Personal noise dosimeters and sound level meters can provide a picture of noise exposure and sources within a workplace.
Features
Measure Up
The images associated with a ‘workplace injury’ are dramatic and visual – falls from height, machinery crush injuries, chemical burns; all such serious injuries warrant due care and precautions from employers and workers. However, an equally serious and pervasive type of workplace injury is a much less visual one. In fact, it cannot be seen at all.
Noise-induced hearing loss (NIHL) is a permanent condition resulting in life-changing injuries that can seriously impair a worker’s quality of life. World Health Organization figures indicate that noise exposure contributes to 22 per cent of workplace-related health issues (bit.ly/35RsJQy).
Personal noise dosimeters and sound level meters can provide a picture of noise exposure and sources within a workplace
In the UK alone, HSE statistics suggest that more than one million employees are exposed to levels of noise at work which puts them at risk of NIHL (bit.ly/2XObtae). In 2018/2019, it was estimated that 21,000 workers suffered from work-related hearing problems, including hearing loss.
NIHL can lead to long-term consequences that can affect life both inside and outside of the workplace. Sufferers face social isolation and increased anxiety due to impaired communication and are put at greater risk in the workplace due to a decreased ability to monitor the workplace environment for audio cues warning of a potential hazard, such as alarms or machine noise.
Also, as the conversation around health and safety has turned to encompassing mental health and wellness, the impact of hearing loss on mental health cannot be understated. In fact, research has shown that a person with mild hearing loss is three times as likely to experience depression, and someone with more severe hearing loss is five times more likely.
It must be remembered that NIHL is preventable. The figures serve to reinforce that, despite increases in health and safety culture and committed legislation around workplace noise – namely the Control of Noise at Work Regulations 2005 – it is vital that employers and employees alike understand and commit to the need for an effective programme of noise monitoring and control measures. This relies on two key elements – training and tools.
Training
Whether conducted in-person or in a digital format, courses that provide a firm grounding in the mechanics and methodology of noise exposure and monitoring are the foundation of any comprehensive workplace programme.
SLMs provide highly accurate static spot-readings of noise sources and individuals
From covering the basic biology of how the ear reacts to and can be damaged by sound, courses should also cover topics including the parameters and terminology of noise and monitoring and legislation surrounding noise at work. Instruction on the practical use of instrumentation – such as noise personal dosimeters and sound level meters (SLMs) – should be a core component of training, alongside how they are calibrated, and how to calculate and interpret the results accurately.
Tools
To provide a comprehensive picture of noise exposure and sources within a workplace, two main tools are used – noise dosimeters and SLMs. Dosimeters are body-worn monitoring devices that are used to give readings of workers’ noise exposure as they undertake their daily tasks. SLMs provide highly accurate static spot-readings of noise sources and individuals.
SLMs are hand-held devices, enabling measurements to be taken at ear level with the instrument pointing at the noise source. If workers are likely to be exposed to high levels of impulsive noise, emitted from heavy pressing operations or sheet metal working, peak noises must be measured for accurate results and compared to peak action levels. Data captured by SLMs can also be used to demark noise control areas and select appropriate hearing protection and attenuation.
Highly mobile workers can employ a small body-mounted noise dosimeter to collect individual exposure data. Employees wear dosimeters for a full shift and data is logged instantly. When downloaded onto another device, details of the time history of the noise exposure can be reviewed, highlighting where and when high exposures occur throughout the day.
Advances, including Bluetooth connectivity and partner software or apps, allow safety managers to record, download and interpret data from units remotely, without needing to interrupt workers during their duties. This has become especially vital as a result of mandatory social distancing measures instigated across many workplaces as a result of the Covid-19 pandemic. This technology allows safety managers and employees to monitor their exposure to noise hazards and safeguard auditory health while remaining compliant and reducing the possibility of virus transmission.
Two key things to take away: ‘knowledge is power’ and ‘have the right tool for the job’. These are not the end of the story, of course. Though you may know the exposure of an individual, it then becomes about how it is used to provide the right controls, ensuring that NIHL does not occur in the workplace.
Tim Turney is Technical Product Manager at Casella
FEATURES
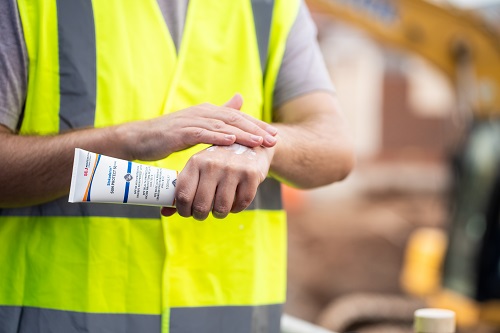
Facing the facts: protecting your outdoor workforce from UV exposure and skin cancer
By SC Johnson Professional on 11 July 2025
With outdoor workers at significant risk of skin damage, ageing and cancer due to exposure to the sun’s UV rays, it’s essential that employers in sectors like construction and agriculture create a working environment where sun safety precautions become the norm, rather than the exception.
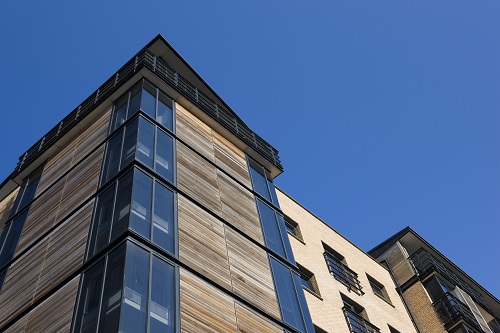
2025 UK fire safety regulation updates: a quick guide
By Chloe Miller on 11 July 2025
The regulatory landscape covering fire safety arrangements and structural features in domestic and commercial buildings has undergone a number of significant changes in recent years, making it essential for responsible persons to review their approach to keeping residents, workers and the nearby public safe from the risk of fire.
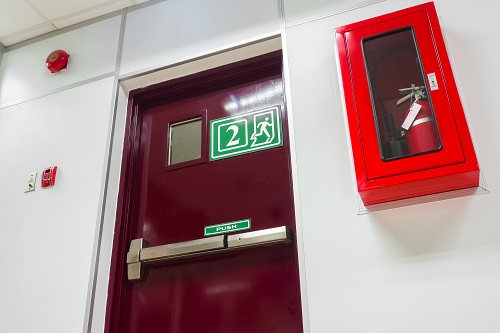
Tackling new fire risks as Fire Door Safety Week celebrates 12th year
By Helen Hewitt, British Woodworking Federation on 11 July 2025
The British Woodworking Federation’s annual Fire Door Safety Week this September will encourage duty holders such as those in charge of residential buildings to consider the dangers from lithium-ion batteries and ensure fire doors remain fit for purpose in reducing the risk should a battery-related fire break out.