The Health and Safety Executive is currently conducting an inspection programme looking at the adequacy of employers’ noise control measures, while changes to how compensation claims for noise-induced hearing loss are assessed are predicted to result in higher payouts for affected workers. As a result, it is crucial employers review their noise risk reduction approach to ensure it reflects current best practice.
Features
HSE inspections target hearing protection and noise control failures
HSE noise inspections – the common failings
The following are some of the common issues identified over the first three months of HSE inspections, which triggered a 300 per cent increase in noise-related enforcement actions issued to duty holders by HSE.
• Duty holders were often unaware that personal protective equipment (PPE) in the form of hearing protection equipment (HPE) is a difficult option due to poor advice from consultants and others, and due to the duty holders’ lack of knowledge of this area
• Just five per cent of sites were testing that warning sounds are audible to wearers of hearing PPE (i.e. the PPE was providing over-protection)
• Serious and common errors were found in noise reports, including those from the external noise consultants used by 41 per cent of sites visited
• None, very limited or very poor advice on noise control found in duty holders’ noise reports, including those produced by external noise consultants.
Substantial changes are taking place to the legal landscape surrounding the risks to health caused by exposure to noise at work. Photograph: iStock
HSE inspections – the next phase
HSE is collecting noise assessment reports and will be comparing them against its recently issued Noise Risk Assessment – consultant and reporting quality checklist. (This checklist has not yet been published on HSE’s website but a copy can be downloaded via the link on INVC’s website.) The plan is to encourage an improvement in the quality of noise reports and advice, both produced in-house by duty holders themselves and by noise consultants. HSE also plans to take enforcement action against ‘rogue’ noise consultants.
INVC has reviewed countless noise assessment reports submitted by duty holders attending our IOSH-approved training courses designed to ensure competency in noise at work risk assessment and management. As a result, our advice on the reporting and advice element of noise control is: “Why spend money and resources on placebo risk assessment reports that tell you what you already know – that you still have a problem? Spend the resources on risk reduction instead...”
This is fundamentally an issue of a lack of knowledge among duty holders, and/or a failure to obtain suitable advice, about what constitutes best practice in noise risk reduction in the particular circumstances, whether in-house or via a consultant.
Apart from the expected substantial increase in noise-related enforcement activities by HSE, a key feature of the regulator’s noise inspection focus is a desire to move organisations away from the standard and very commonplace ‘risk assessment report checkbox mentality’ towards drawing up action plans to determine and implement effective risk controls to reduce noise exposure at work.
£700k-plus compensation settlement – the legal landscape for noise damage has changed
Substantial changes are taking place to the legal landscape surrounding the risks to health caused by exposure to noise at work. In the near future, these changes are predicted to lead to a tidal wave of litigation that will result in a massive increase in the costs of claims for work-related noise-induced hearing loss (NIHL), with a knock-on effect on employers’ insurance premiums.
Some little-known salient facts regarding the effects of NIHL include:
1. The damage caused by noise is avoidable using the latest revised best practices
2. The damage is not just to hearing, but to health. This includes the recently discovered huge increase in the risks of dementia and Parkinson’s
3. Higher risks of unemployment, early retirement and the likelihood of accidents.
Previous legal guidelines (Coles, Lutman and Buffin, CLB, 2000) for assessing whether an employer should be held liable for an employee’s NIHL were based on the results of Pure Tone Audiometry (PTA) and any noise exposure below 85dB(A) was discounted.
However, new guidelines (MLC 2022) for assessing whether an employee should be awarded damages from their employer for their NIHL are likely to herald a dramatic change as they take into account the nerve damage not assessed by PTA with no lower limit on noise exposure. The latter opens up the possibility of compensation claims for exposures to noise at work as low as 75dB(A).
A key feature of HSE's noise inspection focus is to move organisations away from the commonplace ‘checkbox mentality’ towards drawing up action plans. Photograph: iStock
In addition, the health effects of NIHL have been seriously underestimated. Recent research has shown that NIHL can:
• Increase the risk of dementia by up to five times with up to a 57 per cent increased risk of Parkinson’s
• Cause much higher risks of unemployment, early retirement and the likelihood of accidents.
Consequently, settlement costs for NIHL from affected workers are expected to balloon, as will the costs of insurance for high-risk working environments.
In a recent (2023) court case where a worker was seeking damages for work-related NIHL, Barry v Ministry of Defence, the judge awarded the claimant a settlement of £713,716 by taking into account not just PTA results, but synapse damage, earnings (past and future), general damages (suffering past and future) and other costs. This case is therefore the ‘canary in the NIHL costs mine’.
The urgent proactive actions required to mitigate risk and costs
In light of both HSE expectations linked to the ongoing huge increase in enforcement actions and the new legal landscape, duty holders operating work sites and tasks that pose a risk of NIHL to workers, must take swift proactive actions to update their current risk reduction programmes to the latest revised best practices.
On the plus side, most of these changes can be implemented to reduce noise-related risks by up to 90 per cent with little or no cost increase over current expenditure.
The following is a summary of the actions duty holders should take to determine what constitutes current noise risk reduction best practices and how they can be implemented. A one-day online workshop is also available that provides details of HSE’s expectations, the current legal framework on noise control and changes to best practice in noise control at work, with examples.
1. Hearing protectors
Don’t assume PPE provides sufficient protection; it very often doesn’t. Duty holders need to be able to prove how much protection is being achieved. Guaranteeing adequate protection much above 90dB(A) is difficult.
2. Noise assessments and reports
Develop or acquire a high-quality report template for all future reports, whether in-house or via consultants. Do not keep repeating placebo assessments. You must create and implement an Action Plan based on the revised best practices that include noise control.
3. Noise control cost/benefit analysis
Invest in a Noise Control Audit that provides a cost/benefit analysis of the options to reduce noise levels through modern engineering control measures. This is a regulatory requirement. Modern noise control programmes can quite often be self-financing.
4. Audiometry
Traditional pure tone audiometry cannot pick up the early signs of hearing damage. It is a very lagging indicator that is of little use in risk management. Duty holders should ask their occupational health provider to switch to otoacoustic emission (OAE) hearing tests instead. OAE provides a rapid, objective evaluation of the early signs of hearing damage, the results of which can be used to update risk management programmes.
For a comprehensive list of online resources on noise control at work from a variety of organisations, see: invc.com/resources/technical-notes-occupational-noise/nihl-risk-management-online-resources/
For more information see: invc.com
[email protected]
T. +44 (0)1753 698 800
Peter Wilson is Technical director at Industrial Noise and Vibration Centre (INVC)
FEATURES
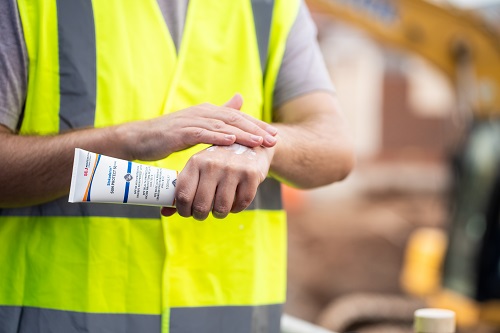
Facing the facts: protecting your outdoor workforce from UV exposure and skin cancer
By SC Johnson Professional on 11 July 2025
With outdoor workers at significant risk of skin damage, ageing and cancer due to exposure to the sun’s UV rays, it’s essential that employers in sectors like construction and agriculture create a working environment where sun safety precautions become the norm, rather than the exception.
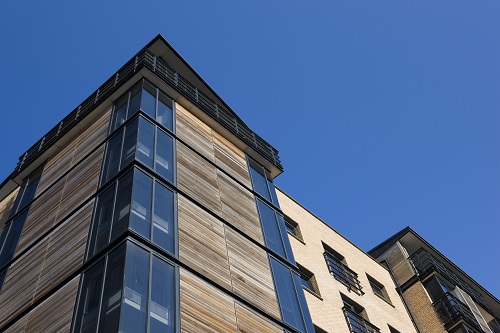
2025 UK fire safety regulation updates: a quick guide
By Chloe Miller on 11 July 2025
The regulatory landscape covering fire safety arrangements and structural features in domestic and commercial buildings has undergone a number of significant changes in recent years, making it essential for responsible persons to review their approach to keeping residents, workers and the nearby public safe from the risk of fire.
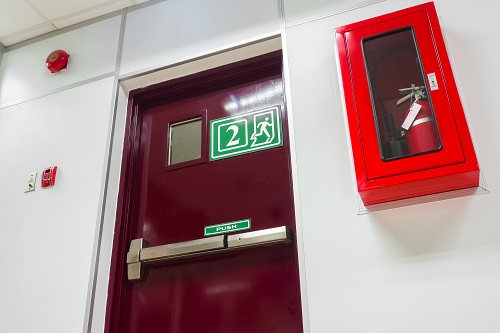
Tackling new fire risks as Fire Door Safety Week celebrates 12th year
By Helen Hewitt, British Woodworking Federation on 11 July 2025
The British Woodworking Federation’s annual Fire Door Safety Week this September will encourage duty holders such as those in charge of residential buildings to consider the dangers from lithium-ion batteries and ensure fire doors remain fit for purpose in reducing the risk should a battery-related fire break out.