Machinery can deteriorate, malfunction or become unsafe when water or dust enters or if operators wrongly insert tools into the enclosure. It’s therefore vital to purchase plant that has been independently assessed to ensure it is robust enough to cope with the environment and the ways in which it will be used.
Features
Machinery at work: why it’s vital to only select plant that offers suitable ingress protection
Ingress protection (IP) testing reduces the risk of machine failure in real-life use in the field by assessing the degree of protection the equipment provides against mechanical intrusion, accidental human contact with the machine’s hazardous internal parts and dust and water intrusion into its casings and enclosures.
However, sourcing equipment that reacts well to the threat of intrusion has its challenges as, for example, even the smallest sealing flaws will result in water ingress into machinery.
IP69 rated machinery is effective against powerful high-temperature water jets used in environments that require a more stringent washdown. Photograph: TÜV SÜD
As machinery can deteriorate, malfunction or become unsafe when water or dust enters, it’s vital to ensure that it has the correct protection for its intended use. ‘IEC 60529 – Degrees of Protection provided by IP Code’ is the standard that must be followed. This standard contains the criteria for assessing equipment to its appropriate IP Code, and there also are sub-standards for IP protection for machinery designed for specific industry sectors, such as food processing and pharmaceuticals. This ensures machinery is robust enough to deal with the environment within which it has been installed.
Types of ingress protection
The International Electrotechnical Commission’s (IEC) ingress protection ratings grade an enclosure’s level of resistance to items entering it, defining three different types of ingress protection that an enclosure could provide:
1. The protection of human access to hazardous components within an enclosure
2. The protection of equipment from solid objects, including dust
3. The protection provided by an enclosure against the ingress of water.
The IP Code consists of the letters IP followed by two digits and an optional letter. The first digit indicates the level of protection that the enclosure provides against access to hazardous parts and the ingress of solid foreign objects. It is rated on a scale from 0 to 6:
• 0 – no protection against the penetration of solid particles, objects or dust
• 1 – the equipment is protected against any solid object larger than 50mm
• 2 – the equipment is protected against any solid object larger than 12.5mm
• 3 – the equipment is protected against any solid element larger than 2.5mm. For example, if a machinery operator attempted to insert fine tools, etc.
• 4 – the equipment is protected against any solid object larger than 1mm. For example, larger types of tools or screws, etc.
• 5 – the equipment is partially protected against dust. This rating means that while dust can enter crevices within the equipment, it cannot damage it, and that contact is not possible.
• 6 – the equipment is completely dustproof, so that dust is unable to enter crevices and the equipment cannot be soiled or damaged.
Darren Hugheston-Roberts: "IP testing minimises the risk of product failure in the field by assessing the degree of protection against mechanical intrusion, dust, accidental contact and water into casings and enclosure."
The second digit indicates protection of the equipment inside the enclosure against harmful ingress of liquids, using a scale from 0 to 9. This covers both the amount of water and the depth of immersion, including the power of a jet. The additional letter can be appended to classify only the level of protection against access to hazardous parts by persons:
• 0 – no protection against moisture or any liquid coming into contact with the equipment
• 1 – the equipment is protected against liquid falling vertically only
• 2 – the equipment is protected against drops falling at an angle of 15 degrees
• 3 – the equipment is protected against liquid sprays in all directions, provided that they do not exceed an angle of 60 degrees
• 4 – the equipment is protected against splashing
• 5 – the equipment is protected against water projections
• 6 – the equipment is protected against powerful water jets. For example, if equipment is being cleaned with a high-pressure device
• 7 – the equipment is waterproof up to a depth of 1m
• 8 – the equipment is waterproof beyond a depth of 1m, so water may be able to seep into the equipment, but it cannot damage it
• 9 – the equipment can resist high-pressure hot water from different angles.
For example, IP69 rated machinery is effective against powerful high-temperature water jets used in environments that require a more stringent washdown, while IP66 is effective against powerful water jets.
Supplementary letters are used to designate:
• F – Oil resistant
• H – High voltage apparatus
• M – Motion during testing
• S – Stationary during testing
• W – Weather conditions.
Meanwhile, other letters denote access to hazardous parts:
• A – Protection from back of hand access
• B – Protection from finger access
• C – Protection from tool access
• D – Protection from wires.
Post-manufacture additions
However, simply specifying an IP-rated machine does not cover the fitting of any post-manufacture additions, such as push buttons and indicator lights. Neither does it allow for any necessary drilling into the enclosure that is required for the addition of power cables once the machine is on-site.
Also, factories are likely to spray water at much closer distances than those stipulated in the IP-rated tests.
Although high-pressure washdown cleaning techniques enhance cleaning efficiency – and reduce water and detergent usage, thereby minimising costs and environmental impact – they can impact the machine’s integrity, creating potential leakage points. To ensure problem-free operation in washdown areas, it is therefore important to maintain the ingress protection rating during assembly and installation.
Reduce the potential of ingress through machine design
Enclosure designs that reduce the potential for ingress in the first place will also enhance long-term protection from ingress.
For example, although water ingress protection is a key factor to consider when selecting equipment for use in washdown areas, there are other aspects that also need to be taken into account, including the material used in the fabrication of the equipment.
While many materials cannot withstand regular exposure to water from washdown operations, stainless steel can. For this reason, grade 316 stainless steel is usually specified for equipment that will be used in washdown as it has better corrosion resistance than other commonly available grades. Also, machinery that faces fluctuating temperatures, combined with heat-generating electrical circuits, will often cause condensation within the machine’s housing. As this can attack terminals and damage protected components, an anti-condensation system should be used.
IEC 60529 not only defines the different levels of protection provided by enclosures but also outlines the test methods required to verify that level of protection. IP testing minimises the risk of product failure in the field by assessing the degree of protection against mechanical intrusion, dust, accidental contact and water into casings and enclosure. This ensures that machinery remains functional, reliable and safe for operators.
TÜV SÜD is a global product testing and certification organisation. For more information see:
tuvsud.com
E: [email protected]
linkedin.com/company/tuvsud
Darren Hugheston-Roberts is senior manager, digital & industry solutions at TÜV SÜD/
FEATURES
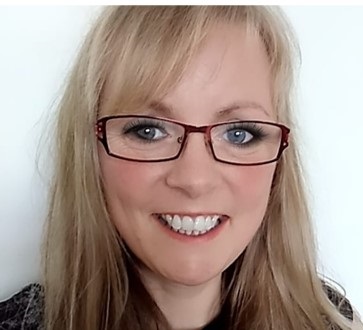
From crisis to prevention: the urgent role of employers in upstreaming health
By Dr Julie Riggs, British Safety Council on 16 June 2025
Poor public health and long-term sickness absence are placing extreme financial pressure on the UK’s health and social care system and the overall economy. However, by investing in workplace health prevention programmes and education initiatives, employers can help reduce the scale of ill health among the population and minimise the associated costs for society and business alike.
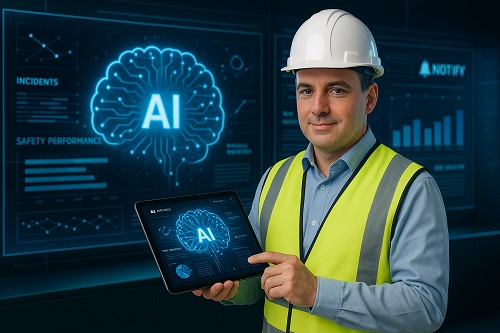
The AI safety revolution: augmentation, not elimination
By Alex Nichol, Notify Technology on 16 June 2025
Artificial Intelligence looks set to vastly reduce the amount of time and effort required to record, create and analyse occupational safety and ESG data, procedures and performance, while automatically providing insight into areas for improvement and areas of excellence.
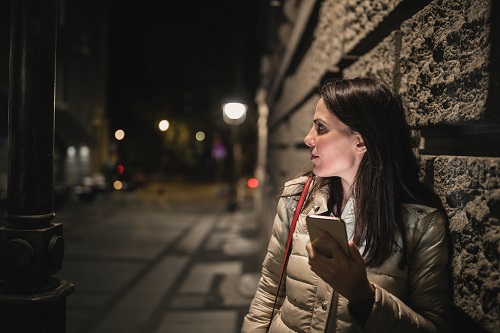
Protecting lone workers: a structured approach is critical
By Naz Dossa, Peoplesafe on 06 June 2025
Whether dealing with the public in their homes or working in remote locations, lone workers face a variety of risks to their health, safety and wellbeing. It’s therefore vital that employers systematically identify and assess the specific hazards lone workers face and then implement suitable measures to mitigate them.