Conventional noise control techniques for plant and machinery incorporate considerable embodied carbon due to the volume and types of materials used – and often result in higher energy demand due to problems like an increased need for cooling fans. However, adopting modern analysis and engineering processes means the costs and carbon footprints of typical noise control projects can be cut by up to 90 per cent.
Features
The sustainable approach to noise control carbon footprints
The environmental impact of conventional noise control
Both environmental and occupational noise control projects traditionally generate significant quantities of both waste and carbon dioxide (CO2) greenhouse gas emissions. In the case of hearing conservation programmes, these include:
- PPE: earmuffs and earplugs – continuous generation of plastic waste because it is often wrongly assumed that noise reduction is not practical
- Noise control measures: the material types and material quantities used in conventional noise control measures, such as enclosures and silencers on plant and machinery, and the manufacture, transportation and installation processes include considerable embodied carbon
- Power consumption: continuous additional CO2 emissions due to the additional power required by increased cooling requirements (enclosures) and the reductions in fan efficiency caused by adding silencers.
Photograph: iStock/RealPeopleGroup
Conventional noise control solutions rely on bulky, material-intensive structures. Acoustic enclosures (for example, on machines) require substantial amounts of sheet metal and acoustic absorbent materials. Manufacturing these materials, transporting them to site and eventually disposing of them contribute significantly to embodied carbon. Furthermore, enclosures impede access for maintenance, leading to increased downtime and resource consumption.
Similarly, traditional silencers use large quantities of absorptive materials like fibreglass, mineral wool and foams. While acoustically effective, these materials have environmental drawbacks related to their production processes and end-of-life management. The ‘pressure-drop’ introduced by silencers also increases the energy consumption of fans and blowers, leading to higher operational carbon emissions.
‘Greener quieter’ benefits
The use of modern diagnostic techniques and engineering noise control technology can dramatically reduce the environmental impact of noise control projects. In some cases, projects can even be rendered carbon negative by increasing system efficiency to reduce power consumption.
The benefits of the ‘greener quieter’ approach to engineering noise control include:
- Waste: minimising or eliminating plastic waste by reducing or eliminating the requirement for hearing protectors
- Material quantities: dramatically reduces the quantities of material used on noise control projects
- Material types: the use of ‘greener’ acoustic materials, such as acoustic absorbent made from recycled plastic bottles, instead of the virgin materials commonly installed, is more sustainable
- Manufacture and transportation: choosing local manufacturers for noise control materials eliminates or reduces the environmental and financial impact and cost of transporting them to the required site
- Installation and maintenance: engineering source control techniques are quicker and easier to install with less (or no) downtime
- Power consumption: reduced cooling requirements and improved fan efficiencies reduces power consumption. It is even possible for aerodynamically silenced fans to use less power than unsilenced units, let alone fans fitted with silencers. In fact, organisations worldwide are currently using aerodynamic noise control technology to reduce fan power consumption by many megawatts – every hour of every day.
It is therefore time to cut the carbon costs of noise control projects.
Implementing more sustainable options
At INVC, we take a more sustainable approach to noise control that emphasises the importance of diagnosing the precise noise generation mechanisms before considering potential solutions. This makes use of advanced techniques to identify the root causes of noise problems, rather than simply treating plant as immutable noisy objects onto which you apply noise control structures and materials.
Step 1: accurate diagnosis
We suggest duty holders carry out, or commission, a detailed analysis of all the potential noise sources to pinpoint and rank the specific components or processes that contribute to the overall noise level.
At INVC, we use techniques such as narrow band frequency analysis and vibration analysis coupled with simple plant operational tests and an extensive library of past diagnostic results.
The diagnoses for an increasing proportion of our noise control projects can be carried out virtually without a site visit, making projects both faster and eliminating travel carbon. This has become possible due to the developments in smartphone technology that can even allow for the virtual presence of an expert on the shoulder of a site engineer.
Accurate diagnosis therefore enables the development and implementation of precisely targeted engineering noise control measures.
Common examples that INVC has drawn up and implemented at workplaces include:
Cyclone separator: detailed diagnosis proved that the 110dB(A) noise level was dominated by a flow-induced acoustic resonance. Our solution was to design and insert an A4 size formed steel panel into the cyclone that cut the noise by 25dB(A).
This effectively zero carbon (and zero cost) solution was installed instead of the proposed extensive foam and mass-loaded vinyl acoustic lagging and a pair of silencers.
Power press: we used the frequency analysis shown in the graph below to diagnose that the dominant noise from a large power press was down to flywheel resonances. All previous investigations had just stated “the noise level is 100dB(A)”, which basically meant there had been zero diagnosis by previous noise control assessors.
Instead, our analysis meant we could design and fit £15 worth of small, tuned vibration absorbers to the flywheel inside the existing guards. Coupled with a quiet nozzle using 20 per cent less air, the overall noise was reduced by 15dB(A).
This low-cost noise reduction solution, with reduced electricity consumption, is a stark contrast to the suggestion from other noise assessors to install a £30k acoustic enclosure to attempt to reduce noise at work. As well as costing a great deal more, the subsequently rejected £30k acoustic enclosure would have significant embodied carbon emissions and would have affected plant productivity and ease of maintenance. It would also have required a cooling fan to be run continuously, increasing power consumption.
Source: INVC
Step 2: engineering noise control techniques
Traditional noise control measures are based almost entirely on palliative ‘add-on’ measures such as acoustic enclosures (including lagging), barriers and silencers. These solutions are not based on detailed diagnosis – they simply accept that there is a noisy item of plant and that the only noise control option is to add structures to reduce the spread of the noise.
The low carbon and more sustainable alternative approach to noise control is based on a precise diagnosis of the mechanisms responsible to determine which minor engineering modifications could be made to reduce the noise at source.
If this is not practical, then, and only then, should conventional measures be considered.
There are many engineering noise control at source techniques, ranging from those that are quite generally applicable to one-off solutions for particular sources. Some of the more general options include:
- Vibration damping and isolation – for example, using rugged, low-cost sound damped steel
- Controlling impacts via geometric and material changes or via cushioning
- Improving tolerances on key elements – for example, a specific gear pair
- Eliminating structural resonance excitation by changing the stiffness of elements
- Eliminating acoustic resonances by changing geometry or via tuned absorption
- Improving the efficiency of fan or combustion systems via aerodynamic technology
- Retro-fit aerodynamic components to reduce fan noise at source.
The following are case studies that illustrate the benefits of this more sustainable approach.
Dust control fans
These fans (pictured below) are used to prevent the build-up of potentially explosive layers of dust in buildings. Each fan generated 87dB(A) at 3m, making them the dominant noise source in buildings with multiple fans. We developed aerodynamic noise control measures that not only reduced the overall noise by 75 per cent (6dB(A)) but also increased the fan performance by 17 per cent while simultaneously cutting power consumption by nearly seven per cent. The performance and reduced running costs meant that the noise control modifications would have been implemented even if the fans had not been noisy. A very carbon negative noise control project.
Source: INVC
Pneumatic noise sources
Instead of converting the box round this camshaft washer drying station (pictured below) into an acoustic enclosure, the air-jets were replaced with carefully designed high efficiency nozzles. These not only cut the noise by 12dB, but they also reduced both the air consumption and the drying cycle time by 20 per cent, rendering the project very self-financing due to lower energy costs and increased productivity. This is a common benefit of the source control approach to pneumatic noise problems.
Photograph: INVC
Vibratory moulds, hoppers and feeders
A vibratory concrete tile mould generated 99dB(A). The proposed enclosure would have been costly, would have used considerable material quantities and would have impacted maintenance and productivity. The engineering alternative was to re-tune the vibratory system to feed more energy into the concrete and less into the structures at a cost of around £100 plus a fitter for a half day. This cut the noise by 15dB(A), the cycle time by 25 per cent and the power consumption. A carbon negative noise control project.
Coupled with subtle geometry changes, 5dB–25dB noise reductions can often be achieved for vibratory feeders and sieves via controlled damping that has perhaps one per cent of the embodied carbon of enclosures. This type of controlled damping can also improve productivity and reduce maintenance by eliminating fatigue cracking.
Granulators
These can be large, very noisy machines, generating 100dB(A) or more. Conventionally, they are fitted with substantial acoustic enclosures. The low carbon source control alternative in this case was to design a web damper coupled with retrofit internal modifications. These provided more attenuation (18dB) than the enclosure at around five per cent of the embodied carbon, 17 per cent of the cost and without affecting access or maintenance.
Large fans
Retrofit aerodynamic noise control techniques increasingly used round the world are currently saving megawatts of power all day, every day on large fans (example pictured below).
Photograph: INVC
‘Green peace’ noise control: a virtuous circle
The default attitude to noise control is that it involves the purchase of costly add-on equipment and components that cause production, maintenance and operational issues. These negative assumptions mean that noise is not reduced nearly as often as it should be, to the detriment of both occupational and environmental health. Ironically, where this flawed approach is implemented, these default solutions create unnecessary environmental damage due to embodied carbon and increased power consumption.
These drawbacks can very often be minimised or even reversed by taking a more sophisticated approach based on precise diagnosis and the use of modern ‘greener quieter’ engineering source control technologies. This dramatically cuts the capital and operational costs and the carbon footprint of noise control projects. It can even reduce power consumption by increasing plant efficiency to render projects carbon negative.
Lower costs. Less or no impact on productivity. A much reduced or even a positive impact on the climate. What’s not to like?
Peter Wilson is technical director at Industrial Noise and Vibration Centre (INVC).
For a comprehensive list of online resources on noise control at work from a variety of organisations, see:
invc.com/resources/technical-notes-occupational-noise/nihl-risk-management-online-resources/
For more information see:
T: +44 (0)1753 698 800
FEATURES
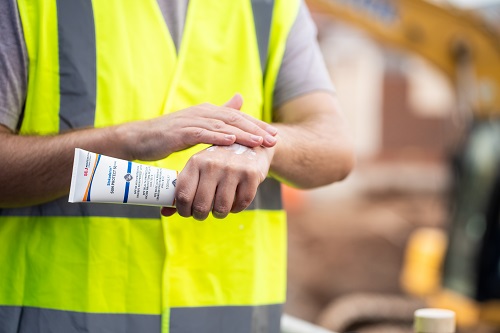
Facing the facts: protecting your outdoor workforce from UV exposure and skin cancer
By SC Johnson Professional on 11 July 2025
With outdoor workers at significant risk of skin damage, ageing and cancer due to exposure to the sun’s UV rays, it’s essential that employers in sectors like construction and agriculture create a working environment where sun safety precautions become the norm, rather than the exception.
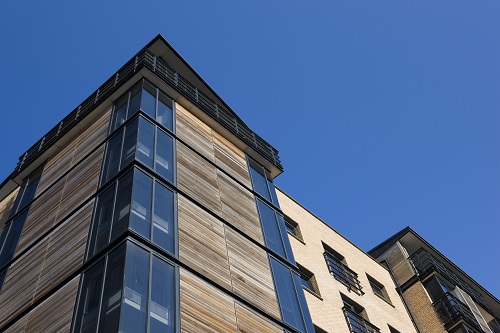
2025 UK fire safety regulation updates: a quick guide
By Chloe Miller on 11 July 2025
The regulatory landscape covering fire safety arrangements and structural features in domestic and commercial buildings has undergone a number of significant changes in recent years, making it essential for responsible persons to review their approach to keeping residents, workers and the nearby public safe from the risk of fire.
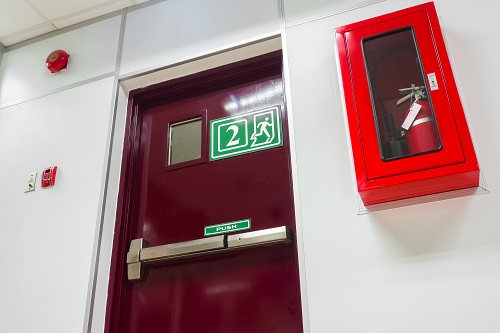
Tackling new fire risks as Fire Door Safety Week celebrates 12th year
By Helen Hewitt, British Woodworking Federation on 11 July 2025
The British Woodworking Federation’s annual Fire Door Safety Week this September will encourage duty holders such as those in charge of residential buildings to consider the dangers from lithium-ion batteries and ensure fire doors remain fit for purpose in reducing the risk should a battery-related fire break out.