Advances in hearing protection technology are making it easier to warn workers in real-time to protect themselves from hearing damage – and spot those who could be at greatest risk.
Features
Cutting through the noise
Noise-induced hearing loss (NIHL) is a global health problem. According to the World Health Organization (WHO), an estimated 1.3 billion people worldwide suffer from hearing loss due to noise exposure through work or leisure activities.
Occupational noise exposure is responsible for 16 per cent of all cases of disabling hearing loss in adults. In the UK, the Health and Safety Executive reported 14,000 new cases of work-related hearing loss in 2021 – and this is likely to be a conservative estimate.
Workers employed in the construction, manufacturing, mining, agriculture, utilities and transportation industries, as well as military personnel and musicians, have the highest risk of occupational NIHL. Although hearing loss is serious and debilitating, most people simply don’t realise they have damaged their hearing until it is too late – and the effects are irreversible.
What is the problem?
The root problem is that noise exposure is highly variable and can be difficult to predict. Transient peaks – such as walking past a noisy machine or a large vehicle passing by – may not even register as a risk. And even where the risk is recognised, exposure limits may have been exceeded before the employee is informed or has time to respond.
Clever personal monitoring systems can be configured to present critical data. Photograph: Minuendo
Another major factor is that the actual attenuation provided by hearing protectors in real-world settings varies significantly between individuals. Results in the field don’t always correlate well with the noise reduction performance suggested by the manufacturer. This can make spotting areas for improvement problematic.
These variances can be further exacerbated because traditional earmuffs and earplugs are not always correctly deployed: workers commonly find them uncomfortable or restrictive to wear, particularly when attempting to communicate with colleagues. In industrial and construction settings, this can present a safety risk in itself: particularly where mobile, heavy machinery such as forklifts, lorries, passing trains, drilling rigs and dumper trucks is present.
For employers, this is a real headache. Traditional hearing protection cannot help them to understand what level of protection is being achieved over time. Nor can passive devices support employers in understanding whether their hearing protection measures are effective and legally robust.
For the health and safety manager, lack of reliable data and insight is compounded because hearing loss prevention is just one of their many responsibilities. Other significant daily tasks include compiling safety reports, investigating and reporting on safety incidents, devising corrective actions and updating processes and procedures.
In a health and safety setting, it is easy to see how wireless connectivity could be deployed to support noise monitoring regimes. Photograph: Minuendo
The role also demands close attention to health and safety legislation to ensure compliance with many wide-ranging regulations. In other words, the safety manager often simply does not have the resources to work at an individual employee level – particularly where the workforce is highly mobile or widely dispersed.
So, for some businesses, the current situation on NIHL in the workplace is this: safety managers are time-poor and drowning in data; employers have no accurate record of an individual’s noise exposure over time; and employees are not being empowered to take responsibility for their own wellbeing. Clearly, a more effective way to tackle NIHL in the workplace is needed.
Optimum solution
Any effective new solution must avoid information overload and provide safety managers with meaningful and actionable insights so their limited time and resource can be properly targeted. Also, any physical equipment needs to be comfortable and intuitive to ensure that it is worn correctly by end-users to provide the highest levels of hearing protection.
Ideally, the new solution should also reinforce good practice and involve employees proactively and personally in taking action to prevent damage to their hearing while at work. For the employer, an accurate record of each individual’s noise exposure would be a major improvement – particularly in demonstrating compliance.
It’s a tall order, but the good news is that the technology now exists to answer all these requirements. Using a combination of technology transfer and the enormous potential of digitalisation, it is possible for employers to make a major step-change in how they tackle NIHL in the workplace.
For example, the physical discomfort or inconvenience experienced by wearers of traditional earmuffs and earplugs can be remedied by adopting design advances from the professional music sector. Lossless earplugs are now commonly available that use foam and silicon materials to achieve a universal fit. These earplugs are extremely small and lightweight, offering excellent noise attenuation properties without compromising the wearer’s situational awareness.
Meanwhile, the evolution of intelligent digital technologies is enabling more effective data collection, analysis and interpretation in almost every aspect of our lives. Ubiquitous connectivity makes it possible to collate and transmit massive amounts of data reliably from many locations at once – often in real time. In a health and safety setting, it is easy to see how wireless connectivity could be deployed to support noise monitoring regimes and alert safety managers and workers at the point action is required.
Less noise, more insight
New protective equipment that combines the latest aural comfort with the data collection, storage and analysis capabilities that modern working environments demand is now available.
For the first time, employees can take responsibility in real time. Active noise monitoring means that when an immediate risk is detected, an individual alarm will alert the employee to take action. This may mean moving further from the noise source, using the ergonomically designed earplugs, or adding more hearing protection.
Data from each shift can be uploaded in the cloud and used to generate further guidance. For example, employees can receive automated notifications about their daily noise exposure levels in the form of emails or text messages. These messages can also provide straightforward suggestions that they can adopt to lower their risk of NIHL.
Cloud-based storage and analysis can also provide the insight and targeted approach that safety managers need to be more effective. These intelligent personal monitoring systems can be configured to present critical data in a simple dashboard format. This access to contextual data cuts through the noise and helps to prevent information overload. It allows the safety manager to pinpoint the individuals who are most at risk of NIHL, enabling them to work with them collaboratively – not coercively – to drive improved behaviours.
Nor are these new hearing loss prevention solutions limited to recording noise exposure levels. The intelligent technology can also provide other valuable usage data, such as when and how well the earplugs have been fitted. Cloud storage also allows historical noise exposure data to be stored over time. This data pool provides a vital audit trail of compliance should it be required.
Conclusion
Current occupational hearing loss prevention processes are often inadequate and not fully effective. They rely on passive and outdated equipment that does little to support safety managers, employers and employees in tacking the problem.
In the 21st century, it is simply unacceptable that anyone should suffer the consequences of workplace-induced hearing loss. The condition is entirely preventable – and we now have the technological tools to achieve real and permanent behavioural change.
This article is based on the white paper Cutting Through The Noise, which is free to download at: minuendo.com/cutting-through-the-noise
Neal Muggleton is Chief operating officer (COO) at System Science at Minuendo
FEATURES
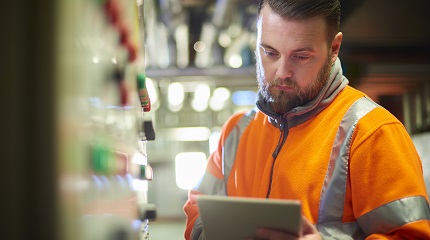
The compelling case for mandatory UKAS accreditation in asbestos surveying
By Robert Southall, Asbestos Testing and Consultancy Association (ATaC) on 02 September 2025
With recent HSE research concluding that asbestos site surveys from UKAS-accredited companies and surveyors consistently deliver higher quality results than their non-accredited counterparts, the time has arrived for the Government and HSE to introduce mandatory UKAS accreditation for all organisations providing asbestos surveying services.
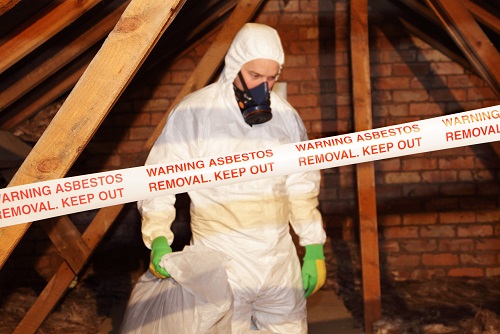
Why it’s time for a new national asbestos strategy
By Campaign team, Asbestos Information CIC on 01 September 2025
A group of asbestos management organisations have developed a methodology that can more accurately identify the location and condition of asbestos-containing materials (ACMs). It presents the information in simple form so building owners have a better understanding of the risk the ACMs pose. The move would also allow asbestos removal strategies to be targeted at buildings with the riskiest ACMs and the most vulnerable occupants.
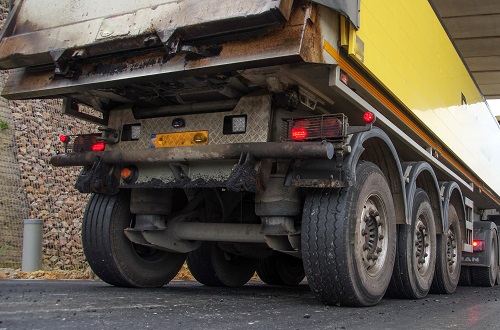
For better or reverse
By Belinda Liversedge on 01 September 2025
This July, HSE prosecuted two cases in which two workers were killed by reversing HGVs. They shared striking similarities.