Employers need to provide workers with effective hand protection solutions when doing manual handling.
Features
Get a grip
If you think about manual handling injuries, you could be mistaken for automatically considering back and lumbar injuries as a result of lifting excessively heavy or awkward loads. But drill down into the latest injury statistics from the Health and Safety Executive (HSE) and it’s clear that there is much more to consider when it comes to protecting workers against manual handling risks.
Aside from the bodily stresses and strains associated with lifting and shifting heavy loads, manual handling is as likely to result in hand and arm related injuries to workers including:
- Trapped fingers
- Cuts from contact with sharp objects
- Wider mechanical injuries from pushing and pulling loads using bodily force
- Sprains
Hands are more sensitive to pain than almost any other part of the body
Add in factors such as specific loads that are difficult to grasp because of shape or a wet or greasy surface, the number of times a worker picks up or carries an item and the distance they are carrying it, and the issue of hand protection and grip performance magnifies significantly.
According to HSE in 2017/18 there were 197,000 upper limb injuries as a result of manual handling. This accounted for 42 per cent of all manual handling injuries, resulting in an estimated 2.7 million lost working days. Manual handling accounted for 32 per cent of all reported injuries to the HSE.
And while most of them may not be life threatening – they can and do impact on the quality of life of workers along with worker absence levels.
Not just a lifting issue
While many may perceive manual handling to be predominantly a back issue, it is interesting to note that, of all reported manual handling-related injuries in the UK, 23 per cent of them are related to the hand, arm and wrist compared to 29 per cent relating to the lumbar region, according to HSE’s latest statistics.
Managing hand protection in manual handling
There are a number of key factors to consider when looking at providing effective hand protection and grip performance to minimise the risk of manual handling injuries, including:
- Glove sizing and comfort
- Glove material
- Grip performance
- Impact protection.
The importance of correct glove sizing and comfort
You wouldn’t provide workers with safety boots that are two sizes too
small or big, for obvious reasons, the main one being they could actively contribute to an accident. The same applies to head and respiratory protection, because correct sizing is critical for safety.
And this is absolutely the case in hand protection. Yet, still the vast majority of workers don’t have their hand measured or have any idea what size their hands are. As a result, getting the right ‘fitting’ glove can become a lottery.
So, in manual handling situations correct glove sizing is essential – especially when it comes to grip and comfort. Get this wrong either way and one of two things can happen:
- The glove is too loose and the hand will slip inside it, affecting general grip and increasing the risk of dropping an item, or
- The glove is too tight and the hand will quickly fatigue – again affecting the ability to grip when carrying loads.
Even a glove with a high performance grip coating will be compromised if the glove is too big for the wearer. So, it’s important to know workers’ hand sizes so the glove fit can be accurate.
Importance of comfort
Glove comfort is equally critical as it will help reduce hand fatigue and, by doing so, improve productivity and wearer confidence. The flexibility and dexterity of the glove are key considerations. This is where the thickness of the glove needs to be considered against the protection required.
If cut protection is important, new yarn technology means 15 & 18-gauge yarns provide enhanced cut protection, which also improves the dexterity significantly. Previously, that same level of cut protection would have required a thicker 13-gauge yarn. For that reason it is important that employers keep abreast of the latest glove materials available as they could bring measurable benefits over traditional hand protection solutions.
For greater levels of grip, particularly in wet environments, consider nitrile foam glove coatings, which have gone through a double dipping process
Second skin options – ensuring a sense of touch
The human hand contains a high density of nerve endings compared to any other part of the body. Not only does this enable the hands to carry out extremely complex tasks, they are also more sensitive to pain than almost any other part of the body.
Within the fingertips, rapid adapting receptors in the nerve endings deliver information on changes of surface, while the slowly adapting receptors deliver information regarding prolonged touch when carrying something for a longer period of time.
When we cover these receptors with glove materials, that level of vitally sensitive information can be minimised. So, where workers are undertaking manual handling tasks and sensitivity of what they are holding is important you should consider thinner second skin gloves.
While the glove material may be thinner, they can offer excellent levels of durability and grip in both wet and dry environments as well as cut resistance up to level four.
Select the right glove material
Glove material development and, in particular, glove coating technology enhances the level of grip performance offered for specific environments and particularly in wet and greasy environments. If grip protection is required, latex and nitrile coated gloves offer great performance for different environments (as a general rule of thumb latex in dry and nitrile in wet conditions).
For greater levels of grip, particularly in wet environments, consider nitrile foam glove coatings, which have gone through a double dipping process. The initial nitrile dipping process provides the glove with liquid proof undercoat. Once dried, the glove is then dipped again, adding a foam nitrile coating on top. This coating helps absorb liquids, drawing them away from the surface of the glove and by doing so improving grip – particularly effective in wet and oily environments.
Impact protection
Trapped fingers are one of the main manual handling injuries. Where there is a risk of this occurring from the task being carried out, you may want to consider enhanced impact protection.
Leading manufacturers offer the combination of foam nitrile with the addition of Thermo Plastic Rubber (TPR) shields added to the back of the fingers and hands, enhancing impact and crush protection.
By bonding these rather than stitching them, the glove is able to flex and move with the hand making it more comfortable for the wearer and as a result increasing wearer compliance.
With thousands of hand-related manual handling injuries annually, it makes sense to ensure that you are giving workers a hand protection solution that is not only going to protect them from physical hazards but ensure the integrity of the load they are carrying or handling.
Manual handling guide available here
More information available at: globus.co.uk
Gregory Tessier is Product Development manager – hand protection at Globus Group
FEATURES
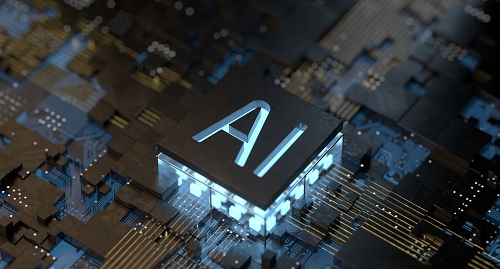
Why quality data is essential when using AI for occupational safety and health management
By Dr Bob Rajan-Sithamparanadarajah. Safety Groups UK (SGUK) on 01 April 2025
Artificial intelligence-powered models, systems and technology have the potential to significantly improve the management of occupational safety and health (OSH) risks, but it is vital that OSH practitioners understand the limitations and dangers of using AI to protect people at work.
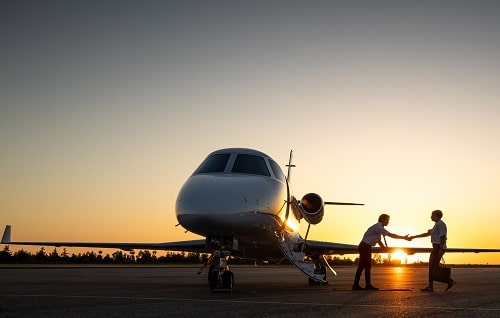
Sustainable aviation fuels: how do we put the SAFety in SAF?
By Megan Hine, Draeger Safety UK on 01 April 2025
Sustainable aviation fuel is seen as having great potential to reduce the greenhouse gas emissions from air transportation. However, as with other emerging renewable energy sources, the safety risks arising from the production, processing and storage of these biofuels can be accompanied by new risks and will require careful management from the safety industry as utilisation increases to meet the Government’s mandatory targets.
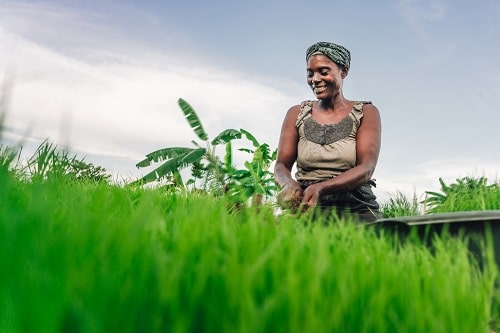
Why social sustainability should be a priority for health, safety, environmental and compliance professionals
By Agnes Chruszcz, IEMA (Institute of Environmental Management and Assessment) on 01 April 2025
By embedding social sustainability principles into their policies and operations, organisations can not only improve quality of life for their employees, workers in their supply chains and the communities they interact with, but boost their business resilience, productivity and reputation.