work and performance during daily activities, such as difficulty fastening buttons.
Photograph: Casella
The severity of HAVS symptoms can vary depending on factors such as the duration and intensity of exposure to vibration, individual susceptibility and the specific characteristics of the vibrating tools being used.
Preventing HAVS involves implementing measures to reduce exposure to hand-arm vibration, such as using tools with lower vibration levels, taking regular breaks, maintaining equipment in good condition and providing training to workers on safe tool use practices. Additionally, early detection through health surveillance programmes can help identify and address symptoms before they worsen.
UK legislation
UK legislation regarding HAVS primarily falls under the Control of Vibration at Work Regulations 2005. These regulations were the first of their kind in the world to be implemented to protect workers from the health risks associated with exposure to hand-arm vibration. The key aspects of the regulations include:
- Employer responsibilities: employers are required to assess and manage the risks associated with hand-arm vibration in the workplace. This includes conducting risk assessments, implementing measures to control exposure, providing information and training to employees, and conducting health surveillance where necessary.
- Action Levels and Exposure Limits: the regulations set out action levels and exposure limits for hand-arm vibration. If employees are likely to be exposed above these levels, employers are required to take action to reduce exposure and protect workers’ health
- Health surveillance: employers are required to provide health surveillance for employees who are exposed to hand-arm vibration at or above the exposure action value. This involves monitoring the health of employees to detect and address any early signs of HAVS.
- Training and information: employers must provide suitable training and information to employees who are at risk of exposure to hand-arm vibration. This includes guidance on the risks associated with HAVS, how to use vibrating tools safely and the importance of reporting any symptoms or concerns.
- Control measures: employers must implement control measures to reduce exposure to hand-arm vibration, such as using alternative tools or equipment with lower vibration levels, providing rest breaks and maintaining tools and equipment in good working order.
- Monitoring and review: employers are required to monitor and review their control measures regularly to ensure they remain effective in reducing exposure to hand-arm vibration and protecting workers’ health.
Preventing HAVS involves implementing measures to reduce exposure to hand-arm vibration, such as using tools with lower vibration levels. Photograph: iStock
These regulations are enforced by HSE in the UK and failure to comply with them can result in legal action. Enforcement is increasingly resulting in large six figure fines for employers that fall short on safeguarding employees from exposure to harmful hand-arm vibration. It is important for employers to be aware of their legal responsibilities and to take appropriate action to protect the health and safety of their workers. The HSE publication ‘L140’ is a valuable source of information.
Safety data
As with all health and safety hazards, employers should carry out a risk assessment which begins with looking for sources of vibration data for the tool(s) in question. This data might be available in the tool’s handbook or from a database provided by HSE, which also publishes useful guidance on the regulations for hand-arm vibration, in the ‘L140’ guidance.
Regulation 4, for example, states that the daily Exposure Action Value (EAV) – the daily amount of vibration exposure above which employers are required to take action to control exposure – is 2.5 m/s2 A(8). The use of A(8) is intended to differentiate between the vibration magnitude of the tool itself and the daily exposure. There is also a level of vibration exposure that must not be exceeded, known as the Exposure Limit Value (ELV).
The magnitude of the vibration transmitted to the hand exists in three axes – x, y and z. As such, the acceleration magnitude of the vibration must be calculated in all three directions first, to ascertain the vibration magnitude. This is also frequency weighted, defined by British Standard BS EN ISO 5349-1:2001, and since the risk to health from vibration is affected by the frequency content of the vibration, it is measured over a range of about 5–1250 Hz, whereby lower frequencies are given greater ‘weight’.
Measurements
The latest HSE guidance seeks to clarify the position on measurement versus monitoring. Of the latter it says that “monitoring hand-arm vibration all the time is probably not a good use of resources” and that “monitoring alone is not enough to control risk”.3 The guidance also makes it clear that employers should not confuse monitoring systems with vibration measurement systems. It is only necessary to measure vibration magnitudes if suitable data cannot be attained through a risk assessment.
Tim Turney is Global marketing manager at Casella
However, if using a vibration meter, it should meet the correct specification given in British Standard BS EN ISO 8041 and specifically have the correct weightings. It is not unknown for people to use general vibration meters that are not suitable and therefore return inaccurate results.
An accelerometer is normally used to measure vibration. The accelerometer must be rigidly mounted to the handle of the tool at each hand position, and it is preferable to measure all three axes x, y and z at the same time. A vibration meter with a tri-axial accelerometer will do this, and also automatically calculate the acceleration magnitude. If fixed mounting systems are not feasible, Appendix D of BS EN ISO 5349-1 gives advice on the use of hand-held adaptors. Measurement results are unlikely to be representative if they are measured away from the palm of the hand, so it is essential that the measurement is taken from this position.
How many measurements?
The guidance states that a single measurement for a machine, an operator and a task provides limited information on vibration risk. This is because vibration magnitudes vary due to factors such as changes in forces, posture and techniques adopted by the operator as well as variation in materials and product.
When making measurements, you should plan to measure several operators, each working across a range of common operating conditions. Further guidance on carrying out vibration measurements can be found in HSE’s L140 document.
In conclusion, with reports of six-figure fines for employers for failing to carry out competent vibration risk assessment and/or health surveillance regularly featuring in the health and safety press, it is worth investing time and effort in conducting vibration measurements where necessary and appropriate. However, the measurements must be conducted properly, which means using compliant instrumentation with the sensor correctly fixed in place. Employers should also remember that while the terminology may seem daunting, there is a lot of explanatory guidance and expert advice available.
Tim Turney is global marketing manager at Casella.
For more information see:
casellasolutions.com
hse.gov.uk/vibration
FEATURES
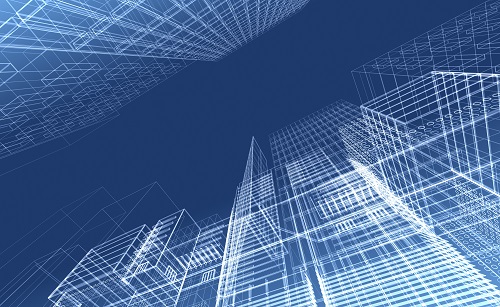
A year on – what have been the developments in competence management and the golden thread?
By Sofie Hooper, Association for Project Safety and Anthony Taylor, Resolve Risk Ltd on 03 July 2025
Last July the authors published an article in Safety Management where we looked at the expectations for those responsible for managing competence and those creating and managing the golden thread. In this edition we provide an update on both these key requirements of the Building Safety Act/Fire Safety Act’s ‘new regulatory regime’ including for higher-risk buildings (HRBs).
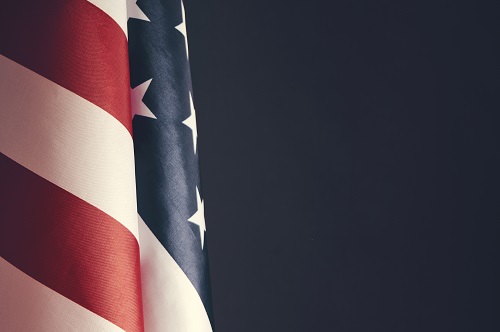
Stars, stripes and safety
By Belinda Liversedge on 02 July 2025
It seems like America today is rarely out of the news, particularly since President Trump won his second term. Our ‘special relationship’ with America has continued, with the country a strong pipeline for inspiration, products and trends.
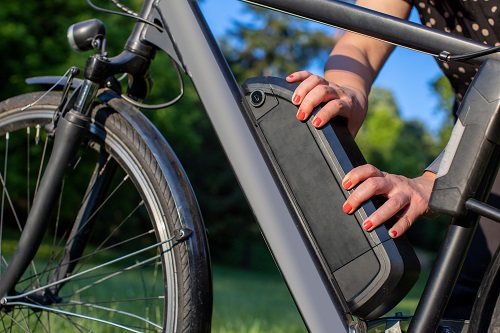
The hidden risks of lithium-ion batteries
By Adrian Simmonds, QBE Europe on 01 July 2025
With UK fire services now tackling at least three Li-ion battery fires a day, it’s clear that stronger regulation and enforcement is urgently required to prevent the sale, use and modification of poor-quality and potentially dangerous batteries used in e-bikes and scooters.