Just three years ago, Farrow & Ball, the well-known manufacturer of paint and wallpaper with offices in Dorset and showrooms around the globe, decided to join the British Safety Council (BSC). It was an easy and, in a way, predictable route in the safety journey the company initiated back in 2006, when they achieved their first ISO accreditation.
Features
Painting the walls of safety
With safety at the core of their manufacturing activities and while managing a complex network of employees, the company decided to reach out to the British Safety Council to get the information, support and challenges needed ‘to become the best’, as Lee Davis, the global safety, health and environmental manager put it.
Come 2019 and they received their first International Safety Award for their Dorset site, an accolade that has inspired them to keep going forward and apply for the extremely prestigious Sword of Honour Award.
Lee Davis, global safety, health and environmental manager with Farrow & Ball, shares with Safety Management his own trajectory in the company, the processes in place to increase safety standards and his enthusiasm for contributing to make Farrow & Ball a better place to work.
What are the main safety risks you face in your operations
As you can imagine, safety and environmental undertakings are varied from market to market and we understand that with global operations, occupational health, safety and the environmental aspects present several challenges. Along with increasingly demanding supply chains, this requires that our occupational health, safety and environmental management system should be properly aligned at an international level.
Lee Davis and Michaela Mattocks, SHE advisor, at their Dorset premises.
Manual handling is always a risk within retail and more so within manufacturing. For me, prevention means good guidance and training, mechanical aids and strict processes.
If we can engineer out manual handling as far as reasonably practicable, we do.
During our manufacturing process we use various powder raw materials, so due to the nature of the environment and loading activity we must ensure significant controls are in place, to reduce Work Exposure Limits (WEL) for our employees. We are currently reviewing and implementing a manufacturing design study, and have implemented Respiratory Protective Equipment (RPE), Local Exhaust Ventilation (LEV) and loading controls.
Air monitoring has recently been completed, assisted by Environmental Essentials Ltd, and we are significantly below the work exposure limits. We have also recently reviewed all our training to guarantee compliance and decrease the likelihood of incidents.
Farrow & Ball uses powder raw materials to manufacture paint, and significant controls are in place to reduce Work Exposure Limits (WEL) for its employees
Role and responsibilities
I have worked at F&B for over 20 years, however, not always in a safety role. I’ve supervised in some capacity for every operational department, from manufacturing to warehousing at our Dorset head office. I eventually moved into a new role completing special projects for the business, to develop our ISO Management System in safety and environment.
This was my formal entrance to the world of safety, health and environment (SHE), in 2004. At the time we recognised that as a growing business, there were areas for improvement, so we started to use the ISO systems to assist us to get to the safety level we are at today.
As part of the Key Management Group at Farrow & Ball, I manage our Integrated Safety, Health and Environmental Management System. This now covers ISO 45001:2018 (occupational health and safety management systems) and ISO 14001:2015 (environmental management systems), which together with our certification body United Registrar of Systems (URS) have helped to ensure we are compliant with legislation and capable of developing a good SHE practice globally.
I facilitate all external audits such as the British Safety Council Five Star Audit process, ISO certifications, Energy Savings Opportunity Scheme (ESOS) and, through trend analysis, continue to develop our global zero harm SHE strategy.
Farrow & Ball joined the British Safety Council in February 2016: "We realised that the resources and support we would obtain would be paramount to our activity in progressing to be the best."
I also complete internal auditing at our locations to establish and enhance our systems in line with our zero harm strategy, allowing me to listen to our colleagues. The feedback concerns and on how we could continue delivering good safety practice, and what is reasonably practicable to achieve, are essential. Via this process, we have then gained ownership of the issues among employees and particularly behavioural-based safety awareness. I also support legal visits from HSE and the local authority when they occur.
I have worked together with my colleague Michaela Mattocks (SHE advisor) for the past seven years; she supports all areas of our global zero harm strategy, keeps our systems in order, supports all our onsite SHE champions and our UK showroom network. Michaela’s current project is facilitating our behavioural based safety program globally.
Individually and collectively as a company we all have responsibilities and the systems we develop assist in our success and support our drive for business excellence, but you need the people to own it.
Health and safety culture
Two of our company values are accountability and care. That means that we work together with transparency and respect, and we also consider the impact we make on each other, the future of the company and the world.
Safety is our number one focus in all activities. And our zero harm ethos means that at the end of the day we want our colleagues to go home safe. With over 600 employees and 63 sites globally, we must ensure managerial and employee safety culture is nurtured. This is why we have changed our approach from ‘tell and do’ to ‘challenge and engage’; this way we seek others’ views before deciding, involve them in decision making; it treats people as individuals.
When and why did you join the BSC
We joined the BSC in February 2016 as we realised that the resources and support we would obtain would be paramount to our activity in progressing to be the best. The Five Star Audit programme and the immense guidance that it provided, really challenged us to lay our foundations in an enhanced safety strategy; our membership of the BSC has given us access to online training, and information in all industries. We also felt that being members of such a prestigious organisation we would be seen as a company that takes safety and health seriously for our employees and customers alike.
2019 International Safety Award
We are extremely proud to have been recognised for this award, and it shows how far we have come since starting our formal SHE journey by obtaining our first ISO accreditations in 2006.
We have also achieved ‘The Coatings Care Overall Best Performer Award’ from the British Coatings Federation (BCF) in 2016 and were finalists 2017 and 2018, for environmental and safety performance within the coatings industry, which we are extremely honoured by.
The ISA award recognises our commitment to safety and demonstrates to our employees that their involvement has helped us to achieve this. By attaining these awards from two of the most prestigious bodies the BSC and the BCF we show our employees and customers a safe environment. The Five Star Audit was paramount to achieve them.
When and why did you decide to apply for the ISA
We had always wanted a safety award but decided to apply when the time was right to ensure we benchmarked to succeed. The guidance provided by the Five Star Audit took us over a three-year period to achieve the five-star bracket, an immense sense of achievement for us. Then, we received an invite to enter the awards and achieved an exciting Merit. We are extremely proud of it, we have shared the news and the award itself with our staff who were all involved individually and collectively to achieve it, and it is displayed on our website.
Describe your relationship with the BSC and how it has impacted your company
The BSC is an extremely resourceful organisation, the training opportunities, Safety Management magazine and the website have great information and background on other industries, including relevant case studies. The audit process, as I’ve previously mentioned, gave us valuable direction. The awards process and recognition has greatly encouraged our business to continually improve and strive to be the best. The BSC team is extremely supportive in all aspects of the process for the Five Star Audit, the International Safety Award and now for our first application for the Sword of Honour. I greatly advise businesses to become members of the BSC to acquire these resources.
What advice would you give to meet current standards
Complete a BSC Five Star Audit, because this has helped us over the past four years to go above and beyond the ISO standards, and helped us understand the need for behavioural based safety, and the positive impacts this can have on the company. This has given us an outside professional perspective on our processes and brought further consultation in the areas it was suggested we could improve on. The outcomes of the audit generated key actions within our zero harm strategy objectives, so it is a great tool to plan and deliver the foundations of your safety strategy.
It has also supported our move forward into employee wellbeing and behavioural safety initiatives, to look after our employees better.
The other advice I can give, is get your employees involved from the shop floor up – they appreciate being listened to and actively involved in the operation of the business.
Tell me about the practices and policies that made you successful at the ISA awards
To support our integrated management system, we have developed our global zero harm standards, these map each process and requirement to allow ease of completion by the management teams. The global standards explain the scope of the subject; for example, control of contractors, the specific market legislation, training requirements, responsibilities to deliver, and the associated assurance documents, etc. These key standards are the driver of our commitments and compliance to our management system processes in one clear document for each process. This also greatly improves the external audit process.
We use a SWOT analysis to reference potential risks and how changes are being evaluated and linked to operational controls such as training, communications, safe systems of work and maintenance needs. We also evaluate any legislative changes which could pose a risk, to generate our legislation registers across our core markets, we are subscribed to the Barbour online legislation system which has assisted us. Any changes to process or activity (or incident) will receive a revisit to the risk assessment to identify if changes are suitable and do not increase potential risks in other areas of the manufacturing process. The risk assessment standard includes reference to the management of change process and how changes are evaluated for risks prior to being introduced.
Wellbeing is also a contributory factor to the award, via our behavioural safety programme, our internal training modules and induction process.
Sustainability and the environment
We are accredited to ISO 14001:2015 and are very proud of our eco credentials. Our paints are water based, so kinder to the environment, and low in VOC levels, so you don’t have to breathe in nasty fumes. 100 per cent of our dry waste from our Dorset plant is recycled or converted into energy via our waste handler Suez.
We also recycle cardboard and soft plastic wrapping using our on-site Mill size balers and Perry’s Recycling collects and diverts back for processing and further reuse. 97 per cent of our liquid waste, which is generated by the manufacturing process, is also recycled via our liquid waste recycler Chloros Environmental Ltd, ensuring all is diverted via several recycling methods.
All of our equipment washings are processed in our own water treatment facility to ensure we only discharge low solid/low COD clear water. It is important to us that our contractors have our same ethos when it comes to the environment.
We have recently written an in-house training module for all our staff to complete, for awareness about the environment and the future of the planet. This includes the reduction of single-use plastics and the correct recycling at work and at home.
What are your future plans
We will continue to develop our behavioural based safety programme across our global network, as you can imagine globally this is logistically a very large undertaking specifically with language barriers. This programme will span the next few years to ensure implementation is business as usual as part of our continual improvement and commitment to our colleagues. We are also considering the BSC’s Five Star Environmental Sustainability Audit during 2020 to hopefully mirror our success with the Five Star Health and Safety Audit.
FEATURES
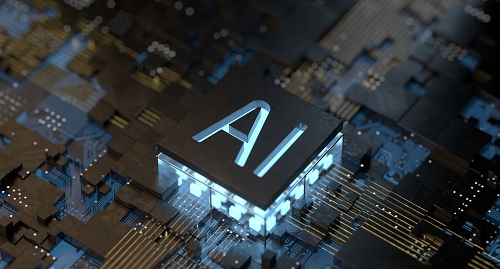
Why quality data is essential when using AI for occupational safety and health management
By Dr Bob Rajan-Sithamparanadarajah. Safety Groups UK (SGUK) on 01 April 2025
Artificial intelligence-powered models, systems and technology have the potential to significantly improve the management of occupational safety and health (OSH) risks, but it is vital that OSH practitioners understand the limitations and dangers of using AI to protect people at work.
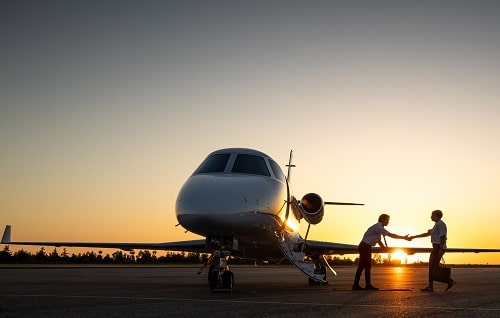
Sustainable aviation fuels: how do we put the SAFety in SAF?
By Megan Hine, Draeger Safety UK on 01 April 2025
Sustainable aviation fuel is seen as having great potential to reduce the greenhouse gas emissions from air transportation. However, as with other emerging renewable energy sources, the safety risks arising from the production, processing and storage of these biofuels can be accompanied by new risks and will require careful management from the safety industry as utilisation increases to meet the Government’s mandatory targets.
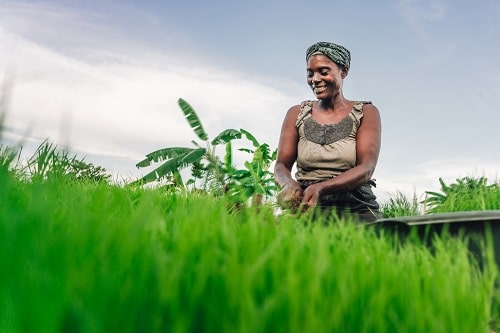
Why social sustainability should be a priority for health, safety, environmental and compliance professionals
By Agnes Chruszcz, IEMA (Institute of Environmental Management and Assessment) on 01 April 2025
By embedding social sustainability principles into their policies and operations, organisations can not only improve quality of life for their employees, workers in their supply chains and the communities they interact with, but boost their business resilience, productivity and reputation.