Over the past 10 years, the introduction of varying pieces of road safety legislation across the UK and Europe has left fleet managers with the unenviable task of managing numerous regulations to ensure their vehicles comply across all relevant jurisdictions. With a litany of legal points to unpick, and numerous safety devices to choose from, how does a fleet manager decipher what is most suitable in terms of functionality, quality and compliance without the worry of a device being defunct in a few years?
Features
Managing work-related road risk – a guide to current legislation and safety devices
Here, experts at global commercial vehicle safety specialist Brigade explain the various regulations and what fleet managers can do to make the most of available safety solutions.
Unravelling road safety legislation
Emily Hardy, Brigade’s UK marketing manager, is a member of the CLOCS Strategy, Standard and Governance Board and regularly involved with consultation on Transport for London’s Direct Vision Standard. Here, she explains the nuances among current legislation, such as the Direct Vision Standard and Europe’s General Safety Regulation, and how these interlink with the Fleet Operator Recognition Scheme.
What’s new with Greater London’s Direct Vision Standard?
Introduced in 2020, the Direct Vision Standard (DVS) is legislation affecting any goods vehicle weighing more than 12 tonnes operating in Greater London. Enforced by Transport for London (TfL), vehicles require a permit based on a star rating, which indicates how much a driver can see from the cab in relation to other road users.
Photograph: Brigade
HGVs that do not meet the minimum star rating must be equipped with a series of vehicle safety measures to improve and aid the driver’s indirect vision before they can qualify for a permit. Non-compliant HGVs are banned from entering Greater London and operators and drivers risk daily fines if they breach the rules.
As of October 2024, the DVS underwent some significant changes and vehicles that don’t meet the minimum rating of three stars must comply with the Progressive Safe System (PSS). This means vehicles require additional devices to be installed for indirect vision (similar to the specifications for FORS and CLOCS) to alert drivers of vulnerable road users who are in a vehicle’s blind spot. Compliance will not alter a vehicle’s star rating, but it will permit vehicles to be driven in Greater London.
For fleet operators who are unsure about a vehicle’s star rating, then they can apply to find out for free here.
What does the transition from the DVS Safe Permit to the Progressive Safe System (PSS) mean for fleet operators?
Before the updates, the permit for additional safety equipment was referred to as the ‘Safe Permit’. However, it has now transitioned to the Progressive Safe System (PSS) as part of a broader effort by Transport for London to enhance safety standards. The PSS introduces the latest advancements in technology, which means that some operators may need to replace their existing equipment with new, more advanced technology.
What are the requirements for vehicles that need to comply with DVS’s PSS?
This is a simplified version of the requirements for PSS and relates to any goods vehicle which has a rating of 0 to 3 stars.
- Predictive side sensor technology to warn the driver of a collision
- A front sensor system that provides alerts to the driver when a vulnerable road user is in the detection path, both when preparing to move off and when moving off
- A nearside camera and monitor
- An audible alarm to warn other road users that the driver is about to move.
- An A3 size DVS sticker
- Products must not interfere with safety critical aspects of the vehicle and must therefore have E Mark Certification.
The new specification also requires the Original Equipment Manufacturer to test the products with a specific test procedure.
Photograph: Brigade
However, the specification states that the tests do not need to be carried out by a third party and OEMs can self-certify their devices.
To date, Brigade is the only supplier of safety systems to have its relevant devices for the PSS independently verified, meaning fleet managers can rest assured that products meet the latest DVS requirements.
What other regulations should fleet managers be aware of?
Aside from DVS, fleet managers with vehicles operating in Europe should be aware of the General Safety Regulation (GSR). This is a set of safety standards that applies to heavy-duty vehicles operating in the EU which aims to improve road safety by mandating the use of advanced safety technologies and improving the design of the truck cab.
The regulations include:
- R151 – Blind Spot Information Systems (BSIS)
- R158 – Reversing Information Systems (REIS)
- R159 – Moving off Information Systems (MOIS).
Each of the above covers requirements for safety systems that must have a particular range of specifications to comply. More information about this can be found here.
My fleet is FORS accredited – do I comply with DVS?
This depends on which level of FORS you have been awarded. For those with vehicles that are FORS Silver or Gold accredited, vehicles must still apply for a DVS permit, and, if needed, implement the PSS to be compliant with the DVS.
As of 2 January 2025, new requirements for FORS (Version 7) will apply to all organisations with audits on or after this date.
The amendments cover everything from documentation and regulatory licensing to driving standards and, of course, vehicle safety equipment.
What are the FORS V7 changes for vehicle safety equipment?
There have been rewording and additions to the vehicle safety equipment requirements that encourage evolving best-practice, with limited additional requirements.
Most notable is the emphasis on reducing false alerts for articulated vehicles. The update reads: “For articulated vehicles, sensors shall be suitably positioned on the tractor unit to provide sufficient coverage but preventing activation solely on articulation of the trailer.”
Operators with vehicles that comply with the Direct Vision Standard and are either rated three stars or above, or have fitted the equivalent Progressive Safe System to their vehicles, are considered to meet S6 blind spot vision aids requirements.
However, for those that don’t operate as part of the London HGV Permit Scheme, how can operators ensure their vehicles meet the latest V7 requirements?
Introducing Radar Predict and its trailer discovery mode
Radar Predict is an award-winning advanced collision prediction system specifically designed to protect cyclists from collisions with HGVs and is the ideal solution for the latest FORS and DVS updates.
Perfect for articulated vehicles, Radar Predict incorporates a trailer discovery mode to eliminate false alerts when the vehicle is turning. This cutting-edge technology aids drivers by presenting visual cues via warning LEDs and audible alerts, guaranteeing prompt intervention and the protection of road users from possible collisions.
Using AI technology, the single dual-radar analyses data such as the speed and direction of both the vehicle and the cyclist. By differentiating between static and moving objects, the Radar Predict algorithm alerts the driver only when an impact with a cyclist is likely and aids the driver to keep focused without being overloaded by alarms while driving in busy urban areas.
Radar Predict complies with DVS PSS, FORS V7 and GSR’s R151 for blind spot information systems.
There so many different regulations. How do I know which safety devices to invest in?
The good news is that you don’t need to have numerous devices for each piece of legislation. However, just because you have one device fitted, say to comply with the GSR’s R159 for Moving Off Information Systems (MOIS), this doesn’t mean you automatically comply with other regulations, such as the PSS for DVS in Greater London. This is because there are nuances between the legislations, such as how devices should work and the distances of detection zones in relation to vulnerable road users and their vicinity to the vehicle. In short, although a device might be suitable as a system for one regulation, it might not be compliant for two different legislations requiring a similar device.
In this instance, the best thing to do is to speak to a specialist, such as Brigade, to discuss the best solutions for your fleet and how and where your fleet operates.
What should I look for when choosing safety devices for my fleet?
Any product you choose to enhance the safety of your fleet should have undergone thorough testing and, even better, if they offer a lifetime warranty then you can be assured of complete reliability.
For example, at Brigade we will never release a product until we are 100 per cent confident it’s fit for purpose.
Photograph: Brigade
It’s important not to settle for low quality vehicle safety solutions. Investigate the credibility of the safety devices you’re investing in and how they compare to their counterparts. The more time that’s been spent on developing and testing the product and including extra functionality, the less likely it is going to need replacing or upgrading too soon, and the more likely it is that your fleet safety isn’t compromised.
The future of fleet management – minimising the burden for managers
James Tyrell is the fleet services technical support engineer at Brigade. He explains how telematics and video integration is helping to improve safety for fleets across the UK and minimising the burden for fleet managers.
How does telematics for fleet management work?
Telematics enables vehicle tracking so a vehicle’s location and movements can be monitored. The system delivers important information to fleet managers and supervisors, who are given an overview on a vehicle’s designated route and can analyse how it’s being driven, helping to contribute to safe driving behaviour.
The system can collect data on various aspects of driver performance, such as speeding, sudden braking and rapid acceleration. By analysing this data, companies can build up a picture of risky driving patterns or pinpoint the actions of a specific driver. This enables fleet managers to decide whether driver safety training is necessary, or whether a persistent offender should be put on an internal driver safety programme. Telematics can therefore help to prevent potential incidents by identifying risks before incidents occur.
Such systems can also issue warnings if, for example, the speed limit is exceeded by more than 10 per cent. Fleet managers will be able to see at a glance how many speed limit violations have occurred in a day, week or month. If a driver is stationary with the engine running, fleet managers will get a notification and be able to spot and subsequently reduce lengthy periods of idling, which has obvious environmental benefits as well as helping to reduce costs.
Geofencing capabilities are another important aspect of telematics. A virtual geographic boundary, defined by GPS, will enable software to trigger a response when a device enters or leaves an area. Fleet managers can set their own geofences according to their areas of work. For example, if a company has 15 different depots across the country and the manager wants to know where a specific vehicle is located, then they can click on the vehicle and the system will tell them where it is and match it to a particular depot, region, or even a country if the vehicle is operating internationally.
Systems like Brigade Telematics can be fully managed via Cloud connectivity that links to the vehicle through a mobile digital recording system and CCTV. The benefit of Cloud-based services is that fleet operators who are working from home or unable to be in the office, can still access data remotely rather than having to physically enter the vehicle to retrieve information.
The system is also intuitive, meaning if an incident does occur, the Google Maps function, which provides dates and times, can be clicked on and the precise snapshot of footage relating to the incident can be located and downloaded instantly.
The most recent advances in telematics have enabled Brigade to integrate its systems with Webfleet – Bridgestone’s globally trusted fleet management solution. This enables fleet managers to combine telematics and video safety solutions to increase efficiency and streamline their operations.
Vehicle safety solutions are evolving and increasingly moving towards understanding why incidents happen and not just that they have happened. The UK Department for Transport estimates that human error is responsible for 88 per cent of road collisions, making the focus on reducing it through advanced technologies in commercial vehicles a logical step. As we look to the future, the objective is to minimise human error on the roads through technological advancements.
Telematics can, for example, understand whether a driver was distracted, and this can paint a very different picture, or it may point to bad driving practices. This has also been regulated in Europe, requiring new vehicles to be equipped with such systems. The installation of Driver Drowsiness and Attention Warning (DDAW) systems and Advanced Driver Distraction Warning (ADDW) systems are obligatory in new vehicles from this year, with certain extensions for smaller manufacturers.
As safety moves towards the future, one thing is certain – the burden for fleet managers to prove how incidents occurred and provide irrefutable evidence in the event the driver is not at fault is becoming easier to oversee.
For further information or advice about managing a fleet’s safety devices, contact Brigade:
T: +44 (0)1322 420300
FEATURES
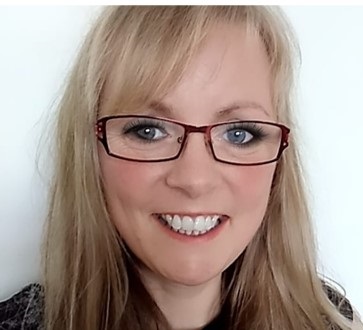
From crisis to prevention: the urgent role of employers in upstreaming health
By Dr Julie Riggs, British Safety Council on 16 June 2025
Poor public health and long-term sickness absence are placing extreme financial pressure on the UK’s health and social care system and the overall economy. However, by investing in workplace health prevention programmes and education initiatives, employers can help reduce the scale of ill health among the population and minimise the associated costs for society and business alike.
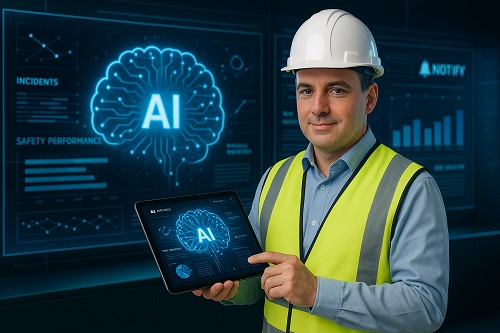
The AI safety revolution: augmentation, not elimination
By Alex Nichol, Notify Technology on 16 June 2025
Artificial Intelligence looks set to vastly reduce the amount of time and effort required to record, create and analyse occupational safety and ESG data, procedures and performance, while automatically providing insight into areas for improvement and areas of excellence.
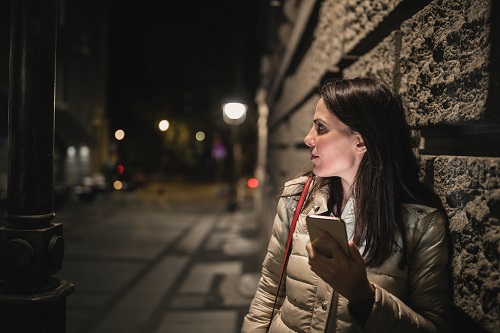
Protecting lone workers: a structured approach is critical
By Naz Dossa, Peoplesafe on 06 June 2025
Whether dealing with the public in their homes or working in remote locations, lone workers face a variety of risks to their health, safety and wellbeing. It’s therefore vital that employers systematically identify and assess the specific hazards lone workers face and then implement suitable measures to mitigate them.