Engineering solutions for noise control on plant, machinery and tools are often straightforward, low-cost and bring financial savings themselves, so it’s time employers moved away from the default position of purchasing and issuing personal hearing protection to workers.
Opinion
Beyond compliance: why noise control must evolve beyond PPE
Gill Cussons: "We must move beyond compliance and into effective, practical solutions."
1. The PPE illusion vs the evolution of noise control
Over the past decade, personal protective equipment (PPE) technology has surged ahead, with hearing protection now offering built-in communications, alerts, noise monitoring, and even the ability to adjust the attenuation to suit the environment (Active Hearing Protection). These innovations are fantastic; and I use and recommend them myself.
But here’s my question:
If we’re embracing these PPE advancements, why aren’t we embracing the incredible advancements in noise control solutions too?
Why do I open safety magazines and see page after page of hearing protection and sound measurement devices, but almost nothing about noise reduction technologies? If we truly care about reducing noise-induced hearing loss (NIHL), shouldn’t noise control get as much attention as PPE?
The issue isn’t a lack of innovation – the technology is there. But there seems to be an unspoken fear of ‘getting it wrong’ when it comes to noise control, leaving safety teams reluctant to push for engineering solutions.
This is an example screenshot of the spreadsheet I use to show clients how much they spend on hearing protection and how much waste is accumulated each year compared to noise controls. Credit: Noise & Vibration Solutions (NVS)
2. The fear of noise control: why companies default to PPE
Through my work, I’ve seen time and time again how companies struggle to act on noise reduction – even when the solutions are straightforward, low-cost, and, in some instances, can even save money.
Take air leaks, for example. I once identified that the main noise source in a facility wasn’t the machines, but compressed air leaks. Fixing them wouldn’t just be a win for employees’ hearing – it would also reduce energy costs. Yet instead of jumping on this opportunity, the company hesitated because the fix had to come out of the safety budget rather than the engineering budget.
Another case? Missing silencers on pneumatic systems. A simple replacement could drastically lower noise without affecting performance. Again, pushed back because it wasn’t a compliance issue.
There’s a disconnect between safety and engineering that results in missed opportunities. Too often, companies default to PPE because:
• It’s simple to implement – just buy and distribute
• It’s visible – regulators and inspectors can see compliance instantly
• There’s a fear of getting noise control wrong – even though many companies also get PPE implementation wrong!
Ironically, I’ve been in businesses where they spend over £85k a year on disposable earplugs alone but won’t invest £35k on noise reduction modifications that could eliminate the problem.
3. ALARP in action: what real noise reduction looks like
We hear the phrase “as low as reasonably practicable” (ALARP) all the time – but what does that actually mean in real terms?
A reasonably practicable approach to noise reduction would include:
• Fixing compressed air leaks instead of masking the noise with hearing protection
• Using quieter cutting blades – like the Leitz WhisperCut and Norton Clipper Pro Silencio, which reduce cutting noise by up to 9dB(A) without affecting performance
• Using modern pneumatic silencers, which cut exhaust noise by 30dB(A) or more while improving efficiency
• Replacing open-ended air guns with low-noise alternatives, significantly reducing impact noise
• Swapping grinding wheels for flap sanding discs, cutting both noise and vibration
• Installing Helmholtz resonator silencers on ventilation and exhaust systems, reducing noise without restricting airflow
• Regularly maintaining equipment to prevent noise levels from creeping up over time.
Photograph: iStock
One of the most overlooked ways to reduce noise is simply maintaining existing equipment. Machines don’t get noisy overnight – it happens gradually, and because workers are used to it (or wearing hearing protection), they don’t always notice how loud things have become. A common example is worn bearings and unbalanced fans. Regular maintenance, such as tightening bolts, replacing worn parts, and lubricating bearings, can bring noise levels back down without expensive modifications.
4. Hearing protection is here to stay – but let’s use it properly
No matter how much we reduce noise, there will always be a need for hearing protection (HP). That’s fine, but only if we get it right.
HSE’s five-year focus on noise in the workplace has already identified shocking failures in workplace inspections:
• 77 per cent of workers had never been shown how to store hearing protection properly
• 82 per cent didn’t know how to check for damage
• 74 per cent didn’t know they should report damaged PPE
• 63 per cent had no training on why hearing protection matters
• 95 per cent of staff were never assessed for audibility when issued with hearing protection.
Overprotection is a growing problem. If workers can’t hear alarms, colleagues or moving vehicles, their risk of fatal accidents increases. Yet ironically, when we look for hearing protection with lower attenuation (to allow safe hearing), we find we have to pay more for ‘less protection’.
The misconception that ‘loosely fitting earplugs let in some sound but still protect’ is widespread. However, earplugs and ear defenders rely on a proper seal, without it workers are left unprotected while thinking they’re safe.
I use an earplug fit-testing tool from Hear 4 The Long Term when I deliver toolbox talks, which provides a Personal Attenuation Rating (PAR) against the SNR of the worker’s ear plugs, for each ear. Time and time again, untrained workers assume their earplugs are working – but the test results prove otherwise.
Once they see the numbers themselves, their attitude changes. Employees tell me that, for the first time, they understand what properly fitted earplugs should feel and sound like.
If we’re relying on HP until noise controls are in place, at the very least, we should do it properly.
5. What about the equipment manufacturers?
We know duty holders must reduce noise “as far as reasonably practicable”. As part of this, HSE inspectors now ask companies about their purchasing policy – expecting them to consider buying quieter equipment as a mid to long-term strategy for reducing noise exposure.
But what about the manufacturers? Why aren’t they held to the same standard?
The requirement for equipment manufacturers to reduce noise and vibration “as far as reasonably practicable” is set out in multiple UK and EU regulations, including:
Supply of Machinery (Safety) Regulations 2008 (UK) – the UK’s implementation of the EU Machinery Directive 2006/42/EC, which legally requires manufacturers to design machinery that reduces noise and vibration risks at the source.
What this means for manufacturers:
• Noise and vibration must be engineered out where possible
• Where not possible, manufacturers must justify why they can’t reduce it further
• Noise levels must be measured, documented and disclosed in the technical file.
Failure to comply means equipment cannot be CE/UKCA marked and cannot be legally placed on the market.
So why aren’t machinery manufacturers held accountable in the same way that duty holders are?
Noise emission data is often inaccurate or missing
Even when businesses ask for quieter equipment, they’re often just offered a ‘quieter’ model – which usually means an off-the-shelf enclosure rather than an actual redesign.
Why is noise not fully integrated into the design process? If cars must be designed to be cleaner, why aren’t machines required to be quieter?
We need industry-wide accountability – if the British Safety Industry Federation (BSIF) can take a stand on PPE that isn’t fit for purpose (where 90 per cent of non-member hearing protection failed suitability tests), why can’t we do the same for machinery noise?
6. Rethinking noise management: a cultural shift is needed
So, where do we go from here?
We need to change the industry mindset by asking:
• Why are we obsessed with PPE when noise control is the first line of defence?
• What’s stopping us from investing in noise control when it’s often more cost-effective?
• Would businesses think differently if they saw the financial cost of relying on PPE?
• Are we too focused on compliance instead of effectiveness?
Noise control doesn’t have to be expensive or complicated. Some of my favourite fixes involve simply adjusting something, fitting a switch or making a small modification – zero cost, no impact on production, huge impact on workers’ health. We must move beyond compliance and into effective, practical solutions. If we don’t, NIHL will remain a leading occupational disease for another 50 years.
Gill Cussons is a noise and vibration consultant. She is owner at Noise & Vibration Solutions and co-founder of Hear 4 The Long Term Ltd. She is a supporter and member of the UK Hearing Conservation Association.
Contact her at:
uk-nvs.com
[email protected]
linkedin.com/in/gillcussons
T. 07837 385 248
hear4thelongterm.co.uk/
For more information on the UKHCA see:
hearingconservation.org.uk
OPINION
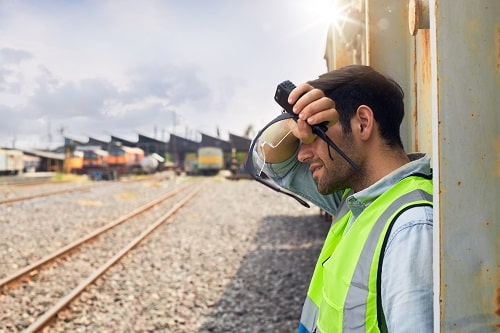
Heat at work: a silent killer
By Halshka Graczyk and Lacye Groening, ILO on 07 April 2025
Workers across the world are increasingly being exposed to excessive heat with serious implications for their safety and health. It is therefore vital that governments, employers and workers’ organisations develop, share and implement practical and low-cost strategies and measures for effectively reducing the risk from heat stress at work.
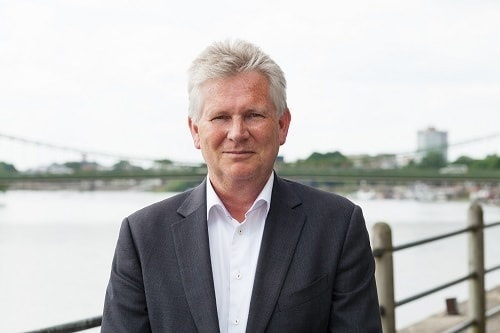
Making good work the foundation
By Mike Robinson FCA, British Safety Council on 07 April 2025
In 2024, for the first time, the UK dropped out of the list of the top 20 happiest countries: according to the World Happiness Index. This year, the UK rests in 23rd place, slightly ahead of the US and behind the Nordic countries, Germany, the UAE and others.
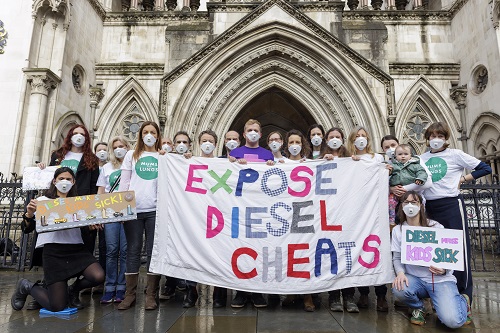
The air we share: why tackling pollution protects us all
By Scott Paul, Mums for Lungs on 04 April 2025
Air pollution is often invisible; its impact is anything but. Whether you’re a parent worried about your child’s lungs, a construction worker breathing exhaust fumes, or a commuter passing through busy streets, polluted air is everyone’s problem.