The problem of substandard safety products regularly made headlines during the Covid pandemic as poor quality and unusable products flooded the market, but the issue of substandard PPE and safety products existed long before Covid and remains a significant concern today.
Features
Poor quality PPE and safety products: not just a Covid problem
The Covid pandemic put substandard personal protective equipment (PPE) and safety products under the spotlight with reports suggesting hundreds of millions of pounds were wasted on poor quality and unusable PPE during the global health crisis. While these kinds of statistics grab headlines, substandard PPE and safety equipment is an issue we deal with at the British Safety Industry Federation (BSIF) day in, day out.
Unfortunately, not all safety products are created equal. For example, the law states that PPE must be correctly tested and certified to comply with the Personal Protective Equipment Regulations, but not every supplier of PPE follows the rules.
A lack of market surveillance and enforcement in the UK means it can be difficult to distinguish responsible suppliers from less responsible ones. This has led to an increase in the quantity of substandard products for sale.
Employers must ensure that they only provide fully compliant PPE for their workforce otherwise they will contravene safety legislation. A number of items are available that claim UKCA (UK Conformity Assessment) and or CE approvals but, in reality, they have not all been appropriately tested and certified. In our experience these products often do not perform as they should, putting wearers at risk and exposing businesses and individuals to prosecution for failing to protect staff.
Testing the market
Between December 2021 and December 2022, the BSIF completed tests on 127 products from non-BSIF members, which included checking their compliance with relevant standards and testing whether they perform as advertised. Only 18 (15 per cent) of these products were fully compliant. This means 108 products (85 per cent) failed to meet the regulatory criteria, many of which are still available and being sold to unsuspecting users.
Examples of products we have come across for sale recently include:
1. Hapless hood/helmet combo!
This sand-blasting hood which came with a safety helmet attached was purchased online from an SME in the UK. The helmet was not manufactured by them, but the outer cotton and leather hood with a visor was. The hood was connected to the helmet by two rivets that have been fixed to the brim and centre top of the safety helmet – this act in itself would have made the product non-compliant, as any combination of PPE has to be tested and approved as an ensemble.
The helmet was tested for impact protection according to BS EN 397:2001, which consists of a weighted ball being dropped from a height onto the helmet and the amount of force transferred from the outside of the helmet to the inside (where your head is) should not be above five Newtons. In the case of this helmet, the conducted force was 16.53 Newtons – more than three times the maximum allowable
In addition, the hood itself was not marked with any of the required information – no CE or UKCA mark to indicate it had been assessed before placing on the market; no details of who the manufacturer was; no details of what protection the hood offered; and no identifying information, such as a product name or code.
The product was also supplied without the required user instructions (the PPE Regulation obliges all manufacturers to provide detailed instructions on how to care, store, use and maintain PPE), nor a Declaration of Conformity – the manufacturer’s assurance to the market that the product has been suitably assessed and (where relevant) certified. Both of these are known as ‘Accompanying Documentation’, although it is permissible to have the Declaration available to download via a link printed on the user instructions.
2. The indestructible safety trainer that proves to be anything but
This product is advertised widely on social media channels and purports to be ‘indestructible’ – claims are made that the toecap can be run over by a vehicle and the wearer can stamp on nails without any sign of injury.
The product was provided in an unmarked box and does not carry any CE/UKCA markings, no details of the manufacturer and no information on the levels of protection offered (slip-resistant, midsole penetration resistance etc.). When tested the toecap did pass the compression testing; however, the midsole penetration resistance failed miserably, with the nail used in the test puncturing the midsole repeatedly in different locations along the midsole and at much lower than the required resistance (1,100 kN) to pass the test.
No user instructions or declaration of conformity were provided either.
3. Safety harness and lanyard that falls short of expectations
This was purchased online and supplied from China. The product arrived in a bag claiming it was ‘climbing equipment’ – something that conflicted with how it was advertised on the website, where it was clearly designated as PPE.
The markings on the product are not compliant with the PPE Regulation – no CE or UKCA marking. There were no details of which BS EN standard it conforms to and the majority of text on the product label and attached swing ticket were in Chinese.
The product did not come with the required accompanying documentation and the QR code on the swing ticket only took you to a ‘sales’ website – again primarily in Chinese. Fall protection PPE comes into the highest risk category and must have independent testing and annual quality assurance from an Approved Body. None of this had been done!
How do products from BSIF Registered Safety Suppliers compare?
The findings around non-member products are in contrast with the results of tests carried out on products supplied by BSIF Registered Safety Suppliers, who are committed to only selling certified PPE and trading honestly and ethically.
Registered Safety Suppliers’ products are tested annually as part of the scheme’s audit process and if products fail to meet the test’s strict criteria any issues must be addressed and rectified immediately for members to remain part of the scheme. Of 387 tests completed on Registered Safety Suppliers’ products between December 2021 and December 2022, 332 products (86 per cent) passed immediately and of the 55 (14 per cent) that initially didn’t meet the test criteria, all issues have now been resolved.
Buyers and end users can be assured that companies displaying the BSIF RSS shield have signed a binding declaration that the PPE and safety equipment they offer meets the correct standards, fully complies with the regulations and is UKCA and or CE-marked. This means that by using a Registered Safety Supplier a business can be confident they will receive genuine products that are fit for purpose as well as genuine information and guidance.
Benefits of specifying a Registered Safety Supplier
Verifying that your supplier is a Registered Safety Supplier gives you reassurance that the necessary checks have been performed and you know your supplier is committed to high standards.
Members of the RSS scheme must fulfil the following criteria in order to gain admittance and carry the shield: sell only certified PPE; meet all responsibilities of the PPE Regulations; submit their products for random independent performance testing; train public facing staff in the BSIF’s Safe Supply Course (a publicly recognised qualification to educate those selling PPE and safety products); maintain a quality policy; hold necessary authorisation for service provision; have the capability to carry out any necessary product recalls and trade honestly and ethically.
All Registered Safety Suppliers are audited to confirm compliance with the scheme’s requirements.
Product safety to come under the spotlight in 2023
Thankfully an increasing number of public and private sector organisations are now mandating the Registered Safety Supplier Scheme for their supply chains and we expect to see this number increase in 2023 as the focus on product safety sharpens.
2023 will see the introduction of a new post-EU Product Safety Framework which will help to strengthen the rules around the sale of products including PPE. Timings for publication of the framework are still to be confirmed, but there will be a strong focus on improving the safety and compliance of goods sold by third-party sellers on online marketplaces. We expect to see stricter responsibilities for online vendors and harsher penalties for those who fail to comply.
At the same time, the environmental, social and corporate governance (ESG) agenda is having a growing impact. Companies looking to strengthen their ESG performance are closely scrutinising the credentials of their suppliers and choosing only to work with responsible companies. When it comes to buying PPE and safety equipment, many buyers now realise that specifying the BSIF’s Registered Safety Supplier Scheme is the easiest way to ensure they are only dealing with suppliers who are compliant, competent and trustworthy.
A full list of registered suppliers is available to view at: https://www.bsif.co.uk/rsss/
Take the risk out of sourcing PPE – always specify the shield!
The BSIF is the UK’s leading trade body within the safety industry. BSIF members include manufacturers, distributors, test houses, certification bodies, safety professionals and service providers. The BSIF aims to provide support and guidance on a wide range of occupational safety issues.
Find out more at:
www.bsif.co.uk
T. (0)1442 248744
Alan Murray is CEO of the British Safety Industry Federation (BSIF).
FEATURES
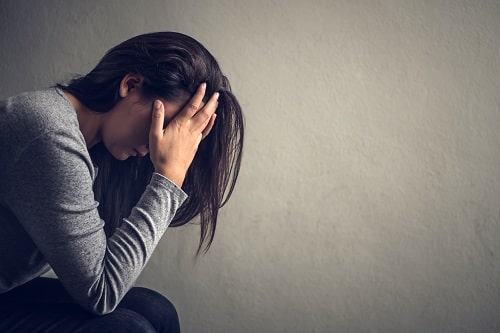
Winter pressures mean good mental health support is crucial
By Kevin Bampton, British Occupational Hygiene Society on 01 December 2021
I will tell anyone who cares to listen that winter 2020/2021 was a historic moment in British social and economic history. British business became, for the first time ever, my public health hero.
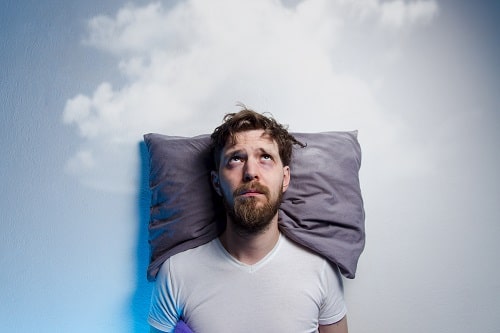
The big sleep
By Marcus Herbert, British Safety Council on 01 December 2021
Poor quality sleep can affect both our physical and psychological wellbeing, but simple lifestyle changes can make a big difference.
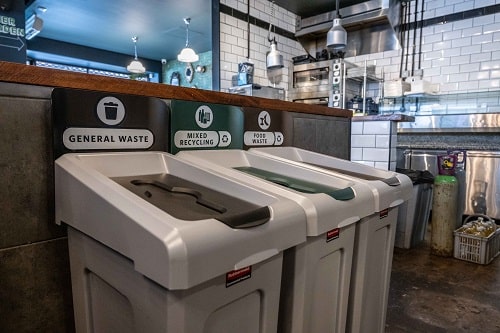
Why changes to recycling legislation in England are an opportunity, not a burden
By Adriana Olaya Rodriguez, Newell Brands on 12 November 2024
From March 2025, many businesses in England will have to begin separating their recyclable and food waste from general waste prior to collection, but the changes will bring wider business benefits, such as reduced waste disposal costs and improved sustainability credentials.